Have you found an innovative equipment solution to a plastics processing challenge? Let us know.
Problem: A custom molder needed to find a way to produce its high-mix, low-volume portfolio of parts without requiring two to three operators on every job.
Solution: A mix of cobots and vision systems can be quickly adapted to handle a wide range of parts.
By David Tillett
Cobots, sometimes working in coordination with vision systems, handle tasks that may include part takeout, sprue removal and ultrasonic welding at Akron, Ohio-based custom molder Ferriot Inc. The company has evolved these capabilities over the years to allow it to free up operators to handle more machines, and to focus on other tasks. But the company’s earliest experiments into automation were rather modest.
“It all started, actually, years and years ago with a guy named Randy Honeycutt. He actually would make end-of-arms that would do inserts and stuff like that … instead of having our operators open the door and put little inserts in every single time,” said Jeff Hodnick, an automation engineer at Ferriot.
“And from there, it kind of evolved into now where we have cobots that we deploy to handle different operations. We’re able to totally eliminate the need to have two or three operators on a job; we can just use one. And, so, it's a better distribution of labor across the floor.”
As Ferriot dove deeper into automation, its engineers were able to take on more challenges in-house, with the company forming its own automation department about three years ago.
And as more automation is introduced, it can free workers to do more-varied tasks.
“We’re able to have them work with multiple presses, so it’s not like they’re just stuck there doing the same thing,” Hodnick said. “I know a lot of people struggle more and more … especially as the younger generations come in, with factory work specifically because it’s a lot of times just repeatability over and over and over. It’s the same thing. So, us being able to diversify in that way and keep things changing for them, I think is a big advantage.”
He said some of the tasks that have been reduced include cutting and trimming, “and a lot of the stuff that isn't fun.” This shifts some duties more to bagging parts, filling boxes and packaging. “They’re able to be part of the line of defense, when it comes to quality as far as checking the part itself,” he said. “It frees their mind up to do a lot more of the quality and fine-line side of things, I would say."
Cobots are relatively easy to use, with some OEMs touting the promise that they can be set up, programmed and begin handling parts in a matter of hours. For the simplest tasks, Hodnick said a cobot can work as advertised.
As the needs become more challenging, he said there are third-party companies that sell specialized parts to work with cobots, such as clamps and sanders. “But … premade solutions can get kind of pricey.” And for really complex applications, processors could turn to integrators — an even more-expensive proposition.
Or a company can decide to develop these capabilities from within, as Ferriot has. “And, so, it depends what you want. Internally as a company, if you have the engineering staff and they have the time and the capabilities of going out, custom-selecting their own sensors and that type of deal to put on the end of a cobot, for example, then I would say, ‘Yes, it's worth doing it that way,’ ” Hodnick said.
“But if you're in a company where you only have one engineer, or somebody who's knowledgeable enough to do these type of things … then it doesn’t really make sense to do all this stuff hand-picked as much as it makes sense going with a company that already has stuff preconfigured for you — like Fanuc, with their cobots, they have partners that already have end-of-arms designed that have vision systems, it’s already integrated in the software and their control tablets. Same with the Universal Robots, they have the same thing.”
Ferriot’s automation department has broadened its capabilities. “We are to the point where we will make stand-alone stuff and full-on automations. We do all our own PLC programming, the HMIs, all of that internally,” Hodnick said.
The tactics the automation department employs are very job-dependent, Hodnick said. Sometimes, the company might forgo an HMI to use a simple PLC with no screen. “I mean, it’s great to have an HMI. But at the same time, there's a lot of situations where it’s really just not required.” As an example, he said, Allen-Bradley makes great PLCs that can cost about $2,500, but for many applications a lower-cost Omron or Eaton PLC is more than sufficient — for about $200. “So, for a high-mix, low-volume manufacturer like us, the little tricks, little things like that … that is huge.”
Ferriot has been able to press cobots into service in some unique ways. “The easiest task for a cobot is pick-and-place stuff. And then from there, it kind of evolves up into where we actually put Dremel tools to use a cobot almost like a CNC. Worked phenomenal, too,” Hodnick said.
Another job the automation department tackled was welding. “We will actually use parts underneath an ultrasonic welder with one [cobot]. We had to come up with some of our own proprietary stuff to pull it off, but we were able to.”
