By Rick Bohan
Is your plant spotless? No electric cords or air hoses on the floor? No dirt or grease on any machinery, motors, or operator panels? No trash, debris, obsolete or broken parts or materials anywhere?
If so, you’re ready for the next step, Straighten and See. This is the phase during which you’ll apply visual factory methods. In simple terms, Straighten and See involves identifying a location for everything in the work area, then marking or labeling that location. (Along the way, we’ll add some new things to the work area, but we’ll get to that in our next article.)
The Straighten and See phase will be more work and will take more thought and planning than the Sort and Shine phase did. First, everyone in the work area needs to be part of the discussion as to where everything will go. Second, it’s likely that some financial investment will be required; shelves, cabinets, work desks, tool chests, shadow boards, label makers and signage will probably need to be purchased. Third, all the new labels, markings, storage, and signage need to be installed.
Finally, everyone in the work area will need to discuss and document any new standard procedures that the new Straighten and See tools require. (We’ll get to that in a later article that will address the Standardize and Sustain phase.) All of this takes a strong commitment of time, patience and persistence to accomplish.
Why Straighten and See?
Before we actually start making labels and putting down floor tape to designate walkways and placement of product, let’s take a step (or two) back to talk about why we’re going to all this trouble in the first place.
Take a quick look at your shop floor right now. Is it immediately evident where all the tooling, tools, supplies and materials your operators need are kept? If you had to find a pair of vise grips, or a crescent wrench, or a rubber mallet, or safety glasses, or a broom and dustpan, could you do so quickly? Can you lay your eyes on the tooling for the next run for each of your machines right away? Can you look at all the work in process and immediately identify what order it belongs to and whether it’s “on schedule” or not? Can you immediately differentiate scrap from good product within the manufacturing process? Are you able to tell right away if you have enough (or too much) raw materials, finished goods and consumable maintenance parts on hand?
An answer of “no” or “I’m not sure” to any of these questions means that neither you nor others can tell for certain whether the manufacturing process is in control or not. That, in turn, means that problems could arise that no one will be aware of until they become really big problems. Tooling that can’t be readily located disrupts the production schedule. When tools and materials can’t be readily located, changeovers and production runs take longer than they should. When WIP can’t be located easily, production is slowed and, in the worst cases, an order might be run again to be certain a promised ship date is met. A smoking gearbox can become an inferno if fire extinguishers can’t be located within seconds.
These and many other problems are avoided or, at least, caught at an early stage by shops that have implemented Straighten and See. Waste is reduced or eliminated altogether by a good implementation of visual factory techniques.
Let’s get started!
First, get everyone in each work area together and have them draw a map that shows where everything in the area will go. The map should indicate each machine, each storage unit (tool chest, cabinet, shelves, shadow boards), each work bench or table in the area. The map should also show where pedestrian and forklift travel ways will be. Finally, locations for work in process, scrap and finished goods should be designated on the map.
You’ll also want to list all the items that will be kept in each storage unit. If the map shows a set of shelves, list the items that will be stored on those shelves. Do the same for any shadow board, tool chest or cabinet shown on the map.
Next, have the team put together a list of materials, tools and supplies that will be needed to get the area in shape. Will new shelves, cabinets or other storage be needed? Materials for shadow boards? Foam or plywood that will have cutouts for tools and be placed into toolbox drawers? New tools or supplies of some sort?
Almost certainly the team will need a label maker and label material and floor tape to provide all the necessary visual cues. Make sure that a small dry erase board (2’ X 3’ or so) and a large dry erase board (4’ X 8’ or larger) are on the team’s list as well. (I’ll talk more about these in our next article.)
When the team has completed its list of materials, take it to purchasing with instructions to acquire all the resources.
In the meantime…
There are several things to do while waiting for all the materials to arrive.
First, make certain that Sort and Shine is being sustained. A good way to do this is to post a list of Sort and Shine duties that are to be carried out each shift. Have each shift check off those duties as they are completed.
Second, direct the team to move or place everything where it will go according to the map. (This is the Straighten part of Straighten and See.) The teams might be waiting for cabinets or toolboxes to arrive or shadow boards to be fabricated, but organize as best you can with what you have.
Pulling it all together
As the needed resources are arriving, the team will get active in putting everything together to create a visual workplace. Place any new storage according to its location on the map. Make and install the new shadow boards. Install floor tape to indicate where raw materials, work in process, scrap, or finished product will be located.
(Why not paint the floor rather than using floor tape? Well, you can, but I recommend using floor tape first. That gives you a chance to move things around later if you decide that the original map needs to be changed. Once you’ve painted the floor, it’s pretty hard to make changes.)
Make sure everything in the area, all tools, tooling and supplies have a marked and labeled home address. This means that cabinets, shelves, work benches, toolboxes, shadow boards, bins, and other storage need to be labeled. It’s better to “over-label,” at least initially. In other words, a cabinet should have a list on the door indicating the contents of the cabinet as well as labels on each shelf of the cabinet. The same is true of toolboxes and other storage.
The Straighten and See phase isn’t easy to accomplish but you’ll see that the investment of time and resources are worth it. You’ll find that morale goes up as workers find the workplace to be safer and less frustrating in which to work. In addition, you’ll find that quality and productivity improve as operators spend less time managing the confusion of a disorderly workplace and more time making the products that customers actually want.
There’s a bit more to do in the Straighten and See phase. In this article, we discussed how to organize things. In our next article, we’ll talk about an element of visual factory that’s just as important: organization information.
Rick Bohan is founder and CEO of Chagrin River Consulting in Akron, Ohio.
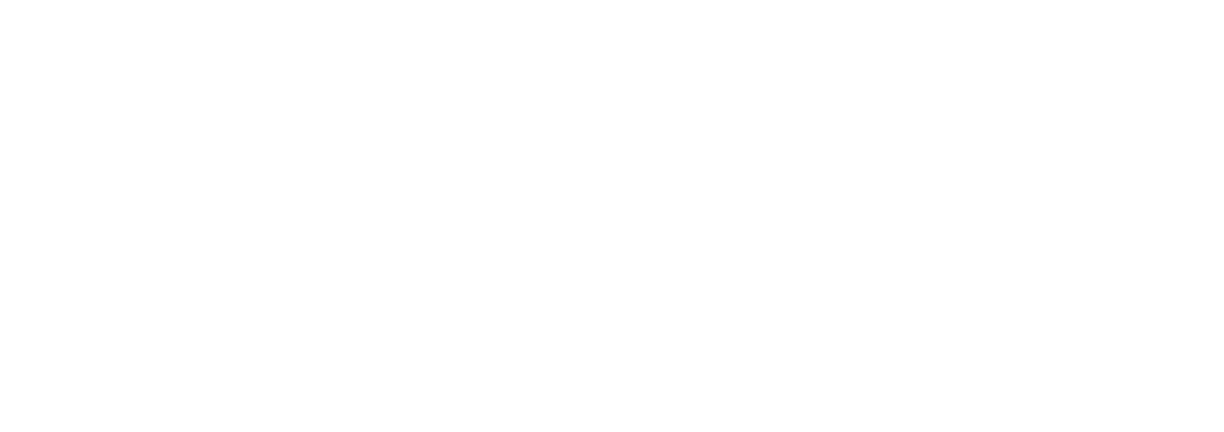