Good manufacturing leaders solve today’s problems but pay attention to things that could become problems later.
Here are a couple of things you might not be thinking about today, but should:
Managing your loose pellets. The American Chemistry Council and Plastics Industry Association (PLASTICS) launched Operation Clean Sweep in 1991, and today about 200 companies with slightly fewer than 600 manufacturing, resin production and distribution locations in the U.S. voluntarily participate. That’s out of more than 12,000 plastics manufacturing plants alone, according to PLASTICS.
I am no longer surprised when I step on loose pellets at a plastics processing plant. By now, every facility should be containing 100 percent of the pellets in their facility, but sadly, that is not yet the case.
Operation Clean Sweep starts with a pledge to manage resin to achieve zero loss. It is based on implementing resin loss programs that are generally inexpensive and easy to follow. The result is a cleaner, more efficient and safer manufacturing facility.
While it seems like a basic sort of program, it can go a long way toward preventing plastic from getting into sewers, lakes and oceans. It is a sign of good management. Having loose pellets in the environment also invites more government oversight.
The Operation Clean Sweep website is www.opcleansweep.org. It is a good place to start.
Understand what ESG means to you. ESG, which stands for a supplier’s environmental responsibility, social impact and corporate governance, can seem like an abstract concept, or at least something to worry about years from now. Don’t be fooled. Some of your customers are already thinking about it.
Processing machinery manufacturers also are paying attention. They all tout the energy efficiency of their injection molding machines, extruders and blow molders, and some have made significant changes to their own manufacturing plants so their operation has a better carbon footprint.
A couple of recent example include Chinese machinery maker Haitian publicly reporting its ESG impact for several years.
Environmental factors were a major consideration in the design and construction of two new KraussMaffei Group plants in Germany. KraussMaffei also has produced a handy lifecycleValueCalculator to help injection machinery users calculate their carbon dioxide emissions, energy consumption, scrap-related costs and lost revenue due to downtime.
Processors can impact their carbon footprint by using less energy, using more recycled resin and operating machinery more efficiently. Here is an idea: Write a report at the end of every year detailing what you have done to improve your ESG, then put the report in a file where you can find it when your customer or banker asks a question.
Get to know your data. Today’s processing machinery and auxiliary equipment, along with other control systems you might have in place, generate huge amounts of valuable data every cycle, every day.
Collecting the data is the easy part. But using it effectively requires effort. The payoff can be huge.
A captive molder with a plant full of the latest, most-sophisticated injection molding machines, once told me he was using about one-tenth of the machines’ capabilities and almost none of the data that was being or could be collected. He had a decent molding operation, but it could have been much better.
The starting point to improving how you use data is with your machinery and equipment sales people. They have a deep understanding of the capabilities of the machinery they sell and nearly always have a good idea of the strengths and weaknesses of your specific molding capabilities. They also have the advantage of going into many molding plants and seeing the good, better and best processing operations. Ask questions and get their advice about using the data.
Next, you need to tie everything together so key managers and supervisors have real-time information they can use to make data-driven decisions.
Overall Equipment Effectiveness (OEE) is the gold standard for measuring manufacturing productivity. It identifies the percentage of manufacturing time that is truly productive.
Google OEE to learn about the value of using the data you already have.
Get involved in protecting plastics. The industry is under assault as never before. What have you done to show your community that your plant is a good neighbor manufacturing essential products?
If your livelihood is based on the plastics industry, you have an obligation to defend it.
Make one or more of these points your New Years’ resolution for 2024. You won’t be sorry you did.
Ron Shinn | Editor
Editor Ron Shinn is a co-founder of Plastics Machinery & Manufacturing and has been covering the plastics industry for more than 35 years. He leads the editorial team, directs coverage and sets the editorial calendar. He also writes features, including the Talking Points column and On the Factory Floor, and covers recycling and sustainability for PMM and Plastics Recycling.
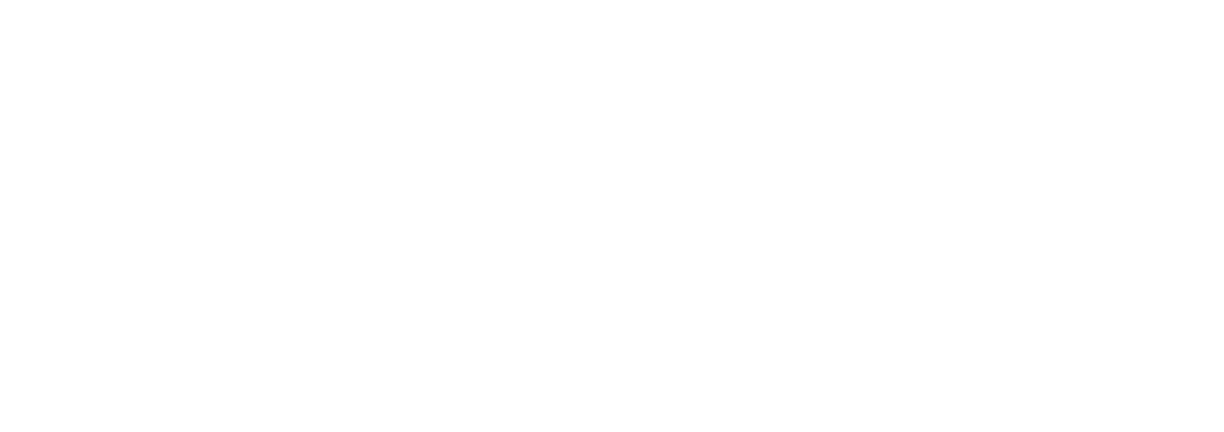