By Karen Hanna
In diverse settings settings around the world, robots now are cooking food, assisting on surgeries, polishing molds, boxing goods, hanging drywall, even operating drills on construction sites.
All without guarding.
And their communication skills also are getting better, according to experts on collaborative robots (cobots), with advances in automation and vision technologies coming at a critical time, as companies look for ways to offset labor shortages. At least one expert says, despite restrictions imposed by safety concerns, cobots will continue to push past barriers regarding speeds and payloads. According to at least one study, prices are coming down, too.
Alberto Borboni is one of the writers of the paper, “The Expanding Role of Artificial Intelligence in Collaborative Robots for Industrial Applications: A Systematic Review of Recent Works.” An associate professor of engineering at the University of Brescia in Italy, he sees a very bright future for cobots, especially over the next five years.
“Because there are no barriers and cobots are simple to program and reprogram, this maintains production rates, reduces the risk of downtime, and allows for more flexible production layouts. It is highly likely that the number of cobot installations will be significantly higher than that of standard traditional robots,” he said.
Easy does it
With a career in robots that spans more than 40 years, Joe Campbell has seen a lot of automation trends. He has advice for anyone who last considered cobots a few years ago: It’s time to look again.
“A lot of the customers that we talk to perhaps looked at traditional automation five or 10 years ago, and they said, ‘Well, it's too expensive, it takes up too much floor space. ... I don't have a robot engineer on staff, I don't have anybody who can program it.’ And those were all fair objections 10 years ago, but that's not the case with collaborative technology, particularly UR’s. It is really, truly easy to use,” said Campbell, senior manager of strategic marketing and applications development for Universal Robots (UR) USA.
When he entered the field a little more than a decade ago, just as cobots began generating a stir, Hulgard said people were excited by the mere notion of having robots that could work safely alongside humans.
“Back when it all started, nobody really paid much attention to the ease of use. Everybody was talking about safety, ‘Hey, we can save time and money and space by not installing these robots with a safety guarding around them, and we don't have to take that much space in manufacturing floor and so on and so forth.’ Now, fast forwarding to now the safety part is something that everybody has accepted, and everybody has figured out. Now, it's all about ease of use,” he said.
Thanks to cobots, expectations of how automation should work are changing, said Chris Caldwell, product manager for Yaskawa Motoman.
“One of the fundamental shifts that cobots drove was an increased awareness of the importance of ease of use. With technology advancing, there is getting to be less and less of an acceptance for things being difficult,” he said.
Get smart
For an explanation of how cobots have improved, look to the innovations and add-ons that make up their eyes and brains.
“Vision and artificial intelligence (AI) are mutually beneficial technologies and, actually, are the key of cobot evolution in manufacturing,” Borboni said. “If we mean artificial intelligence as machine learning algorithms, they will benefit greatly from the widespread use of parallel hardware by enabling higher throughput rates while maintaining safety levels. The ability to perform multiple calculations at the same time will enable the integration of teams comprised of numerous human and robotic agents.”
Relevant technologies include: inbuilt sensors that detect proximity, motion and torque; LiDAR — or light detection and ranging — sensors; and 2D vision sensors. “Systems that employ 3D depth cameras and computer vision algorithms enable cobots to operate alongside people and have complete knowledge of their environment,” states the report Borboni co-coathored.
Over the past five years, cobots have entered the market that have sensing elements all over them, so their joints are independently controlled, says the report, which notes collision rates are down.
Machine learning — a subset in AI — allows cobots to improve at their tasks over time, according to the study.
That gives them an edge over industrial robots.
“Cobots benefit from faster learning and easier programming due to AI,” the study states. “Industrial robots need intricate reprogramming, which calls for a knowledgeable engineer or programmer. A cobot’s real-time interface allows for interactive human input during communication, whereas robots require remote interaction.”
With improvements in machine learning, cobots are able to learn more quickly, even by example, said Ken Fordyce, a retired IBM engineer who has expertise in a diverse set of analytics methods.
Cobots also can recover from failure more gracefully, unlike other machines or computers that might require a full reset to restart. With AI, they can “learn basic tasks quickly through demonstration and basic instruction,” as well as “sense and respond to execute tasks and avoid collisions,” Fordyce said.
The study Borboni co-authored hints at both how far cobots have come — as well as what strides might remain to be made.
“End-to-end autonomy in learning-based robots commonly includes three primary elements, such as perception, cognition and control. Due to the complementary nature of these elements, autonomous control is made possible by sophisticated sensing and cognitive techniques,” the report states.
