IMM makers integrate artificial intelligence to improve production
By Bruce Geiselman
A scarcity of skilled workers is helping fuel increased interest in both process monitoring and artificial intelligence (AI), according to several major manufacturers of injection molding machines (IMMs).
It’s common for plastics processors to run their operations with one worker overseeing multiple IMMs, and perhaps only one or two maintenance workers per shift. In addition, sometimes employees lack experience in injection molding. To help manufacturers, OEMs are trying to provide technology that fills in the knowledge gap.
Right now, about 50 percent of Wittmann’s clients are looking for AI technology, said Sonny Morneault, VP of sales for Wittmann USA. Larger companies, which tend to have more resources, are embracing the technologies at a higher rate. However, they aren’t the only ones showing interest.
“We do have some innovators, even the mom-and-pop side, that have the talent, that understand the benefits of it, and are trying to adopt it,” Morneault said.
Morneault and representatives of two other major IMM manufacturers — Engel and KraussMaffei — talked with Plastics Machinery & Manufacturing about their latest digital offerings and where they think the technology is headed.
Engel unveils new AI technology at K Show
At K2022, Engel demonstrated its new iQ hold control software, which is the latest member of the iQ product family and helps plastics processors determine optimum pressure holding time at the push of a button.
Pressure holding time is critical to producing quality parts and being able to optimize cycle time to boost productivity. However, determining the sealing point consumes time and raw material since processors have to mold several parts and analyze them in a quality-control lab. Engel’s new software removes the need for production workers to go through this process.
By analyzing mold breathing and screw position, iQ hold control can calculate the holding pressure time at the push of a button after only a few cycles. It works with Engel’s CC300 IMM control.
“Now, with hold control, you check a box on the machine, it basically runs through a few cycles, and then it’ll give you a suggestion on or an insight on how the machine can be optimized,” said Nicholas Suter, business development and digital solutions consultant at Engel.
The optimum holding pressure time as determined by the software typically is less than the pressure holding time initially set, reducing cycle times and energy consumption.
At the K Show, Engel ran the feature on an all-electric e-mac injection molding machine. The machine featured all of the smart assistance systems in the company’s inject 4.0 program, showing how they work together to optimize performance.
Other iQ products include Engel’s iQ process observer software, first demonstrated at K2019, which monitors process conditions and helps operators maximize the efficiency of Engel IMMs. The software, installed directly on the machine HMI, constantly monitors hundreds of process parameters and can detect drifts. It checks conditions against previous cycles and compares them to set parameters.
“The nice thing about the process observer is that it constantly watches the process,” Suter said. “It’s basically a set-it-and-forget-it tool. It’ll acknowledge when something is going wonky in your process, and then it will give you basically a stoplight indicator. You click on that stoplight, and it brings you to the exact parameter that is falling by the wayside. It saves you hours of troubleshooting.”
The iQ process observer software also offers operators insights on how to improve their process, he said.
“Another nice feature with the process observer is that it actually shows you the timeline of what happened,” Suter said. “You know what user made a change. It takes out that discovery phase or that big question mark.”
If you go into work and discover a machine went down, and you’re trying to figure out why it went down, iQ process observer offers insights, he said.
The demonstration model at K2022 also was equipped with iQ weight control, which detects fluctuation in the injection volume and material viscosity and automatically compensates for them within validated limits in the same cycle.
“This is what the iQ weight control is doing,” said Hannes Zach, sales director for Engel Digital Solutions. “It monitors the viscosity of the material and ensures that always the same shot volume is injected into the mold.”
This feature is particularly beneficial when using recycled material because it might have a different viscosity as compared to virgin material.
IQ clamp control, another AI product from Engel, allows injection molding equipment to “self-optimize” the clamping force, Suter said. The correct clamping force, which is normally difficult to determine, can result in energy savings, shorter cycle times and extended mold life.
“Generally, what users do is just set the highest clamping force that the machine can take,” Suter said. “What happens is that you use a lot more energy than what’s necessary; you have additional mold wear because of the additional clamping force, and there’s also strain on the components, so you lessen the life of the components that are needed for these movements.”
After a few reference cycles, the software can determine the optimum clamping pressure to ensure part quality without exerting more force than is required, he said. It’s not uncommon for plastics processors to cut their clamping force in half, he said.
“We found out that 30 percent of the injection molders use 100 percent of the clamping force,” Zach said. “So, this has a huge potential for energy savings and the protecting of molds.”
KraussMaffei’s socialProduction encompasses AI
KraussMaffei’s socialProduction is a mobile app and web application that combines the advantages of social media with up-to-date production monitoring technologies. Ranjith Pola, director of Digital Solutions and Controls at KraussMaffei USA, said it includes AI components.
The software uses information gathered from sensors installed on KraussMaffei IMMs to learn trends and normal operating parameters. Working autonomously, socialProduction detects deviations in the production process at an earlier stage than ever before, according to KraussMaffei.
