Getting Started with Lean, Part 4: Make information easy to see and share
By Rick Bohan
At this point, your workplace is clean and orderly. Everything has a marked and labeled home address. Teams are sustaining cleanliness and orderliness through daily tasks. Even new associates know where to find what they need to do their jobs and where to put it back when they’ve completed their tasks. All the tangible “stuff” in the plant has been sorted, shined and straightened.
Now we need to look at organizing and making visible all the intangible stuff in the workplace, i.e., information and performance data. There’s probably a variety of information on the shop floor already, everything from job descriptions tucked in a binder that’s buried in a desk drawer, to computer spreadsheets tucked away on hard drives, to monitors attached to the production machines.
There are problems with this information, though. Some of it is probably outdated (those job descriptions perhaps). Some of it is hard to get to unless you know just how and where to go (those computer spreadsheets).
And some of it is hard to understand, especially for that new associate on the second shift (the processing data on those equipment monitors). Information is available only to those willing to dig for it or those who have a high level of knowledge and expertise.
Effective visual management requires that information be easy to find, easy to see, and easy to understand by everyone on the shop floor. This doesn’t mean that you need to get rid of or replace those spreadsheets and hard-to-decipher monitors, but it does mean that you’ll probably need to add some simple tools for making information easy to see and easy to share.
That easy-to-find, easy-to-understand information will answer questions like:
- How is the plant performing this week/month/quarter?
- How is this department/team performing this week/today?
- What does our work plan look like today?
- Is our work ahead of schedule, on schedule, or behind schedule?
- Are we running into any problems or delays?
First, purchase a large dry-erase board. You can mount it on an available wall or buy one that can be moved, but it will need to be in a location that’s easy for associates to see. That might be an entry or exit passageway, the breakroom, or somewhere on the plant floor but, again, the location needs to be easily accessible and easily visible.
On this large dry-erase board, you will post and keep updated the following information:
- Monthly Plant Performance Metrics: These metrics should include safety, quality, delivery, customer satisfaction and employee engagement yardsticks. (SQDCE… You can remember this set of metrics with the acronym SQuare DanCE.) You’ll need to decide, specifically, what data you’ll use for each of these metrics. Most plants end up with about 10 metrics in total. You’ll produce a line chart for each of the metrics showing the plant’s performance during the past 12 months (at least) and post them on the large dry-erase board.
- Improvement Priorities: Post a list of improvement priorities and the actions being taken to address those priorities.
- Recognition: Post the names (and portraits, if possible) of those involved in present improvement activities or who have successfully completed improvements.
You’ll also mount a dry erase board in each work area or department. Operators will use these dry erase boards to make notes of problems they’ve run into or questions they have. You’ll add to the department dry erase boards a simple table like this one.
Each day, the operators will use the icons to indicate whether they had a good shift or not-so-good shift. You can adjust the design of the table to meet your own situation. For example, you might have more than one shift per day, so your chart might look like this:
All this is just a start to the project of making important information visible and easy to access. There is other information that you’ll want to organize:
- Machine settings/run settings
- Work instructions
- Production schedule
- Troubleshooting guides
- Quality standards
- Personnel schedule
With respect to these and other documents and info, it will be useful to pull your supervisors, lead technicians and operators together and discuss questions like these:
- Do we have this information now? If so, is it up to date? Where is it kept? Where should it be kept? Can we make it easier to find, easier to see, easier to understand?
- If we don’t have the information now, what’s our plan for pulling it together or creating it?
This probably seems like a lot of work, and it is. But the payoff will come in reduced indirect time, errors and delays.
Rick Bohan is founder and CEO of Chagrin River Consulting in Akron, Ohio.
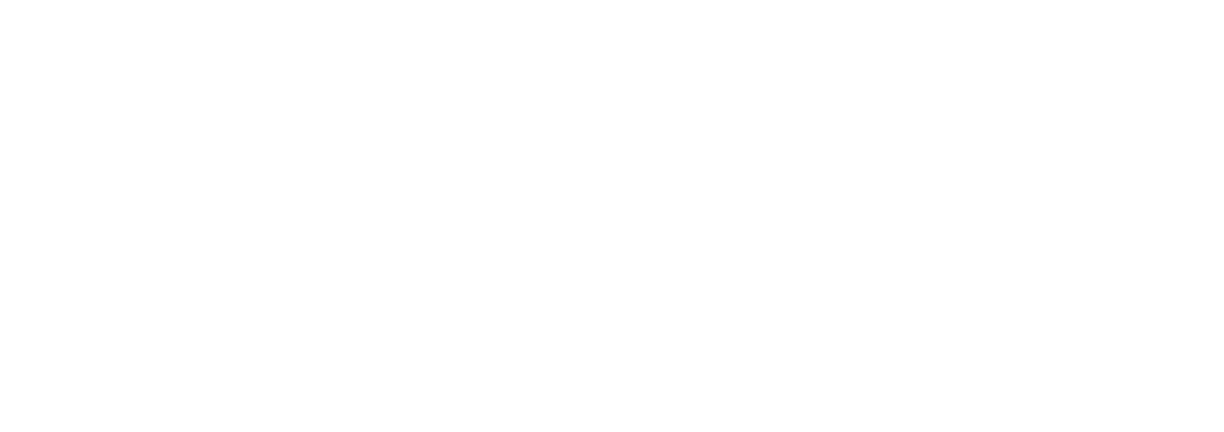