As of now, though, “cobots remain unable to discern an individual’s emotional condition.”
But they will continue to get better, automation experts said.
Application multiplication
Compared with industrial robots, cobots’ ease of use and smaller sizes make them accessible, even for employers that previously might have rejected automation due to concerns over cost or the perceived hassle of handling high-mix, low-volume work that would require constant reprogramming.
“There’s need for all the applications as we’ve always been doing, just at a much higher level, because now we have more affordable automation, we have easier-to-integrate automation, we have faster automation,” OnRobot’s Hulgard said. “The technology is there to support any type of business case.”
Caldwell, of Yaskawa Motoman, listed a raft of possible applications: plastic degating, deburring and finishing, as well as “machine tending or pick-and-place applications … palletizing applications, assembly, fastening or screw tightening, adhesive/tape application.”
He predicted an increase in cobot utilization in post-demolding secondary operations.
One important characteristic of cobots is the ease of reprogramming, which has made them a perfect fit for companies that have frequent changeovers, such as small-batch custom molders Ferriot, Akron, Ohio, which has put a mix of cobots to use to free up labor and Aim Processing, Longmont, Colo., which uses Flexxbotics' FlexxReference app to reprogram its UR cobots quickly.
“In general,” Italian professor Borboni said, “I believe manufacturing systems will increasingly center on two broad categories: standard products with large production batches made with automation and traditional robots, as well as customizations, and small production batches made with collaborative robots and human operators.”
Facilitating that level of flexibility is especially important to UR and its customers, Campbell said.
To illustrate how easy the UR cobots are to use, Campbell cited one manufacturer in rural Wisconsin that staged a contest challenging each of its employees to be the first to program a new application.
“A 26-year-old woman, no degree, certainly not a roboticist, she really dug in,” he said, “And she’s now the robot tech for the plant.”
More than 160,000 people have taken UR’s online training classes, he said. The nine core modules take just about two hours. Students who complete the core module are eligible to take five additional modules.
“You come to a trade show, I’ll have you programming in 10 or 15 minutes,” Campbell said.
Right fit
Matching the machine to the application is a job that requires integrators, some of the automation experts said. Integrators can provide training and insights into what’s possible, and steer processors away from decisions they might come to regret.
“I’ve seen that. It’s not one time; it’s 100 times, I’ve seen. Walking into a manufacturer’s manufacturing floor, and then there’s one or two robots just sitting on a shelf somewhere, and they’re like, ‘Ah, we never really got to it,’ or ‘we couldn’t really figure that out,’ or, you know, ‘we changed some things,’ ” OnRobot’s Hulgard said.
Yaskawa Motoman’s Caldwell said automation experts can help processors identify the easiest applications to automate, as well as dispel misperceptions they might have about technologies such as cobots.
Variables that can determine whether a cobot or industrial robot would be better suited to a given application include throughput, cell design, payload, footprint and safety requirements.
Each has its own place, according to Caldwell.
“Have an automation provider tour your facility, and they’ll find applications that have existing solutions. Start with the low-hanging fruit and use the ROI to fund some of the more challenging applications. Automation is an iterative process, and you can keep attacking the current bottleneck for your business,” he said.
Robots rule the future
Cobots’ appeal will continue to grow as manufacturers look to fill roles in a tight labor market, automation experts say. OnRobot’s Hulgard predicts robot deployment over the next five years will be at a level 10 times larger than today. He envisions the manufacturing plant of the future staffed by robots — and the people who enjoy working with them.
Both he and fellow automation experts also say they believe the technologies will continue to improve.
“Our younger generation of workers, they like to work with computers; they like to work with technology. That’s a big driver in how people select their career, and this is a great fit, saying, ‘OK, instead of having 10 people standing on a conveyor line and putting things together, now we have 10 robots,’ and instead, you’re hiring X amount of people to maintain and to optimize and run these robots, and be part of that side of the technology,” Hulgard said.
Though bound to make cobots that can interact safely with humans, engineers will continue to find creative ways to push the envelope, UR’s Campbell said.
“I’ve yet to meet a robot engineer who doesn’t want a robot that’s bigger, stronger and faster,” Campbell said.
Onexia’s Pelesky is waiting on a specific function to become common and efficient — the ability of automated guided vehicles to taxi cobots from one assignment to the next.
“I want to put an arm on an AGV and make it work effectively,” he said.
Brains — in addition to brawn — likely will continue to underscore cobot advances.
Automation is in an evolutionary stage similar to computers in the 1980s, OnRobot’s Hulgard observed. As people eventually understood about their computers, the user experience is what matters, not the physical components that facilitate it.
