Husky helps boost plant efficiency with automation solutions
By Bruce Geiselman
Injection molders are facing multiple pain points, including a labor shortage, rising energy prices and pressures to increase recycled content in their products.
The solution to these challenges, at least in part, lies in increasing plant automation, according to Husky Technologies, which makes injection molding machines (IMMs), hot runners and molds.
Automation can perform work previously done by humans, increase energy efficiency and enable systems to better operate with the precision necessary when processing recycled materials. However, injection molders face difficulties in finding experts to help them design new plants or upgrade existing plants with state-of-the-art automation.
General contractors might not have the knowledge and experience to determine the specific needs of injection molding facilities.
“General contractors typically may not be aware of the details and specifications of a facility that is really focused on injection molding operations,” said Sean Golzarian, director of Advisory Services at Husky. “Injection molding is not necessarily their main field of expertise.”
Robot and automation companies can help, but they aren’t necessarily experts in injection molding and providing “near-lights-out” automation solutions from resin delivery to final product boxing and shipping.
Filling what it believes is a customer need, Husky’s Factory Planning Group advises food, beverage, consumer goods and medical device producers on automation solutions and building the most efficient injection molding plants.
It can provide services not only as an equipment supplier, but also as an engineering consultant and integrator.
“Factory Planning is really one of a suite of advisory services that Husky provides to help our customers improve their operational efficiencies, reduce their costs, improve the bottom line, and as a result, increase their enterprise value,” Golzarian said. “The group consists of very highly experienced individuals. … We’ve executed well over 500 projects globally in different markets. We’ve facilitated over 80 turnkey solutions for major brands in the water and CSD (carbonated soft drink) markets.”
Husky is a leading company in providing injection molding equipment and services to the food, beverage, consumer goods and medical markets.
The Factory Planning Group works with general contractors as an “extension of the general contractor’s team,” said Gianfranco Niso, business manager for the group. “We provide the best possible solutions for injection molding operations when it comes to the design of the building, the layout, the product flow, the supporting infrastructure such as resin-handling systems, power, compressed air, crane, and what have you. We book projects months in advance and are extremely busy with the demands that are coming our way.”
Husky provides its own IMMs and Shotscope 4.0 software for real-time and historical plant monitoring, and it collaborates with other companies to integrate equipment such as automated resin-handling systems, cranes, quality-monitoring systems, conveying systems, robots and automated guided vehicles (AGVs).
Niso and members of his team outlined for Plastics Machinery & Manufacturing how Husky can help customers automate their processes from the beginning of production to the end.
Automation begins with the delivery of plastic resin, which either is transferred directly from delivery trucks into silos or, when necessary, delivered in large bags.
Working with crane manufacturers, Husky has developed an automated system that can pick up two bags of resin at a time and discharge them into bunkers that feed into the storage silos. Instead of operators having to position cranes manually, they can push a button and the crane positions itself for discharge.
Using scanners and corresponding bar codes on the bags of resin and bunkers ensures that the proper resin is delivered into the proper silo. Husky’s proprietary Shotscope 4.0 plant-monitoring system enables resin-to-preform traceability. If the bar codes don’t match, the transfer of resin won’t take place. By handling two bags at a time instead of one and by preventing the wrong material from being discharged into a silo, the automation increases reliability and reduces the time it takes an operator to fill the silos, Niso said.
Along with other suppliers, Husky also offers an automated solution to reduce energy consumption. Molds typically need water chilled to 50 to 59 degrees Fahrenheit. Normally, that requires the use of energy-intensive chillers during hot summer months. However, in moderate climates with cold winters, more-energy-efficient free coolers mounted on a roof can supply water that’s cold enough for cooling the molds by means of a heat exchanger. The system can be designed to automatically make the changeover from chillers to the free coolers when the outside temperature drops below a certain level, Niso said.
“With this solution, it depends on the location, but we can reach energy savings of 30 percent to 40 percent,” Niso said.
While the majority of injection molding costs are tied to resin prices, energy prices also play a significant role.
