By Karen Hanna
With skilled workers at a premium, many experienced plastics professionals might be finding new tasks on their to-do lists.
But for Tim Forrest, a master field-service technician for Engel, which recently launched formal apprenticeship programs, the newest challenge is one he welcomes; he’s working to develop the next generation.
About a dozen apprentices have taken the first steps in their journey, by joining one of four cohorts launched by Engel beginning in July 2021. Focusing on either automation or field-service work, the four-year programs are registered by the U.S. Department of Labor, meaning participants will earn credentials that can be recognized industrywide.
Manufacturers are realizing the need for more formalized training, said Terri Fanz-Falzone, who as VP of HR for Engel North America, started the apprenticeship program and refers to its participants as her kids.
“It’s evident that our technical skills are somewhat lacking in the U.S. for really anyone under the age of 50,” she said.
The apprentices earn as they learn — typically between $22 and $24 per hour to start, depending on their experience — and as long as they finish the program, they’ll have a job with Engel upon graduation.
Competition for the positions has been fierce, according to Fanz-Falzone, who in February was sifting through applications from people hoping to catch on with a new cohort. The company has established apprenticeships based on its projections of future professional openings, as well as its estimation of how much training staff members can juggle around their day-to-day responsibilities.
“Within a week and a half, I’ve received over 600 applicants. In a week and a half, for four positions. The reality is that [at] Engel, we’re taking, at this point, less than a half of a percent of those who have applied,” she said.
Bright opportunity
At 25 and a member of the initial cohort, Dan Heinrikson considers himself one of the lucky ones — he’s well on his way to becoming a professional service technician.
After he and his fellow apprentices spent the first four months of their apprenticeship at Engel’s U.S. headquarters in York, Pa., splitting time between the classroom and plant, Heinrikson has been on the road, traveling constantly throughout the Southeast from his home in Douglasville, Ga. Under the supervision of mentors like Forrest, who's based in Chattanooga, Tenn., he services IMMs and interacts with Engel’s customers — a job both men say makes them ambassadors for their employer.
When their presses aren’t running, Heinrikson said, customers can be frantic for a fix from Engel.
He said he enjoys helping them out.
“I’ve always liked to work with my hands, I’ve always had some sort of mechanical aptitude, as well,” he said.
He grew up dreaming of being a sports star, but by the time he graduated from high school, he realized that wasn’t in the cards. He needed to kickstart a career, and for ideas, he looked to his father, a salesman who worked in plastics.
He thinks it’s unfortunate that schools don’t provide more information on the trades because he believes without a personal connection to the industry, he might not be on his current path.
“I grew up in Chicago, so we had a lot of unions over there, and most of the kids, if your dad wasn’t in the union, you probably weren’t going to go into the union,” he said.
For three years, he worked in an injection molding shop, where he got his first exposure to the machines he’s now learning to fix.
At first, he changed out molds. In his last year at the molding plant, he worked in processing.
“I’m very partial to Engels because that is all that we had at the place that I used to work at,” he said.
Then, he landed in York.
“As each opportunity presented itself, I did my best to fill that role, and it brought me all the way to Engel,” he said.
Investing in the workforce
Apprenticeships offer opportunities for both people and companies. Registered apprenticeships set standards and expectations for both parties, and, Fanz-Falzone said, ROI is quick.
“Granted, the first year, there’s not going to be much return on investment, but they’re also only making 65 percent of the wage. By the time you get into Year 2 and, certainly, Year 3 and 4, you’re paying them a reduced rate, and they’re performing functions for you. So, I really believe by the time you hit Year 1.5, your return on investment is well-returned,” Fanz-Falzone said.
For employers interested in offering apprenticeships, two basic options are available: Develop a program in-house, or find support from an agency that already administers registered apprenticeships, and work with it to create a new program or implement an existing one.
Even with its ties to Europe, where apprenticeships are far more common, Schwertberg, Austria-based Engel had to tailor its program to the needs and requirements of the U.S., Fanz-Falzone said.
