By Bruce Geiselman
Yaskawa’s new HC30PL collaborative robot (cobot) can handle a payload of up to 66 pounds, and the robot arm has a horizontal reach of about 5.5 feet radius from the base, which equates to an 11-foot diameter ring of reach, according to the company.
Yaskawa demonstrated the cobot in a palletizing configuration at Automate 2023 in Detroit. The demo used a 48-inch-tall riser to achieve an 88-inch stack height. Depending on package height and cell layout, the maximum stack height for the robot can range from 80-90 inches for a full-size pallet, but with smaller pallets, even taller stack heights can be achieved.
“It [the HC30PL] is specifically made for palletizing applications,” said Chris Caldwell, product engineer for Yasakawa America’s Motoman Robotics Division. “It has motion, acceleration, deceleration that are all optimized specifically to be used in high-speed industrial palletizing, but it is still a collaborative robot.”
It joins the 44-pound-payload HC20DTP and the 22-pound-payload HC10DTP in the HC (Human-Collaborative) series.
Yaskawa demonstrated, with the addition of Sick sensors, how the HC30PL can operate at industrial mode speeds when humans aren’t around. Once the sensors detected a human, the cobot at Automate slowed down and continued to slow as the human came closer. The demonstration had three speeds: industrial mode (or high speed), medium speed and low speed.
The cobot meets established safety standards to enable safe operation with or in close proximity to human workers, according to the company. Power- and force-limiting (PFL) technology constantly monitors force to quicky and safely react to contact, and advanced pinchless geometry provides additional safety.
“We see rates with this robot running in industrial mode of about 9.5 to 10 cases per minute,” Caldwell said. “You can run in industrial mode when you have other safety devices like the area scanners that we’re showing here. With those area scanners, you set it up in our FSU (Functional Safety Unit) so that as you approach the cell, it slows down and turns the power and force-limiting devices on to where it slows the robot down, and it will detect an impact.
“We have multiple zones, so it will slow down even more when you get closer, but we have it configured to automatically speed back up as you exit the cell. This allows you to keep as much production and throughput [as possible] in your palletizing cell, but to also keep it safe when humans are around. You can operate it with minimal guarding to minimize your footprint or with no guarding if you have enough safety equipment around it. You can also operate in PFL mode 100 percent of the time; you just have a lower throughput.”
“Basically, what we’re showing is there’s a variety of different ways you can program your Functional Safety Unit to get your application to be safe,” Caldwell said. “We have this set up that, if I went up there and put my hand through the light curtain, you’d have to go to the pendant to reset the cell. And we have the area scanners set to auto recover.”
Users of collaborative robots need to perform a risk assessment to determine how fast the units can move safely around humans.
“There isn’t one single speed limit that applies to collaborative robots,” Caldwell said. “It depends on what you’re lifting, how much it weighs, how sharp the corners are and what kind of pain it can cause. But typically, with palletizing applications, if you’re running it in collaborative mode, you’re looking at about 4.5 to five cases per minute. That’s why the industrial mode really speeds things up — you’re going to get that nine to 10 cases per minute.”
Hand-guided programming allows users to direct teach points without a pendant for quick deployment of the robot, and a plug-and-play tool flange connects a variety of end-of-arm tooling for fast and simple deployment, according to Yaskawa. The HC30PL is built with cast aluminum for industrial durability and has an IP67 rating that allows it to operate in damp or splash-prone environments.
The HC30PL is controlled by the YRC1000 controller and is compatible with either the standard teach pendant or Yaskawa’s more advanced Smart Pendant.
Users opting for the Smart Pendant can use Yaskawa’s new Pallet Builder Smart Pendant Software, which was demonstrated at Automate 2023. The software requires Smart Pendant V3.0 or newer, according to the company.
“It’s an ease-of-use software that lets people that don’t know robots and don’t know programming configure their palletizing cell and get something like this up and running,” Caldwell said. “If you’re a first-timer, you can deploy your robot and get it up and running in about two days, and if you’ve done it before, on Day 1, you’ll be up and running.”
The company introduced the software in March, Caldwell said. Pallet Builder Smart Pendant Software is compatible with GP-series and HC-series robots.
The HC30PL also is compatible with the compact YRC1000micro controller, which minimizes installation space.
Bruce Geiselman, senior staff reporter
Contact:
Yaskawa America Inc., Motoman Robotics Division, Miamisburg, Ohio,
937-847-6200, www.motoman.com
Bruce Geiselman
Senior Staff Reporter Bruce Geiselman covers extrusion, blow molding, additive manufacturing, automation and end markets including automotive and packaging. He also writes features, including In Other Words and Problem Solved, for Plastics Machinery & Manufacturing, Plastics Recycling and The Journal of Blow Molding. He has extensive experience in daily and magazine journalism.
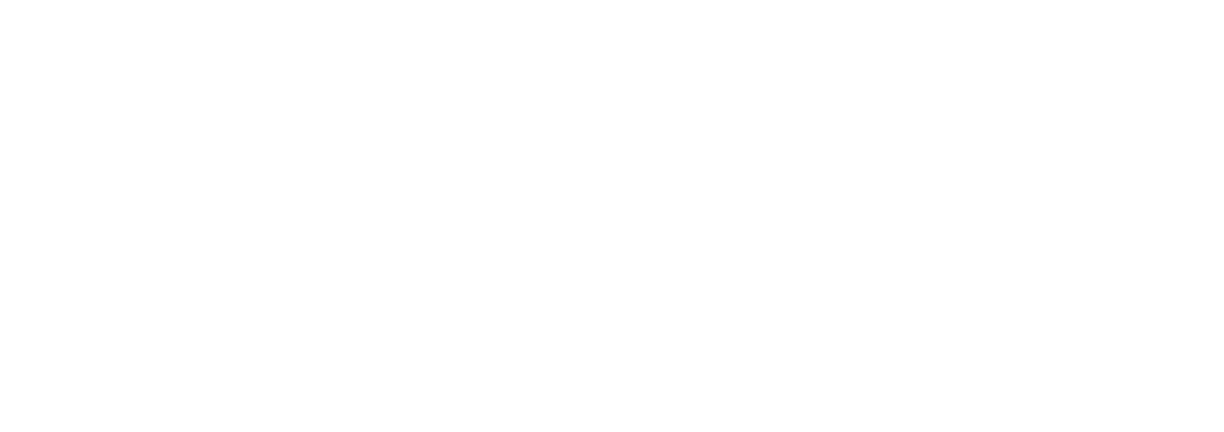