By Karen Hanna
At a recent trade show, the Absolute Group of Companies attracted a lot of attention with an unusual stimulus — the smell of burning wood, which drew the fire department over for an inspection.
But there was no reason for alarm — the injection molding machine (IMM) maker was producing parts from a wood-based material.
While the company’s machines can run biobased materials, users are still in for a new experience. According to representatives of the Absolute Group and other makers of injection molding, extrusion and blow molding equipment, traditional machinery is up to the task — but users might need to adapt.
“It’s still kind of R&D land,” said Ben Hartigan, marketing coordinator for the Absolute Group.
Michael Sansoucy, VP of sales and turnkey systems at Arburg Inc., echoed the sentiments of many of his competitors when he said his company’s machines can accommodate a wide range of materials.
“If you can melt it and inject it,” he said, “we can mold it.”
Going with the flow
Representatives of IMM makers say processors often need to make only slight modifications to run biomaterials.
“No matter what, you’re still using pretty much a normal machine,” said Joe Kendzulak, the executive technical adviser and GM of Nissei America.
Marko Koorneef, president of Boy Machines Inc., agreed.
“As long as the material was of an injection moldable grade, we have not had to modify our machines for processing purposes,” he said.
Challenges related to biomaterials might be familiar to processors working with another problematic material — recycled plastics. Depending on the material, it might be particularly gummy, heat-sensitive or corrosive. Other variables to consider can include moisture and screw geometry.
Users of both biomaterials and recycled plastics can benefit from technologies developed to help monitor and compensate for process variations, OEM representatives say.
“The biggest issue with biomaterials is inconsistency," Sansoucy said. “We’ve had 50 years, 40 years, whatever, to develop polypropylene, as an example, and really optimize it and make the manufacturing process so I can get very consistent viscosity. And on the bio side, it’s brand-new, so we’re still learning how to do that.”
Biopolymers can be especially sensitive to shear, temperature and pressure, said KraussMaffei process engineer Lauryn Burdette, who spoke about the issue in a recent webinar hosted by Plastics Machinery & Manufacturing (PMM).
“I think the biggest challenge that we see with processing with biopolymers is that they really tend to be temperature-sensitive, so it’s very critical for us when we’re designing the process section and screw design, in particular, to make sure that we don’t degrade that material,” she said.
Particularly challenging materials include polycaprolactone (PCL), polyesteramide (PEA), polybutylene adipate coterephthalate (PBAT) and polybutylene succinate (PBS), according to Joo-hyeong Jeon, a senior research engineer for LS Mtron.
Molding tips
At NPE2024, Nissei’s swag demonstrated the company’s success in running biomaterials, despite challenges involving viscosity and other issues.
Proprietary equipment blended wood flour and polylactic acid (PLA) — Nissei makes its own material in Japan — before feeding it into an FNX180Ⅳ-36A hybrid IMM, which molded spoons, forks and knives. Meanwhile, an all-electric NEX80Ⅴ-9E IMM, equipped with Nissei’s K-Sapli low-pressure molding system, made marine-biodegradable combs from poly(3-hydroxybutyrate-co-3-hydroxyvalerate), also known as PHBV.
When molded, the teeth of a comb can web together, but Nissei’s equipment proved equal to the challenge — even though PHBV, a plant-based material derived from corn or cassava, is particularly prone to flash, due to the material's fluidity.
One remedy Nissei has explored involves using MuCell gas technologies, Kendzulak explained, “so we could change the fluidity of the material.”
LS Mtron and Sodick have gone that route, too, representatives for the companies said.
In processing PLA, which is especially susceptible to moisture, for example, Jeon recommends using nitrogen.
The material has a low melting point of around 300 degrees Fahrenheit and must be heated and cooled carefully, to avoid making it brittle.
