IndustrialML software aims to help manufacturers deal with skills gap
Plastics Machinery & Manufacturing is focusing on smart factory solutions in July. Follow plasticsmachinerymanufacturing.com for more, or subscribe to our print issue.
By Bruce Geiselman
IndustrialML’s enterprise software and IIoT software, is aimed at helping manufacturers produce quality products while dealing with a persistent skills gap, according to the company.
“I don’t know exactly what the numbers are for plastics, but I imagine it’s fairly pronounced there as well. People of my generation generally do not want to go into manufacturing, or even if they do, our average tenure of position is a little under three years, whereas with the baby boomer generation, it’s typically about 10 years in any one job. So, for a typical factory, what you’re staring at is a much more transient workforce for the next 10 years than has been the case for the last 70 or 80 years.”
That’s problematic for manufacturers, including plastics processors, because it means they are operating with a declining number of skilled workers, Chandar said.
IndustrialML’s technology aims to make imparting skills easier, better, cheaper and faster, Chandar said. Typical plant floor workers require two to three years to get comfortable performing day-to-day tasks unsupervised and five or more years to gain real intuition for troubleshooting errors that occur during those day-to-day tasks, Chandar said.
Transferring the factory’s decades of accumulated institutional knowledge into IndustrialML’s software and communicating that to workers through alerts and instructions allows them to resolve issues with less time spent internalizing the knowledge and with a paper trail of the instructions they were given. It also leads to workers learning new skills more quickly, Chandar said.
“That’s ultimately what our platform is intended to accomplish,” he said. “The primary thing is, if you have someone who has been on your production floor for six months to a year, they still have some reasonable capacity to do the job as well as someone who’s been there for 10 years because that knowledge can be imparted to them in real time.”
IndustrialML developed its software as a service (SaaS) platform over the past three years by working with one to ONE Holdings (o2Oh), which owns steel tube manufacturing operations, including Daiwa Steel Tube Industries in Japan and Daiwa Lance International in Vietnam.
“We are looking to expand partnerships now,” Chandar said. “Among those industries that we’re interested in expanding to would be the plastics industry in particular.”
The company’s platform currently can connect with six types of PLCs, several types of enterprise resource planning systems, and various third-party sensors and vision systems.
"You can use that not only to inspect for contaminants in your plastic as it’s being spooled or even as it’s being extruded, but you can use similar techniques to monitor the equipment itself to see if there might be chips or cracks in the screw as something is being extruded.”
IndustrialML’s software, working with a vision inspection system, could be taught to identify defects that less-skilled workers might not catch.
“It’s more of a compensation for things that workers can’t do and that they would need decades to be able to do effectively,” Chandar said.
The IndustrialML platform also works with sensors to monitor the voltage and amperage of welders and temperatures of furnaces used in steel tube production. Similar technology could be used to detect a short shot in injection molding, or whether the temperature on an extruder dropped because of a problem like a broken thermocouple, he said.
“We could provide real-time alerts as to the dropping of the temperature, and we could provide the appropriate troubleshooting steps to an operator and a manufacturing engineer and potentially to a salesperson so that they know five hours early to anticipate a delay, instead of being surprised at the end of the day,” Chandar said.
In addition to providing troubleshooting tips, the platform also can provide a set-up checklist to a machine operator when production changes from one product to another, he said. Set-up information and troubleshooting steps can be recommended based on information from a manufacturer’s operations manual and set-up instructions, Chandar said.
The IIoT platform uses several methods of communication with workers.
“This was one of the biggest challenges that we had to try to figure out how to overcome,” Chandar said. “Our original plan was to have giant monitors on the production floor that people could look up at any time. It quickly turned out that was not going to work because there was too much information. Then we progressed to tablets, but it was kind of the same issue. Operators could not be in a factory environment, having to hold a tablet in two hands and pay attention to the line.”
As a result, the company now employs a combination of communications technologies.
Workers on the production floor wear headsets. When there is a critical situation on the line, the platform sends an audio alert to the appropriate workers. If the workers need additional instructions on how to address an alert, they can use a mobile app on a smart device. Workers who aren’t on the production floor can receive email alerts and view dashboards on a computer monitor to track what is happening.
IndustrialML encrypts customers’ data and then transmits it to their cloud service. The data is transmitted using a customer’s internet connection, or in plants with poor internet connections, it could be transmitted using a 4G or 5G router, Chandar said.
Bruce Geiselman, senior staff reporter
Contact information:
IndustrialML, Davie, Fla., 857-529-9656, https://industrialml.com
Bruce Geiselman
Senior Staff Reporter Bruce Geiselman covers extrusion, blow molding, additive manufacturing, automation and end markets including automotive and packaging. He also writes features, including In Other Words and Problem Solved, for Plastics Machinery & Manufacturing, Plastics Recycling and The Journal of Blow Molding. He has extensive experience in daily and magazine journalism.
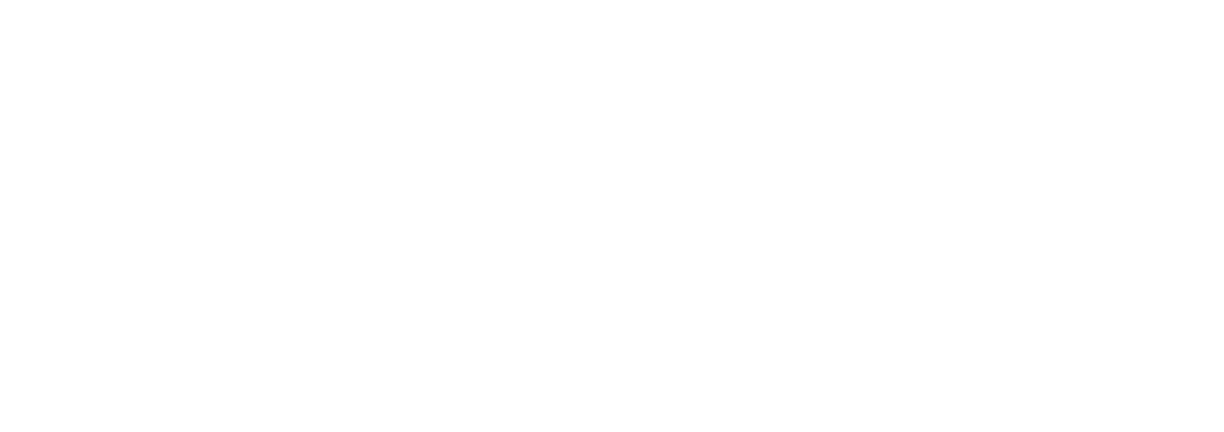