“This is really significant,” Golzarian added. “When you look at the cost of a preform coming out of the injection molding operation, energy is a good part of preform costs. … So, any reduction in energy consumption is really a significant impact to the bottom line.”
In addition to the resin-handling systems, Husky has developed its automated Self-Cleaning Technology for molds. Dust tends to accumulate in IMM molds and can negatively affect product quality. While dust is a problem with all plastic resins, it is of special concern when dealing with recycled materials.
Normally, operators need to shut down an IMM periodically to manually clean the mold, which is often a tedious and time-consuming effort. However, using Husky’s optional Self-Cleaning Technology, converters can go up to 500,000 cycles before the need for manual cleaning, Niso said.
“The mold is going to clean itself at the touch of a button,” he said.
“That level of automation eliminates all that downtime and can gain a typical converter a considerable number of increased production hours per year,” Golzarian said. “Again, it’s a different level of automation. It’s not a product handling or typical automation that we have in mind when we talk about automation, but it’s really the elimination as much as possible of manual preventive maintenance, to automate it to the point that you gain a lot of production hours.”
Husky also has developed its Advantage+Elite “We Call You” service, a proactive, predictive, transparent, remote monitoring service. Advantage+Elite monitors the manufacturing operation in real time, allowing Husky experts to proactively observe and collaborate with on-site engineers to anticipate, recognize and rectify set-up and maintenance needs, maintain optimal production and energy usage, and enable the lowest cost of production.
Finally, working with AGV suppliers, Husky can offer automation at the end of the production process. AGVs can pick up empty boxes off a conveyor belt, take the boxes to be filled, and then return the filled boxes to another conveyor to be carried out of the molding area.
Husky is working toward allowing customers to develop a quasi-lights-out work environment where many functions are automated. It’s a focus of many employers as the costs of labor continue to rise, Niso said.
Bruce Geiselman, senior staff reporter
For more information on Husky’s Factory Planning Services, visit https://campaigns.husky.ca/advisory-services
Contact:
Husky Technologies, Bolton, Ontario, 905-951-5000, www.husky.co
Bruce Geiselman
Senior Staff Reporter Bruce Geiselman covers extrusion, blow molding, additive manufacturing, automation and end markets including automotive and packaging. He also writes features, including In Other Words and Problem Solved, for Plastics Machinery & Manufacturing, Plastics Recycling and The Journal of Blow Molding. He has extensive experience in daily and magazine journalism.
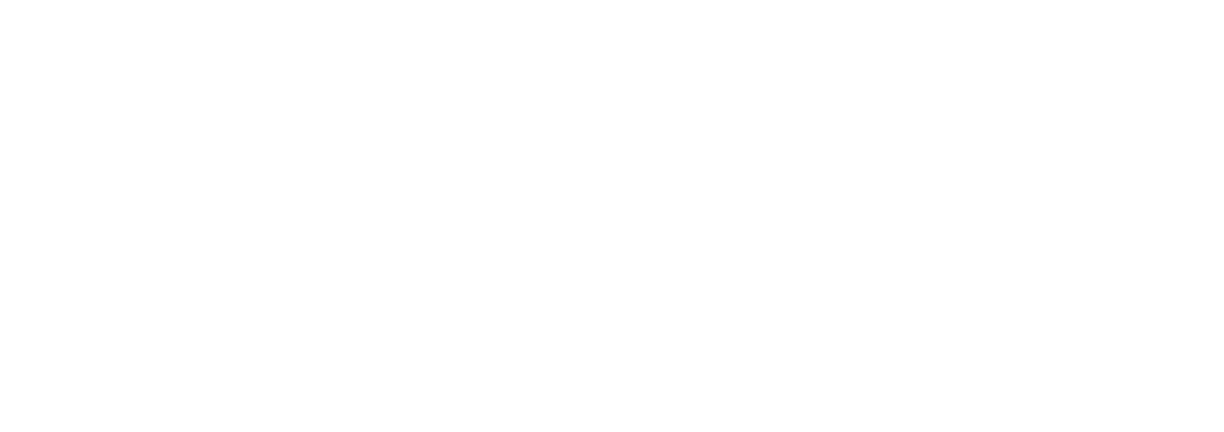