“We use this intelligence or information that we have, and we create notifications to the users right before the machine goes into a breakdown,” Pola said. “That’s where we are working on what I would say is machine learning. Of course, that’s the level of intelligence that other process monitoring cannot provide.”
SocialProduction presents machine information in real time that can be viewed either on a mobile device using a smartphone app, or on a computer using a web application. Users can view either a summary of the condition of all machines or receive an in-depth look at the performance of individual IMMs.
SocialProduction consists of three components, and customers can use any or all of them. The first component is productionMonitor, which collects data about machine performance and can display that data to users.
The second component, processSupport, uses self-learning technologies to recognize normal operating parameters for a machine. If irregularities in the process develop, the software can proactively report those problems to users and offer detailed analysis of all available data.
Problems that might trigger a processSupport alert include anomalies in clamping force, injection pressure and plasticizing time. The alerts can be sent to a mobile device or desktop computer. Right now, process-
Support’s alerts notify users of anomalies but don’t identify the cause.
“In the future, our plan is that when we have the anomaly to also point the customer in the right direction to look at what might be causing this anomaly,” Pola said.
The liveCare component of socialProduction also involves AI and tracks the wear of machine components. It was introduced in the U.S. in July, Pola said.
It helps with the implementation of efficient, condition-based maintenance strategies and with determining the optimum service life of components, according to the company.
For example, liveCare reports on the condition of the nonreturn valve and the condition of the screw.
“This is based on already preinstalled sensors on the machine,” Pola said. “I’m stressing this because screw maintenance or barrel maintenance is where customers spend a lot of time. They really do not know what is happening inside the barrel until they see issues with the produced parts. They spend a lot of downtime to pull out the screw and examine it. Having this health information is very helpful to customers.”
LiveCare also can report on the efficiency of pump groups and identify when they might need maintenance to avoid unplanned downtime. The reports use color coding and percentages to indicate whether a component is in good or fair condition, or needs immediate attention.
Right now, socialProduction software and its components are available only for use with IMMs, but KraussMaffei hopes to expand its applications in the future.
“That’s in our development pipeline for extruders and the RPM [reaction process machinery] machines, but at present, it’s only for the injection molding [process],” Pola said.
The socialProduction monitoring application not only involves software, but also the installation of what KraussMaffei calls its smartCube, which is an edge device or local computer that also connects to the cloud. In the case of socialProduction, it connects with Amazon Web Services. Some of the collected data is stored locally, and some is analyzed in the cloud and transmitted back.
The technologies can help make production monitoring easy and efficient for the user while the intelligent algorithms do the work for them.
“Injection molding is a complex process with a lot of parameters at play to make a good part. Most often, the process fluctuations are unnoticed until a major breakdown occurs,” Pola said. “With little to no user configuration, using socialProduction, even a newbie can understand what’s happening inside the machine. That’s our main goal.”
Wittmann highlights Industry 4.0 technology
The Wittmann Group offers a variety of process monitoring and AI options to injection molding customers, Morneault said.
“Wittmann work cells perform AI machine learning,” Morneault said. “For example, with our HiQ Flow and CMS technology, we can predict and correct potential issues before they happen. The technology draws new conclusions from current parameters and thus becomes increasingly intelligent as it monitors performance, making changes on the fly … to create a closed-loop intelligent process.”
HiQ Flow software compensates for viscosity fluctuations in the material, which can be particularly important when processing alternative materials such as renewable and recycled materials, according to the company.
“With HiQ Flow, if you have different viscosities of material, if you’re running, let’s say, virgin material with 50 percent regrind, and that regrind varies in its properties, that changes the flow of the material once it’s melted into the barrel,” Morneault said. “The machine can then compensate the parameters required to produce a consistent good part and prevent short shots, overflow or other out-of-spec part conditions.”
During the injection phase, HiQ Flow measures the work required during injection to infer changes in viscosity. If it detects a change, the machine compensates by adjusting the holding pressure and switchover point to ensure part weight remains stable.
HiQ Flow software works in conjunction with other optional HiQ software from Wittmann, including HiQ Metering for active closing of the check valve, and HiQ Melt. HiQ Melt is used for good part/bad part separation depending upon the metering work required to turn the screw during recovery. If the metering work is outside of the known tolerance, the parts are discarded for that molding cycle.
Wittmann’s condition monitoring system (CMS) relies on sensors.
“Basically, there are a variety of sensors that are added to the machine that give us the ability to analyze a variety of different elements of the machine to do predictive maintenance,” Morneault said. “For instance, we have a sensor on the motor of the injection unit sensing vibration. If we start to sense a level of vibration that’s outside of a certain tolerance, we can flag the customer and say, ‘Your screw and barrel need to be maintained or changed.’ ”
A variety of sensors throughout the machine can monitor unusual vibrations in the hydraulic system, such as in the pump drive, and detect changes in electricity consumption and hydraulic pressure. The CMS also can monitor the condition of oil, including temperature, contamination and water content. The system also measures the “climate” conditions, including temperature, moisture and smoke, inside the electric cabinet. In addition, vibration sensors can measure the condition of the plasticizing/injection unit.