“In some cases, to improve the low flowability of eco-friendly new materials, gases like nitrogen or carbon dioxide are pressurized to a supercritical state and fed into the barrel during plasticization to improve material flowability and address appearance issues with Rapid Heat Cycle Molding (RHCM) technology,” Jeon said in an email.
Designed to separate plasticizing from injection, Sodick machines are especially adept at handling gummy, high-viscosity materials like PLA, said Kohei Shinohara, senior VP for Sodick-Plustech, which supplies the IMMs. Sodick machines can even make thin-walled parts with the materials.
With Sodick’s Infilt-V technology, processors can increase material flow rate and reduce the volume of material needed to create parts, using nitrogen or carbon dioxide.
The process doesn’t require the high pressures of comparable technologies, so it’s easier and safer, Shinohara said.
“With this unique design, we can introduce the gas at the injection plunger, so that makes it easier to mix the gas without using high pressure in our gas. ... We create the high-pressure environment by compressing the resin by the injection plunger,” he said.
Effective with many materials, including PLA, the technology is useful for lightweighting parts, or “pushing [the] limit for thinner-wall sections ... without the warp or without deformation of the finished products,” Shinohara said.
Sodick machines must be specifically built to perform the process, but machines designed to perform the process also can be used in applications that don’t require it.
Meanwhile, Arburg has in-house technologies Sansoucy recommends for “material that’s got very big shifts in viscosity” — the company’s aXw Control ScrewPilot and aXw Control PressurePilot.
ScrewPilot — which is standard on Arburg’s electric and hybrid machines, and an option on its other IMMs — provides for precise positioning of the screw for stable mold filling.
“What ScrewPilot is saying is that we’re going to control that screw motion ... if it’s hydraulic, we’re going to throttle the oil that goes back to the tank and slow that screw down, and if it’s electric, we have the advantage of it being coupled together, but it’s going to adapt to the melt front that it’s seeing,” Sansoucy said. “... The machines will automatically adjust ... because we’re scanning the injection parameters every half of a millisecond.”
PressurePilot — available as an option on all Arburg IMMs — provides optimized pressure control when switching from injection pressure to holding pressure. This expands the process window and leads to consistent mold filling and improved balancing, especially with high-cavity applications.
“We’re going to be more precise with how we look at that information out of the machine and make an adjustment accordingly,” Sansoucy said.
Bianca Gubi, product manager for the circular economy for Engel, and Kendzulak both indicated that processors of biobased materials might need to employ corrosion-resistant components.
To regulate injection volumes, Engel offers its iQ weight control, which, like competitors’ technologies, can help overcome the issues of processing all kinds of tricky materials.
“This ensures optimal part quality in injection molding, even with viscosity fluctuations in the bioplastic,” Gubi said.
She and Jeon drew distinctions between the challenges of molding non-biodegradable biomaterials vs. biodegradable plastics.
According to Gubi, non-biodegradable biomaterials, like bio-PE and bio-polyamide, can be processed just like their fossil-fuel-based counterparts.
But biobased and biodegradable plastics, such as PLA and wood-plastic composites (WPC) and other materials, can present challenges.
“In these cases,” Gubi said, “machine process conditions may need to be adjusted, such as lower temperatures, longer material pre-drying times and shorter melt residence times, due to the material’s sensitivity. If a very shear-sensitive biomaterial is used, we can employ a plasticizing screw that processes the material very gently.”
Jeon said biodegradable plastics have low thermal stability and a narrow processing temperature range, requiring precise temperature control during processing. He described LS Mtron’s efforts to overcome challenges:
“A variable-pitch screw with a long compression section was designed to accommodate these new materials, and the position of the thermocouple was optimized alongside the heater control logic through thermal analysis of the screw, barrel and heater. This ensures that the material does not receive excessive heat, reaches the optimal temperature and maintains it until the injection stage,” he said.
In addition to the processing challenges, Koorneef, of Boy, pointed out that material feeding — not molding — sometimes is difficult.
