Smart technologies considered critical to manufacturers' success
By Bruce Geiselman
Companies, including plastics processors, that reject smart manufacturing technologies are putting their future at risk, said Alaa Elwany, an engineering professor at Texas A&M University in College Station. While the government mulls ways to help manufacturers unlock the potential of innovations like artificial intelligence (AI) and the use of digital twins, a study by Rockwell Automation uncovered growing interest in the technologies among business leaders.
“They are going to go out of business if they don’t adopt these technologies because others are going to adopt these technologies, and they are going to minimize the cost of their operations. They are going to improve the quality of their products using smart technologies. Then you will be put out of competition. It’s as simple as that,” said Elwany, whose background is in additive and smart manufacturing.
Elwany is currently a Science & Technology fellow with the Advanced Materials and Manufacturing Technologies Office of the U.S. Department of Energy (DOE), which is developing a national strategic smart manufacturing plan. At the direction of Congress, the DOE is examining how the government can encourage U.S. manufacturers to adopt smart manufacturing.
“We are leading the development, but we will involve other agencies from the federal government,” Elwany said. “We will involve industries, large and small. We will involve professional societies. We will involve subject matter experts, and then within a few months to a year, this national plan will be out.”
Smart manufacturing is a relatively new term that lacks a rigorous definition, he said. If you were to ask 10 people, you might get six definitions. The terminology is evolving, and it will eventually be standardized, but that hasn’t happened yet, he said.
Smart technologies include machine learning, AI, cloud computing, the use of digital twins and additive manufacturing. These technologies can support sustainability efforts and make manufacturers more efficient and improve manufacturing quality.
Certain manufacturing sectors have been quicker to adopt smart manufacturing technologies than others. Many traditional manufacturers, including many plastics processors, have been slower to adopt the technologies because they lack familiarity with them and are concerned about costs.
“There are manufacturing industries that were born smart, if you will, such as electric vehicle manufacturers,” Elwany said. “These are manufacturing processes that came out in the last decade — electric vehicle manufacturing, additive manufacturing and whatnot. These were born smart.”
He compared these industries to children born within the past few years who are raised with smartphones versus older generations who had to learn about the technology later in life.
“Now, there are industries that were not necessarily born smart, such as the automotive industry and the aviation industry, but they were quick to adopt smart technologies because it was straightforward for them to adopt. Then we have industries that are more traditional — casting, plastics, injection molding and the manufacturing industry in general. They were relatively slower than other industries in adopting them, but that is the nature of the thing. They were not born smart, and it was not so straightforward for them to adopt smart technology. So, the adoption happened a little slower.”
Adopting smart technology can be particularly challenging for small “mom-and-pop” businesses that lack a technology-savvy workforce and the budgets of larger manufacturers.
Elwany’s argument that smaller businesses in particular face challenges adopting cutting-edge technologies was reinforced in a report recently issued by the National Academies of Sciences, Engineering, and Medicine.
The report, “Options for a National Plan for Smart Manufacturing,” recommends that DOE and other government agencies support the development of smart manufacturing workforce training, a “cyber interstate” for real-time data sharing, and investments in critical technologies such as AI. The report recommends the government assist manufacturers by supporting new workforce education and training programs.
Technological advantages
Ultimately, businesses can benefit from adopting smart manufacturing technologies, according to both the report and Elwany.
“If you take injection molding plastic parts, you have all sorts of machine tools and equipment,” he said. “You have presses. You have dies. You have molds. When all these machines are equipped with sensors that can tell you what is happening in the manufacturing process itself, you can learn more about your process in real time. You can monitor different metrics that tell you how well your manufacturing process is going, and this is highly beneficial in reducing defects in your produced parts or increasing the quality and reducing the energy consumption of your overall smart factory. This is just one aspect of how the plastics or polymers industry can benefit from smart manufacturing.”
Another smart technology that can help plastics manufacturers is the use of digital twins, which are computer representations of a physical product or system. A plastics processor might create a digital twin of a specific machine or an entire production floor.
“For a digital twin to be really useful, it needs to be, No. 1, connected to the physical system that it represents,” Elwany said. “It can’t be static. It can’t be a snapshot of a system at a single point in time.”
A useful digital twin should be connected to the physical system through sensors that monitor machine performance under different conditions. Digital twins can be used, for example, to help refine a manufacturing process to improve efficiency.
“What you ultimately end up with is a very cheap way to run ‘what-if’ scenarios,” Elwany said.
If an injection molder finds its process is producing too many parts with defects, for example, it can run different scenarios — such as changing the process temperature or clamping force — and see a digital representation of what might happen in real life. By contrast, having an operator punching buttons on the injection molding machine to try different settings in real life would result in significant scrap and waste before the right solution could be found.
“But when you do it on the computer, it costs computational time, which is not cheap, but is orders of magnitude cheaper than doing it in reality,” he said.
Additive manufacturing is meant to complement but not replace traditional manufacturing technologies including metal casting and injection molding.
“It is meant to produce parts and features and materials that are not possible or are extremely expensive or time-consuming to produce using other processes,” he said.