“The idea, obviously, is preventing downtime by using predictive measures to notify the user that there could potentially be an issue with the machine in the future to plan some predictive maintenance program now to address it,” Morneault said.
While Wittmann customers currently have the option of using CMS technology to monitor their own machines, a future option would give Wittmann personnel access to the information, Morneault said.
“We are planning to offer in the future CMS monitoring so that we can actually monitor a smart factory for the client, and we can actually schedule our service techs to go in and do the maintenance required for the customer, if a customer or client so wishes,” Morneault said. That service would be offered at an additional fee.
With employers experiencing a shortage of skilled workers and labor in general, demand for digital products, such as process monitoring and AI, is likely to continue to increase.
“I think that’s just the reality; that’s the way the environment is being pushed,” Morneault said. “Right now, the usual injection molder has one process technician for the whole shift. They have one operator running four or five or six machines at the same time, and they have one or two maintenance staff per shift. It’s just the nature of the economy and where things are going. I think that we, as a company, can offer assistance to minimize the requirements of human interaction.”
To run work cells that require minimal human interaction, manufacturers want to bring AI to not only primary equipment but also auxiliary equipment like dryers and blenders.
“There’s some functionality within some of our different devices like our blenders,” Morneault said. “For instance, if we’re running a blended batch with, let’s say, 80 percent virgin and 20 percent regrind, we do have control levels that say, ‘Once I run out of regrind, I sense that, and now I adopt the ingredients that I’m mixing to compensate for a shortage of regrind.’ ”
Natural language processing, involving the use of voice commands, is another AI technology Wittmann is exploring, Morneault said. At the K Show, the company demonstrated the technology, which is still under development. Morneault compared it to smartphone users giving directions to Siri, a voice-controlled personal assistant available on Apple devices.
“Siri then can manipulate what you’re asking and, in most cases, give you a result,” Morneault said. “We’re working toward creating an environment and machine work cell to do the same thing. We’ve demonstrated this once before. We’ve been working with it for several years now, where we’re creating voice recognition on the machine to create an environment that reduces the amount of potential error or user interaction with pushing buttons on the controller itself, where we can use voice commands to do certain things on the machine.”
Examples of possible commands are commands to open the mold, close the mold, move the ejector forward, end production, inject, etc., according to the company.
Challenges associated with natural language processing include getting the software to recognize an individual’s voice and different dialects and accents, Morneault said.
Bruce Geiselman, senior staff reporter
Contact:
Engel Machinery Inc., York, Pa., 717-764-6818, www.engelglobal.com
KraussMaffei Corp., Florence, Ky., 859-283-0200, www.kraussmaffei.com
Wittmann USA Inc., Torrington, Conn., 860-496-9603, www.wittmann-group.com
Bruce Geiselman
Senior Staff Reporter Bruce Geiselman covers extrusion, blow molding, additive manufacturing, automation and end markets including automotive and packaging. He also writes features, including In Other Words and Problem Solved, for Plastics Machinery & Manufacturing, Plastics Recycling and The Journal of Blow Molding. He has extensive experience in daily and magazine journalism.
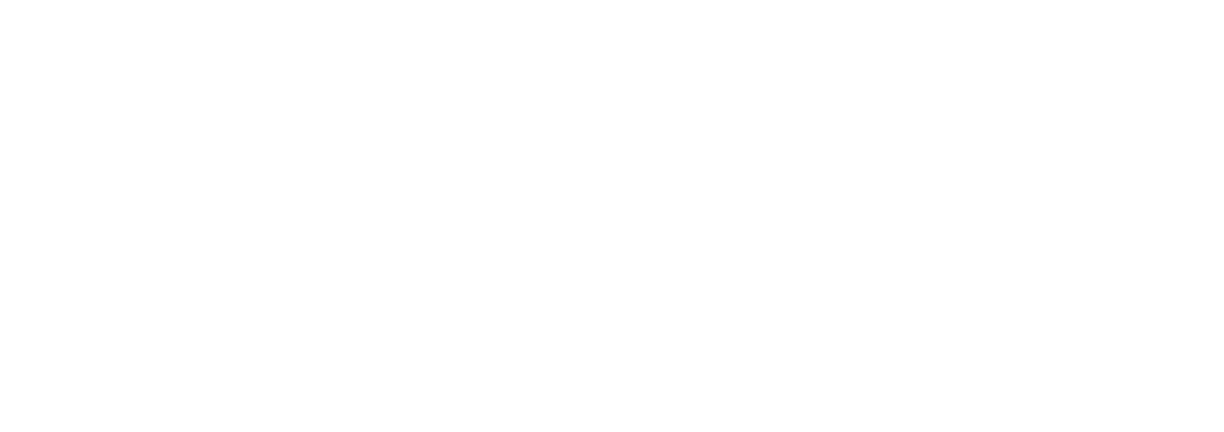