“In the European countries, it’s very common to begin your apprentice[ship] when you’re roughly 15 years of age. In the U.S., there’s a lot of laws that you can’t do that,” she said.
In accordance with Department of Labor rules for registered apprentices, Engel’s apprentices get raises every six months. In addition, they get a raft of benefits, including health insurance, as well as three weeks of vacation and generous per diem rates when traveling.
While in York — where new apprentices begin the program and spend one month each of the subsequent three years — apprentices stay in corporate housing. They're eligible for company-paid airfare to return to their hometown, if necessary.
Program requirements also call for participants to receive at least 144 hours of classroom training a year, but Fanz-Falzone projects that the program will far exceed that. Trainers from the Pennsylvania Manufacturers’ Association provide about 175 hours of training a year, and Engel's own personnel offer between 80 and 120 hours.
In all, the educational costs Engel absorbs are modest. They total $18,644 over four years, but grants — including from the Department of Labor — cover most of the tab.
“My real outlay of education is significantly lower than that. It’s about $800 per year per apprentice,” Fanz-Falzone said.
The numbers demonstrate the benefit to both employer and employee, and, Fanz-Falzone said, help to explain why interest in her company’s apprenticeship positions is so high.
“What we pay goes into it, that the ability that, when you graduate, if you performed all of your tasks sufficiently and ... your performance is up to par, that you’re getting a job. You know, when you look at people going to university right now, they may go for four years and come out with two [or] three hundred thousand in student loans. And the average person coming out of university is making about $66,000 a year,” she said. By comparison, Engel’s newest workers can clear six figures in a year.
In contrast, according to the U.S. Department of Education’s National Center for Education Statistics, the average cost of a year of college in the U.S. varied from $9,400 at public institutions in the 2020-2021 school year to $37,600 at private nonprofit schools.
Top-notch candidates
Five years into an injection molding career, including almost two as an Engel apprentice, Heinrikson is reluctant to compare his experiences as a paid apprentice to those of his peers who chose college instead, but he offers an enthusiastic assessment of what the opportunity has meant for him.
“It’s an awesome career opportunity for me, because, honestly, this is what I envision me doing for the rest of my life,” he said.
Fanz-Falzone finds satisfaction in knowing that Engel’s apprenticeships represent life-changing opportunities for those, like Heinrikson, who are selected.
Apprenticeships can help people from underprivileged backgrounds make a better life for themselves and their families, she said.
To be sure that candidates get a fair shake, the application process follows Department of Labor rules regarding diversity and inclusion.
“I always go by the [saying] that talent is equally distributed; however, opportunity is not,” Fanz-Falzone said. “Things like this really give a great opportunity to those who maybe couldn’t afford to go to university, people coming right out of high school, they weren’t sure what they wanted to do, but they’ve got some technical interests.”
She revels in knowing that prior apprenticeships she set up at other companies launched their participants from $9-an-hour jobs to careers paying $35 an hour or more.
“It gives them a sense of pride. They become better partners, better parents, better community members because they now have that pride in themselves, that, ‘Look at me, look what I did.’ "
More than half of Engel's apprentices represent minority backgrounds, and two women have participated, though one dropped out, she said.
Of the six people in the inaugural cohort, only Heinrikson came aboard with prior plastics experience.
Other apprentices have resumes that include installing heating, ventilation and air conditioning systems, or working on cable towers. Four served in the military — an experience Engel rewards with points in its candidate-evaluation system.
In all, of the 16 people who have participated in either the field-service technician or automation apprenticeships, 14 remain with the program.
Because the company is looking to train service technicians for roles that require constant travel to customers’ molding plants, Engel has one unusual preference for applicants — they should be 25, old enough to rent a car. At the time he was hired Heinrikson was a bit young, but other factors came into play, Fanz-Falzone said.
“Since Dan came to us with experience and interviewed incredibly well, we made the decision to work through any difficulty with rental vehicles — glad we did!” she explained in an email.
Living in — or being willing to relocate to — an area where Engel customers are concentrated is important, too.