3D printing of plastics and polymers is the largest use of 3D printing, by revenue — over the printing of other materials, such as metal. Among other products, the technologies produce end-use products for car components and heat shields used on NASA rockets, Elwany said. They’re also frequently used in low-volume manufacturing processes because they eliminate the costs of tooling.
Additive manufacturing can be used to produce parts with very complex geometries that cannot be produced using conventional processes.
Additive manufacturing also is frequently used in situations where products are produced in large quantities but require customization — such as hearing aids and shoes.
AI is simply the science and theory of producing computer systems that can conduct tasks historically thought to be possible only by humans, Elwany said. Examples of this are reasoning and decision-making that's based on reasoning.
“Simply put, artificial intelligence is a suite of tools and models that can take as input large amounts of data, very large amounts of data — we're talking gigabytes per second of data — that a human just cannot analyze by him or herself and make sense of the patterns,” Elwany said. “An example of this is data that you get from sensors.”
Computers can analyze the data to make predictions and decisions regarding the manufacturing process and equipment to optimize performance and support sustainability efforts.
The ultimate goal of smart manufacturing is to produce products with zero defects, Elwany said.
Worldwide, interest in smart manufacturing technology is growing, according to the recently released ninth annual “State of Smart Manufacturing Report” issued by Rockwell Automation.
The company surveyed more than 1,500 manufacturers around the world for its report. Two-thirds of the respondents worked for firms with more than $1 billion in revenue.
Among the key findings: 94 percent of respondents expect to maintain or grow their workforce because of smart manufacturing adoption, 9 percent are using or evaluating smart manufacturing technology (up from 84 percent in 2023), and 83 percent anticipate using generative AI (which can produce totally novel content including text, images, video, audio, computer code, synthetic data, workflows and models of physical objects). Generative AI is expected to be the No. 1 new area for technology investment over the next 12 months, according to the report.
The Rockwell Automation report concludes that the largest barriers to smart manufacturing adoption are costs, lack of skills to implement smart manufacturing technologies, and resistance among employees and company leadership to change.
Resources
Manufacturers can find additional information about starting or continuing their smart technology evolution through resources available online. Alaa Elwany, an engineering professor at Texas A&M University in College Station, who has a background in additive and smart manufacturing, recommends the following:
- www.nationalacademies.org/our-work/options-for-a-national-plan-for-smart-manufacturing — a workshop series (and report) published by the National Academies of Sciences, Engineering, and Medicine and sponsored by the U.S. Department of Energy (DOE)
- www.nist.gov/mep — information from the National Institute of Standards and Technology's website about the Manufacturing Extension Partnership (MEP) is a public-private partnership network for supporting small and medium-sized manufacturers
- www.cesmii.org/ — information from the Smart Manufacturing Institute, which is one of 17 institutes sponsored by the DOE in the National Network for Manufacturing Innovation (NNMI)
- https://cymanii.org/ — information from the Cybersecurity Manufacturing Innovation Institute, which is one of 17 institutes sponsored by the DOE in NNMI
Bruce Geiselman
Senior Staff Reporter Bruce Geiselman covers extrusion, blow molding, additive manufacturing, automation and end markets including automotive and packaging. He also writes features, including In Other Words and Problem Solved, for Plastics Machinery & Manufacturing, Plastics Recycling and The Journal of Blow Molding. He has extensive experience in daily and magazine journalism.
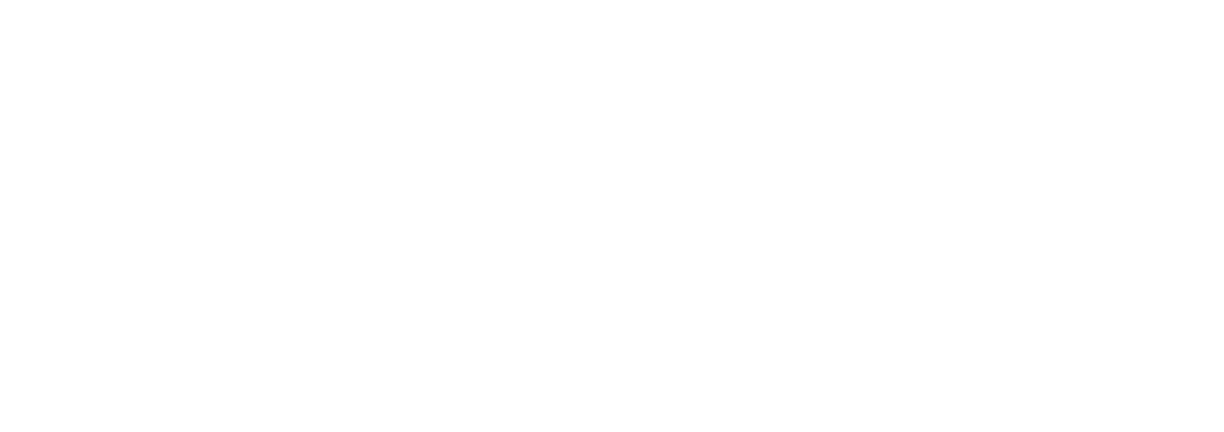