Government touts apprenticeship resources
By Karen Hanna
Its registered apprenticeship program is a selling point for customers of Engel, says Terri Fanz-Falzone, the company’s VP of HR for its North American operations.
But small plastics processing shops that are hurting for workers need not think apprenticeships are only for big companies. The option of starting a registered apprenticeship is open to everyone, said Cierra Mitchell, division director of the U.S. Department of Labor’s Office of Apprenticeship.
Companies intimidated by the thought of starting their own training programs have partners willing to lend a hand, she said. Setting up an apprenticeship program“There’s a lot of resources,” Mitchell said. “Our staff are one resource. This is what we’re paid to do, and we tell people, ‘Please, please reach out to us. And we’re here to help.’ ”
Nearly two years into starting the first of two new apprenticeships from scratch, Engel already is reaping some of the benefits, according to Fanz-Falzone.
The four-year programs are registered — meaning apprentices who complete it will earn credentials recognized throughout industry and across the country. Fanz-Falzone said that promise attracts a much deeper talent pool than programs developed in-house, without the help of agencies like Mitchell’s.
“Having the certified apprenticeship program has actually become part of our sales technique,” Fanz-Falzone said. “Our salesmen, when they go out to visit potential customers, they can show, ‘We have the certified program, and this is what we’re doing to ensure that your customer service will be top-notch, to ensure that, going into the future, four or five-10 years from now, if you have an issue with your machine and you need on-site service, we’re going to have people fully trained, ready and available to assist.’ ”
Extending a hand
The Office of Apprenticeship’s support for registered apprentices has topped $1 billion over the past eight years, Mitchell said. It runs the gamut — from the costs of providing educational opportunities to transportation and child care. The Department of Labor also has poured in funding.
And, for employers, the help is free.
“We work with them based on the current training that they have. And we not only help them create a program that works for them, but we help them launch that program, promote that program in their communities, so people are aware of it,” Mitchell said. “And we also help connect them to partners across the workforce system to help build that pipeline of talent in their organization.”
With more than 1,000 registered apprenticeships already in existence, budding professionals can find myriad opportunities, from making violins to managing bison herds. Plastic parts makers also have an array of choices, among programs with a number of relevant job titles, including plastics fabricator, mold maker, mold designer and extruder operator.
“We help them create a curriculum with structure and rigor so that they tell us exactly what competencies they want that apprentice to learn over the year, two-year timeframe that they want them to have that program for, and the employer leaves knowing, ‘This is what my apprentice will learn,’ and the apprentice knows, ‘This is what I learned throughout this program,’ ” Mitchell said.
Developing the program doesn’t need to take anywhere near as long as completing it. In fact, the range is anywhere from a couple days — if a suitable apprenticeship already exists — to several months, according to Mitchell. Her office can help companies identify partners that can provide funding or educational resources.
The programs offer flexibility for customization, and participating organizations can tweak standards to suit their own needs.
Mitchell pointed to recent experiences implementing programs for truck driving and cybersecurity — two fields identified by the government as national security priorities.
“We launched a 90-day trucking apprenticeship challenge in coordination with the White House, the Department of Transportation and industry, and, within 90 days working together, we were able to help to create over 100 registered apprenticeship programs for over 100 employers who are able to hire over 5,000 apprentices in just 90 days. We did a similar sprint for cybersecurity,” she said.
Clearing hurdles
Fanz-Falzone has started four programs at a series of companies, including her current employer. To employers like her company’s customers that might be considering starting a program, she offers this encouragement: “Don’t be afraid to jump in.”
“I think that there’s a lot of fear about how to start a program, so people don’t; it becomes overwhelming. The reality is, once you have a program up and running, it’s that first round that takes a lot of forethought, takes a lot of time; it takes a lot of energy. After that, it’s just … wash and repeat,” she said. “It’s very easy.”
With so many manufacturers scrambling to fill positions, she urged other companies to look at the big picture. Concerns about the costs of developing workers who might eventually wash out or take jobs elsewhere can become distractions from the role each company can take in rebuilding the workforce.
Apprenticeship programs can play a part in addressing the labor shortage, both Fanz-Falzone and Mitchell said.
“I think a lot of companies are afraid … ‘I’m going to put all this money into an apprenticeship program, and I’m going to wind up losing some of them.’ And that’s true; it’s absolutely going to happen,” Fanz-Falzone said. “But I always look at it as if we’re doing a program, and our next-door neighbor’s doing a program and their neighbor’s doing a program and all around the United States, if all of us in plastics are running an apprentice program, that just really makes us all more viable, more technically solvent. It just really elevates the entire level of what we can do here in the United States, makes us more attractive for businesses coming in from Europe.”
To find out more about how your company can benefit from or start an apprenticeship program, visit www.apprenticeship.gov/employers/express-interest-instructions.
Karen Hanna, senior staff reporter
Contact
Terri Fanz-Falzone, VP of HR, Engel North America, York, Pa.,
Tens of thousands benefit from registered apprenticeships
Average starting salary following apprenticeship graduation | 77,000 |
Employment retention rate | 93 percent |
Lifetime earning advantage over people who have not served apprenticeships | $300,000+ |
Active apprentices throughout 2021 | More than 80,000 |
New apprentices | 241,849 |
Total completers | 96,915 |
Active programs | 27,385 |
New programs | 2,879 |
Karen Hanna | Senior Staff Reporter
Senior Staff Reporter Karen Hanna covers injection molding, molds and tooling, processors, workforce and other topics, and writes features including In Other Words and Problem Solved for Plastics Machinery & Manufacturing, Plastics Recycling and The Journal of Blow Molding. She has more than 15 years of experience in daily and magazine journalism.
Request More Information
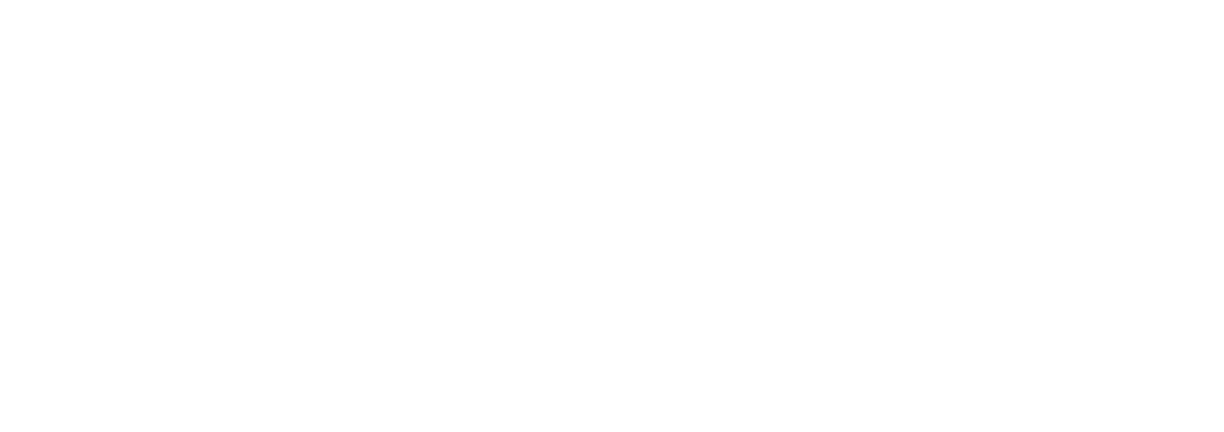