“That’s also the direction I think the whole industry will take, just like the IT industry did back from the ’80s. … The hardware, nobody really cares what’s inside the computer, what your graphic card’s brand is, or what your screen brand is, or whatever. It’s all about the software that controls it. That’s the big difference, and that’s the direction this industry will take,” Hulgard said.
That might mean that cobots eventually operate with digital twins, or develop more natural relationships with humans. The strategies — along with avatars, gestures, gazes and even “MindBots” or EEG brain scans — all are studied in research cited by the report Borboni co-authored.
He foresees a more positive environment for humans, facilitated by cobots.
“When operators can avoid focusing too much on giving commands to robots, they can direct their mental energies more actively toward production or better relating to each other. In short, they can be reborn as humans instead of being part of an assembly line, as in Charlie Chaplin's well-known film, ‘Modern Times,’ ” he said.
Data captured by the sensors cobots use could have plantwide benefits.
“Supply chain management can be improved by centralized data insights from digital industries fed into machine learning algorithms. This includes optimizing logistical routes, switching from bar-code scans to a vision-based inventory system and making the most of available storage capacity. Additionally, machine learning can forecast demand trends to assist in preventing excessive production,” the report states.
As automation and cobots evolve, tolerance for having humans struggle to interact with technologies could continue to decline, Yaskawa Motoman’s Caldwell said.
“Smaller companies have been served very well with solutions that are easy to add into their existing operation. In the longer term, as sensors improve and technology is more widely adopted, I think there will be an even more blurred line between what is a cobot and what is an industrial robot. ….” he said. “Ultimately, I don’t know that market penetration is as much of the metric as much as market disruption is. Cobots have already driven an ease-of-use arms race.”
Karen Hanna, senior staff reporter
Contact:
Association for Advancing Automation, Ann Arbor, Mich., 734-994-6088, www.automate.org
International Federation of Robotics, Frankfurt, Germany, 49-69-6603-1697, https://ifr.org
Onexia Inc., Exton, Pa., 610-431-7271, www.onexia.com
OnRobot, Odense, Denmark, https://en.onrobot.info
Universal Robots USA Inc., Ann Arbor, Mich., 844-462-6268, www.universal-robots.com
Yaskawa America Inc., Motoman Robotics Division, Miamisburg, Ohio, 937-847-6200, www.motoman.com
Karen Hanna | Senior Staff Reporter
Senior Staff Reporter Karen Hanna covers injection molding, molds and tooling, processors, workforce and other topics, and writes features including In Other Words and Problem Solved for Plastics Machinery & Manufacturing, Plastics Recycling and The Journal of Blow Molding. She has more than 15 years of experience in daily and magazine journalism.
Related
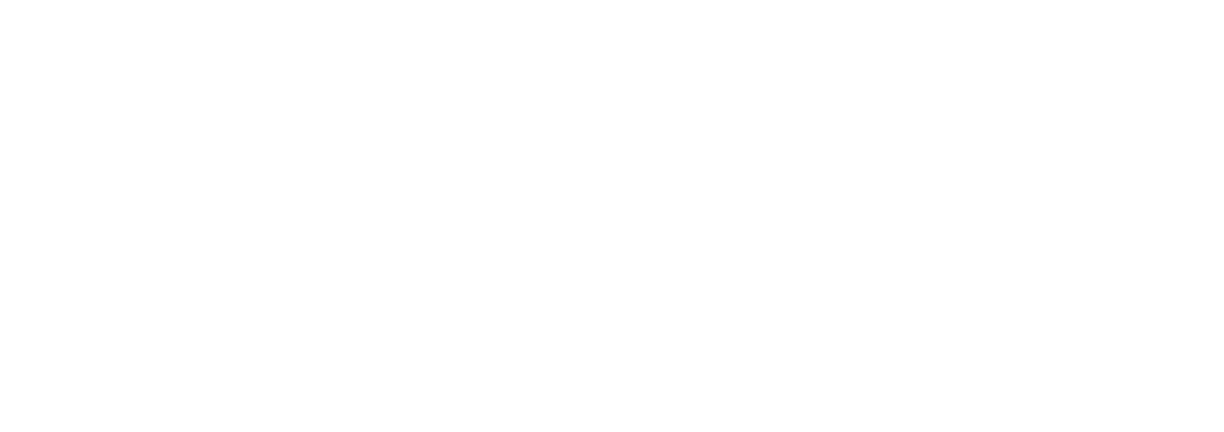