An operator puts a plastic part into a part tray, then loads more than a dozen inserts into holes in the part. When the filled part tray is moved into the correct position, it prompts the cobot to slide the tray under the welder, which lowers to seat inserts one by one each time the cobot repositions the tray. The cobot then slides the tray near the operator, and waits to be prompted to begin the next cycle. While the cobot guides the welding, the operator loads inserts into the next plastic part. Hodnick said the addition of the cobot has allowed Ferriot to double output for this task.
The most complex automation Ferriot has put into action so far, combines a cobot and vision systems to inspect parts. This is used to inspect an injection molded part that measures about 2.5 feet by 2.5 feet and has a lot of features on its surface. The part undergoes what he called pretty extensive secondary operations that add a lot of components to it.
He said the inspection is complex, “because not only are we looking for reflection off stuff, and guaranteed placement of stuff, but we also have multiple sensors on the same end-of-arm. So, we’re also looking for depth of screws, we're looking in deeper channels … checking in different cavities at the same time that everything is properly located.”
Referring to cobots, Hodnick said, “They’re definitely the biggest Swiss Army knife [among automation tools], especially if you’re designing your own end-of-arm.”
How does a cobot vision inspection stack up to its human competition?
“Theoretically, they [humans] could do it faster. But then you have human error that you have to add into that calculation as well, versus, with the cobot, it'll take about maybe 45 seconds, which, with an almost 2-minute cycle time, is nothing. But you’re never going to get a mistake with the cobot.”
Hodnick said the custom molder, which has more than 150 employees and 20 injection molding machines running in its 200,000-square-foot facility, has used several different cobot brands, mentioning Universal Robots, Fanuc and Kawasaki. He said familiarity with a brand’s interface makes it easier to adapt as innovations are introduced. “Because we have several different generations of several different brands of robots … it’s normally easier to then go on to the next newer,” he said.
When asked if he has a favorite among the cobots Ferriot has used, Hodnick wouldn’t commit, saying, “Not specifically yet.”
Vision systems have also played an important role for the company, and here Hodnick singled out the Keyence IV series of sensors for praise. “The capabilities that they have in these little sensors, for the price point, is amazing,” he said.
He said the Keyence sensors are easy to program, and can handle a wide range of functions, such as noticing the presence or absence of a particular feature, detecting short shots, and identifying and inspecting inserts. Using interchangeable nests underneath the sensors, the sensors can switch between programs and check different parts.
For tasks that require color detection, higher-end sensors are required — some of which Ferriot uses in one-off vision systems tailored to specific parts.
Hodnick said some of the greatest value from pairing cobots with cameras and sensors comes from the ability to check parts from any angle — and update the motion to match the needs as new parts are added.
“Versus before, where … everything had to be specialized. If you added a part, and say there was a weird angle over here that none of your other parts have, you immediately have to compensate for that,” he said. “So, even if none of your other parts have a camera that can see that stuff or have the requirement for that, you'd have to add one [sensor] to see that.”
Instead of creating a unique fixed station for each new part, Hodnick said having swappable nests opens the possibility of inspecting multiple different parts with the same cobot and sensor setup.
Hodnick said one thing that has helped Ferriot maximize the value of its cobots and vision systems is the automation department’s focus on standardizing components and fixtures it fabricates in-house so that all employees are comfortable using them, while also allowing for great flexibility to adapt to different tasks’ requirements.
“We’re able to use multiple different setups on the same cobot and do different jobs with it,” he said. “Our cobots are set up so they’re on wheels, they have a standardized table. And then from there, on each of the things we mount to that table [we have] marked where to mount it, how to do it, what to plug in.”
Hodnick said that production volume is one factor in deciding where to introduce automation. As a rule of thumb, for larger parts you might need production to reach 15,000 or more parts per year, while, for smaller ones, it might be 45,000 a year before stand-alone automation is justified.
However, he said Ferriot runs jobs that churn out about 1,000 pieces per year with full automation, and jobs that produce 100,000 parts per year with almost no automation. “A lot of it is just dependent on volume, cycle time and then the specific actions that need to be taken,” he said.
While Ferriot’s efforts to introduce automation sometimes directly decrease a line’s dependence on multiple operators, other efforts focus on lifting repetitive or monotonous tasks from human shoulders.