Finding extrusion’s sweet spot
In PMM’s “Taking the mystery out of processing bioplastics” webinar, Burdette outlined the challenges of running biomaterials — from feeding, mixing, removing volatiles and melting all the way through extrusion with a twin-screw machine.
“Both a volumetric and a gravimetric feeder, you’re going to have some amount of variation in your bulk density over time,” she said.
But gravimetric feeders can compensate for this variation, making them a better bet.
Just like her IMM counterparts, Burdette cited problems with biomaterial viscosity.
Some recommendations include adjusting the screw speed, increasing the size and number of pelletizing holes, and altering the screw design.
The modularity of KraussMaffei’s systems allows customers to tailor various elements to the application.
“So, we can change those elements depending on what the unit operation is, whether you’re feeding the material, whether you’re melting it, whether you’re venting, whether you’re mixing material in or pressure building," she said.
As an example of the challenges KraussMaffei has taken on, she discussed a customer that was trying to compound microorganism-derived, biodegradable poly(3-hydroxybutyrate-co-3-hydroxyhexanoate) (PHBH). The company was concerned about material that was being processed without being sufficiently melted; however, at higher temperatures, the material could degrade.
KraussMaffei worked with the customer to optimize the melt flow index. Among other modifications, it also increased screw speed to eliminate the risk of unmelted plastics emerging from the process.
Asked the biggest problem she’s experienced in material trials , Burdette responded in a way that other processors probably found relatable.
“The most disastrous thing that can happen when I’m processing a trial would be completely locking up the screw. And I have, unfortunately, done that quite a few times,” she said. “I’ve run a lot of trials over the years, and I have done that with biopolymers, and it can be very, very tricky with biopolymers. I’ve run some trials with some starch blends — starch and water — where, if you add too much shear, it becomes like a rock in the extruder. ... I would say, luckily, I’ve never had any issues where I’ve damaged any equipment, but I have had many trials where I’ve had to pull off barrel by barrel.”
Blow molding modifications
Like Nissei, Magic incorporated biomaterial in demonstrations at NPE.
At the show, Pietro Spiga, North America sales and marketing manager for Magic, recounted how the company worked with a California processor to adapt a ME T14-600-D extrusion blow molding (EBM) machine so it could handle polyhydroxyalkanoate (PHA).
According to a press release, the all-electric machine provides for stable and safe production, as well as consistent cycle times. Compared to a traditional hydraulic machine, it’s far more efficient.
“Ninety to 95 percent of the machine is standard,” Spiga said, “so, it’s the same machine that runs HDPE or extrusion PET. What was changed was on the components where we run the material.”
Modified components included the extruder barrel and screw, some inside parts of the head and parts of the mold plate.
“The mold that they have to run, they’re not cool, but they are warm, because this is a material that if you run with a cold mold like HDPE, you will not be able to remove [the part] from the mold. ... It crystallizes, so the material will stick on the mold,” he said.
Born to run
Whatever the material, machine supplier representatives say their companies are ready to put their machines to the test.
Helping customers with materials is just one of the services OEMs provide, their representatives say.
LS Mtron’s Jeon and Sansoucy, of Arburg, which has performed more than 20 trials in the U.S. and Germany involving biomaterials for customers, each stressed collaboration.
For example, one Sodick customer worked to be able to use PLA for tableware that can withstand heat. Normally, such products bow and bend once exposed to hot water — meaning they can’t be washed and reused.
However, the Sodick customer found a formala for making the tableware withstand hot water.
KraussMaffei’s PHBH compounding customer also was successful — and it’s scaled up.
“Following those trials, the customer made changes to their production machine, and they are successfully running these formulations on their lines now,” Burdette said.
