By Bruce Geiselman
Kawasaki Robotics partnered with system integrators and a local distributor to demonstrate two automation applications developed for the company’s robots at the ATX West show in Anaheim, Calif., in February. ATX West was co-located with the Plastec West show.
As manufacturing costs increase and legacy production processes become obsolete, robot automation is integral to any manufacturing strategy as it boosts production efficiencies, reduces material waste and increases throughput, Kawasaki Robotics stated in its announcement of the demonstration partnerships.
One work cell at Kawasaki’s booth demonstrated automated assembly of final parts with a robotic screwdriver. The cell recently was developed for a customer by Provoast Automation, a distributor of Kawasaki robots in Arizona, New Mexico, southern California and Baja California, Mexico. Provoast worked with CESAT Manufacture Solutions, a robot integrator based in Tijuana, Mexico.
While screw fastening is a standard method in assembly processes, slight changes to the process can significantly impact assembly accuracy, according to Kawasaki. Automating the process ensures repeatability, accuracy and traceability of data to ensure quality assembly that meets the customer’s specifications. It also is faster than manual assembly.
Kawasaki Robotics and its partners demonstrated a work cell using a Kawasaki RS007N six-axis robot, which has a maximum payload of 15.4 pounds, equipped with a screwdriver end-of-arm tool (EOAT). The hardware and software package measures torque and screw revolutions to ensure screws are properly tightened without overtightening and stripping the screws or cracking plastic parts.
A green light on the EOAT and a message that reads “pass” in green illuminates on the work cell’s HMI when the screw completes the fastening operation. The driver provides real-time feedback on torque and screw driving status to ensure proper fastening. However, in the event of an error, a red light on the EOAT and a red message on the HMI signals a failure. The data is recorded and stored to verify for both the plastics processor and its customers that all screws were installed to the correct specifications.
“It eliminates the human error possibility to ensure screws aren’t stripped or not properly tightened,” said Ron Mayhew, VP of Provoast Automation, who demonstrated the work cell.
Sumake Industrial Co. Ltd., headquartered in Taiwan, manufactured the electric screwdriver EOAT and the screw feeder used in the cell.
TransAutomation Technologies, a robotic systems provider and conveyor manufacturer in Southern California, developed a second work cell at Kawasaki Robotics’ ATX booth. The company is a preferred integrator for Kawasaki Robotics.
The palletizing/depalletizing work cell featured a Kawasaki RS080N six-axis robot, which has a maximum payload of 176 pounds, equipped with a vacuum gripper EOAT from Joulin, based in Hickory, N.C. It handled 20-pound boxes.
The demonstration cell included a conveyor system with four conveyor lines feeding two pallet locations.
“It could easily have four pallet locations, but due to size [limitations at a trade show], we’re not doing that,” TransAutomation CEO John Thompson said. “But we’re trying to show the flexibility of having more than just one line coming into a palletizer; we could have four different products palletizing in different positions.”
While the demonstration work cell displayed the RS080N robot, TransAutomation offers the palletizing/depalletizing package using Kawasaki robots with payloads up to 661 pounds, Thompson said. The systems are easy to deploy, can be set up in one day and have a small footprint.
TransAutomation offers palletizing packages to customers nationwide, Thompson said.
Contact information:
Kawasaki Robotics (USA) Inc., Wixom, Mich., 248-446-4100, www.kawasakirobotics.com
Provoast Automation, Anaheim, Calif., 714-996-9417, www.proautocon.com
TransAutomation Technologies, Irvine, Calif., 714.881.4988, www.transautotech.com
Bruce Geiselman
Senior Staff Reporter Bruce Geiselman covers extrusion, blow molding, additive manufacturing, automation and end markets including automotive and packaging. He also writes features, including In Other Words and Problem Solved, for Plastics Machinery & Manufacturing, Plastics Recycling and The Journal of Blow Molding. He has extensive experience in daily and magazine journalism.
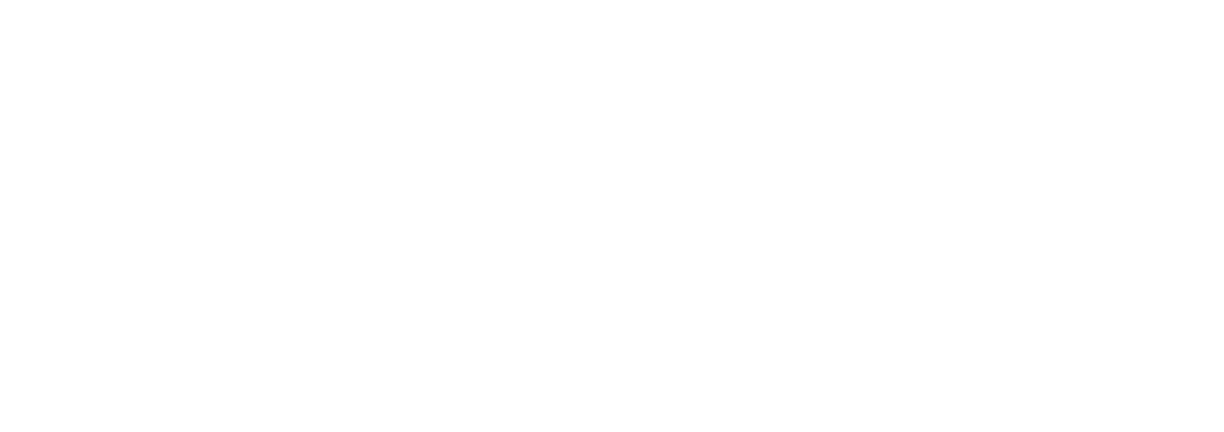