Manufacturing leaders must make plastics plants more sustainable: Talking Points
By Ron Shinn
We operate plastics processing plants to make a profit and not to save the world. But it is becoming clear that it makes good and necessary sense for manufacturing to take the lead in fixing climate change.
Plastics are under far more scrutiny than most other manufacturing sectors. From creating resin to emissions from automobiles that have plastic fenders, we take more blame for ruining the environment than most other sectors.
The president and CEO of the Volvo Group, speaking at a World Economic Forum conference, said that manufacturing accounts for 23 percent of direct carbon emissions in the U.S. and is one of the largest emitters of greenhouse gases in Europe.
“Sweeping changes need to be made across every aspect of manufacturing if we are to collectively transform our operations and products and future-proof business growth,” Volvo’s Martin Lundstedt said.
Plastics processors cannot do much about emissions from the day-to-day use of end products, but the emissions that come from manufacturing and transporting the plastic components and parts they make are important and can be controlled.
Whether you are running a business to pass along to the next generation of your family or you plan to sell it when you retire, spending time now to think about something bigger than reducing cycle time will pay off.
Thinking about fixing the climate is daunting and it is easy to say it is a bigger problem than my plant. But it is likely you have already taken some first steps.
Digital technology is giving us a head start. The implementation of lean processes using digital technology is starting to change our factories. Lean processing makes us more efficient, increases productivity, reduces costs and creates a safer workplace.
Deloitte’s Vincent Rutgers, writing in Forbes, said that “automation through digital technology can also provide manufacturers greater visibility into their production process, equipment wear-and-tear, and, more importantly, energy usage. Armed with this data, organizations can then optimize production and improve predictive maintenance to diminish energy loads as well as reduce material and water waste — all key factors in building sustainability.”
But that is not enough.
Going forward, it is important to take giant steps to use more sustainable energy such as on-site generation, solar panels, wind turbines and geothermal systems. Reducing waste and water usage and efficiently using energy also are key components.
Saving the planet is important, but processing software company SAP lists six direct benefits from sustainable manufacturing practices:
- Address growing consumer trends. A recent survey of Gen Z consumers found that 73 percent said they are willing to pay more for a sustainable product.
- Nurture brand equity. The rise of online shopping has led to a drop in brand loyalty. This means that businesses benefit from building unique, verifiable brand attributes such as sustainability and ethical values, according to SAP.
- Benefit from subsidies. Some companies can win financial subsidies from governments by demonstrating green initiatives.
- Be more attractive to investors. A company’s commitment to sustainable and responsible practices projects an image of success and reduces investment risk.
- Be more attractive to job seekers. Another Deloitte survey found that 49 percent of Gen Z respondents said that a prospective employer’s values played a major role in whether they would accept a job offer.
- Save money and cut costs. The reduction of waste and the ability to make more efficient use of resources and energy speaks directly to a business’ bottom line.
Making the factory floor more efficient and getting every employee to buy into sustainable manufacturing takes bigger thinking and can only be achieved by setting the right tone at the top.
Your 2024 capital expenditures budget is probably already published, but it is important to think about sustainability when you decide which processing machine, dryer or robot to buy.
Many of you will be at the NPE show in May in Orlando, and some of the most notable changes since the 2018 show will be improvements in equipment to make processing more sustainable. In 2018, the concept of the circular economy was something Europeans worried about but wasn’t as big a concern here. Processing machines could not make on-the-fly adjustments without human intervention, and some processing data was being collected, but little was being analyzed and used.
Times have changed. Every plastics processing plant needs to have sustainability in its decision-making process, and machinery makers are helping make that possible.
Ron Shinn | Editor
Editor Ron Shinn is a co-founder of Plastics Machinery & Manufacturing and has been covering the plastics industry for more than 35 years. He leads the editorial team, directs coverage and sets the editorial calendar. He also writes features, including the Talking Points column and On the Factory Floor, and covers recycling and sustainability for PMM and Plastics Recycling.
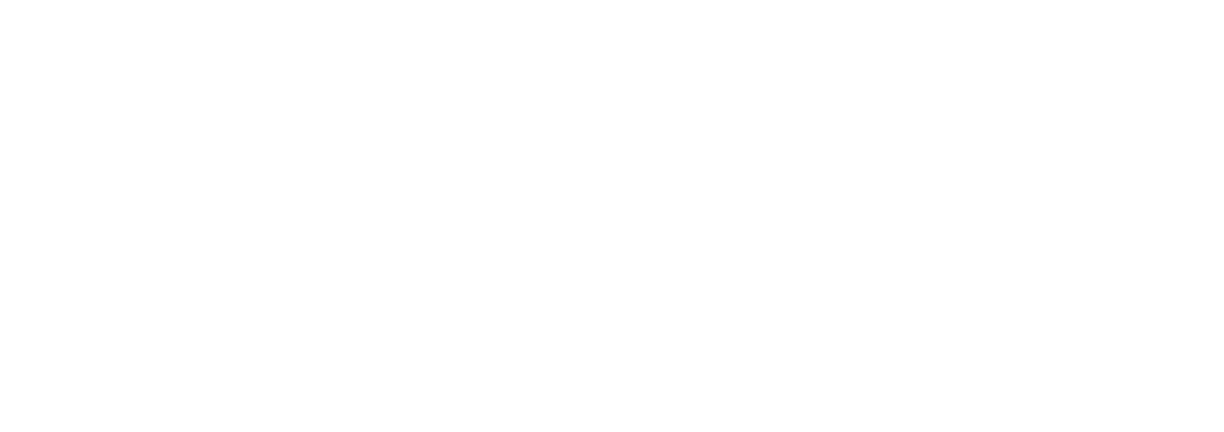