Candidates who’ve held any kind of job for a significant amount of time, or who have demonstrated an interest in working with their hands — whether as woodworkers or robotics enthusiasts — can stand out.
“Maybe they like to monkey around with a wrench in their garage on different vehicles, that type of thing,” Fanz-Falzone said.Building a career
Forrest and Heinrikson represent different generations, but they explain the appeal of plastics in similar ways. They're happy not to sit behind a desk.
“I’ve always, always, always loved playing with machines and anything that had electrical or pneumatics on it. … So, I think that's probably why I have succeeded so well in this industry, because it's something I do for a career, but I actually enjoy doing it because I like fixing things. I like building things. I played with Legos as a kid my whole life,” Forrest said. “To me, it’s just like putting big Lego sets together.”
He called working for Engel “a fantastic fraternity to be in” — a sentiment apprentices echo.
In a video produced by the company, they praised mentors’ knowledge and willingness to teach.
“Engel is very brotherly. … Being an apprentice, I’ve learned a lot from a lot of the people that have been here for years. And, overall, it just makes me a lot more comfortable with learning what we’re doing here,” one said.
Leveraging both technical and interpersonal skills to fix machines and manage relationships with customers takes a special type of person, Forrest said. He has high praise for Engel’s “amazing group” of apprentices. Like them, he learned his job from doing it.
“Engel has found a way to really narrow down those people when they’re recruiting them to make them understand, ‘You’re going to be on the road.’ And those guys like to travel, they like to fix stuff, and they like being around people,” he said. “It’s kind of a three-pronged thing.”
Heinrikson appreciates that, as his aptitude grows, his mentors are standing aside to let him take on progressively harder challenges.
He's ready for it.
“If you let me get in there and get hands-on with it, I will learn better that way. … I do like how Engel has been doing the training,” he said.
Karen Hanna, senior staff reporter
Karen Hanna | Senior Staff Reporter
Senior Staff Reporter Karen Hanna covers injection molding, molds and tooling, processors, workforce and other topics, and writes features including In Other Words and Problem Solved for Plastics Machinery & Manufacturing, Plastics Recycling and The Journal of Blow Molding. She has more than 15 years of experience in daily and magazine journalism.
Related
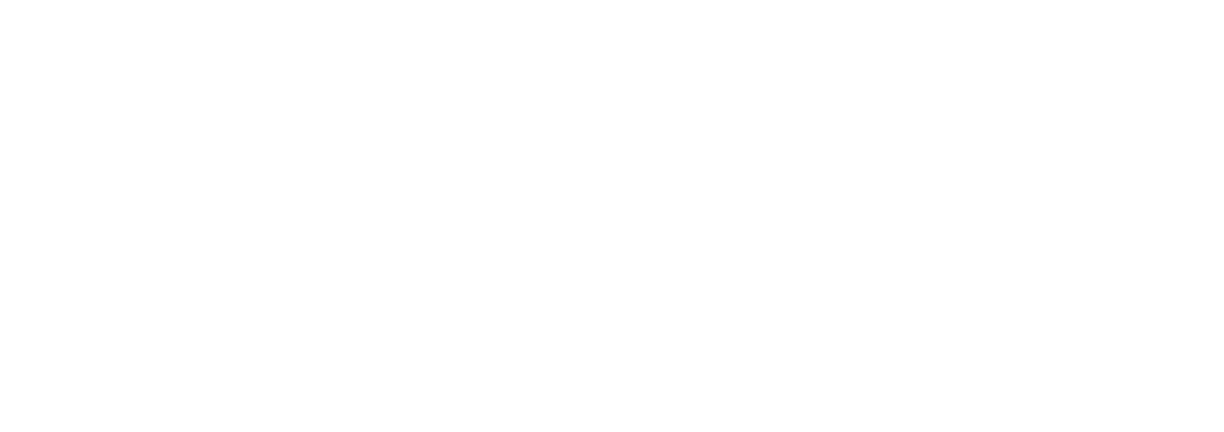