As an example of automation making things easier for operators, Hodnick pointed to a task that required operators to clip sprues off the bottom of each part.
“I’m sure you can imagine the strain on your wrist when you’re clipping a three-quarter-inch thing of plastic every single time a part comes off a belt. … Just them having to do that constantly is not easy on them.”
Ferriot now has a robot arm remove the part from the mold, place it into a nest where it is automatically clamped in place, and a CNC mill removes the large piece of sprue from the underside of the part — greatly reducing the strain placed on operators.
“That’s definitely what I would say is the biggest benefit that I see right now, just removing the harder tasks … it makes their life easier,” Hodnick said.
Another example he gave was a fixture that doles out magnets for operators to add to a part. With the original fixture, the operator would have to reach out and pull a lever for a magnet to be dispensed, and each part required three magnets. He created an updated fixture that had a button on either side, so operators didn’t have to reach as far, and getting a magnet only required the push of a button.
“The strain that little movements like that would start to put on their body — we were able to completely eliminate that.”
“So, just eliminating awkward body movements, just really trying to make stuff more fluid so they’re not straining themselves,” Hodnick said.
Sometimes focusing on incremental changes can bring large gains in productivity.
“A lot of times, it's how can we make a job so it only either requires one operator to be stationed there, or how can we make it a quarter of an operator, so for three presses that are running, we can have one operator doing all of the packaging? … Doing that, you can have four operators running 12 presses at once,” Hodnick said. “The profitability in pulling something like that off is huge, so, I would say [we’re] getting to the point where we can run in blackout [lights-out] mode. But we’re kind of in this stage before that, where we're working now towards the quarter-operator operations.”
Looking to the future, what does Hodnick see as the potential for automation? “We would like to automate every single job, to be quite honest with you,” he said. “We would like to handle everything with robots, everything with automation. The only time a human ever has to even interact with it is when they're taking the parts out the door.”
“But … we're a high-mix, low-volume molder. So, with that comes the challenge of, ‘Do we run enough parts every single year to justify going to the extent of buying all this external equipment?’ So, for us, I guess it really just depends on the right job, the right quantity.”
David Tillett, associate editor
Contact:
Ferriot Inc., Akron, Ohio, 330-786-3000, www.ferriot.com
David Tillett
Associate Editor David Tillett writes and edits for Plastics Machinery & Manufacturing, Plastics Recycling and The Journal of Blow Molding. He covers new products, industry news, patents and consumer and business equipment. He has more than 20 years of experience in daily newspaper, online and magazine journalism.
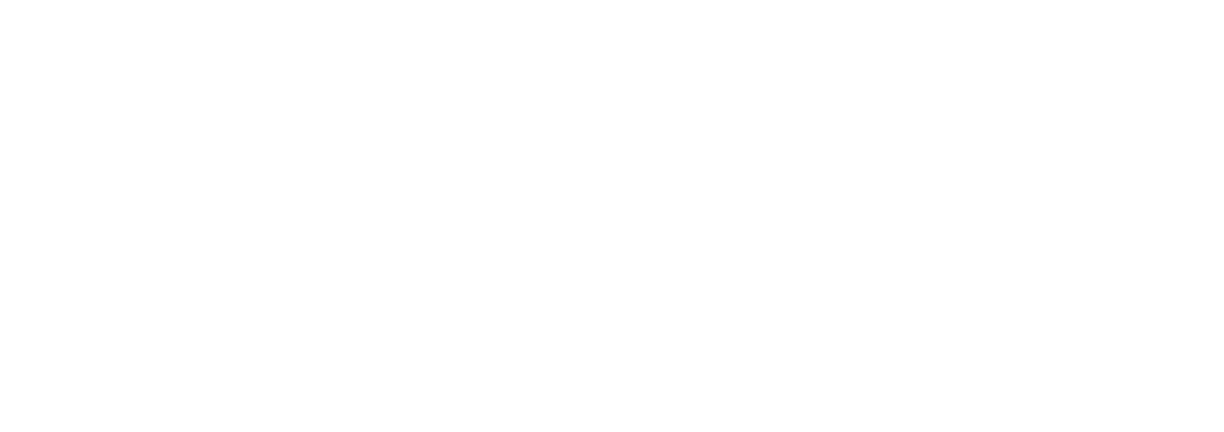