Contact:
Absolute Group of Companies, Parma, Ohio, 216-452-1000, www.absolutehaitian.com
Arburg Inc., Rocky Hill, Conn., 860-667-6500, www.arburg.com
Association of Plastic Recyclers, Washington, D.C., www.plasticsrecycling.org
Boy Machines Inc., Exton, Pa., 610-363-9121, www.boymachines.com
Chemical and Polymer Market Consultants, https://chempmc.com
Engel Machinery Inc., York, Pa., 717-764-6818, www.engelglobal.com
European Bioplastics e.V., Berlin, 49-30-28482-350, www.european-bioplastics.org
KraussMaffei Corp., Florence, Ky., 859-283-0200, www.kraussmaffei.com
LS Mtron Injection Molding Machine USA, Duluth, Ga., 470-724-2263, www.lsinjection.com/us
Nissei America Inc., San Antonio, 714-693-3000, www.nisseiamerica.com
Magic North America, Whitmore Lake, Mich., 734-358-7722, www.magicnorthamerica.com
Sodick-Plustech, Elk Grove Village, Ill., 847-310-9000, www.sodick.com
Read more:
Biomaterials can be classified in three groups: biomass-based materials that are biodegradable; biomass-based materials that are not biodegradable; and fossil-based materials that are biodegradable.
More sophisticated applications and products are fueling production, according to a European Bioplastics report.
Biomaterials are drawing interest from the plastics industry, but supply so far is weak, driving up prices.
Products made from plant material from North Carolina company PlantSwitch have included straws, forks, knives, spoons, and cups; makeup containers, lipstick tubes, closures, and more; and bottles, bottle caps, toothbrushes and coffee pods.
Biobased innovations could bring circularity to the furniture industry.
Chemicals company BASF has announced it will begin producing ethyl acrylate for its methyl acrylate portfolio with 40 percent biobased content derived from grain sources. Eventually, it plans to phase out fossil-based ethyl acrylate production.
Karen Hanna | Senior Staff Reporter
Senior Staff Reporter Karen Hanna covers injection molding, molds and tooling, processors, workforce and other topics, and writes features including In Other Words and Problem Solved for Plastics Machinery & Manufacturing, Plastics Recycling and The Journal of Blow Molding. She has more than 15 years of experience in daily and magazine journalism.
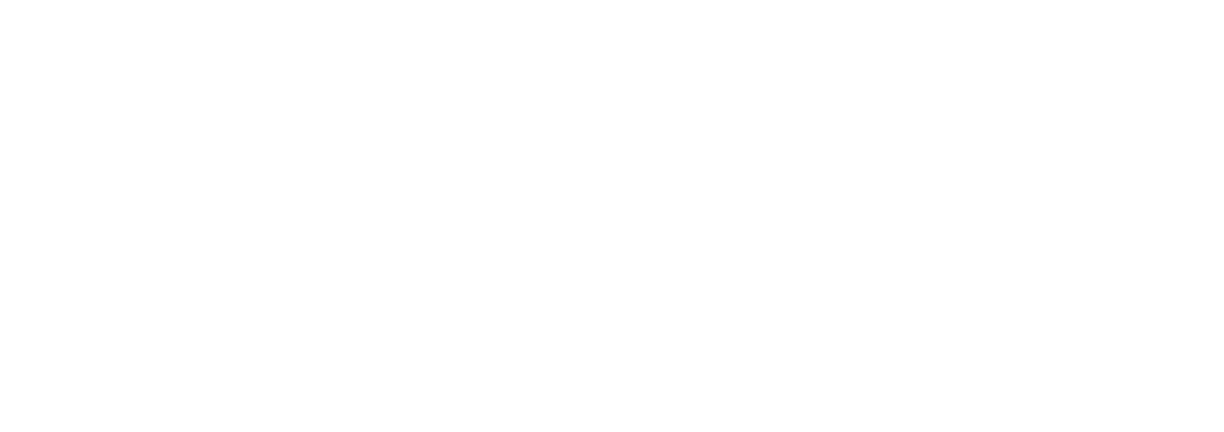