By Bruce Geiselman
An IIoT subscription service two years in the making will allow users of products from the ACS Group to predict and prevent problems involving their auxiliary equipment.
Introduced in April, the MiVue system uses built-in hardware to work out of the gate with new equipment from the conglomerate, which includes AEC, Sterling and Cumberland.
The group’s equipment includes blenders, conveyors, dryers, chillers, temperature control units, cooling towers, granulators and shredders, but eventually, the software will work “with all industry products,” according to a company press release.
Ongoing product development will enable MiVue to work with injection molding machines, extruders and other machinery.
To really make Industry 4.0 work, the ACS Group knows its customers need access to data from primary equipment as well as ACS Group’s equipment and competitors’ equipment, said Michael Gersmeyer, senior product manager for controls and Industry 4.0 for the ACS Group.
“For our own equipment, it’s fairly easy, straightforward,” Gersmeyer said. “We trade data interfaces there, and then for others, for other equipment, it may take a little bit of engineering, but it’s all possible.”
In the future, to make the system more comprehensive, the ACS Group wants the system to access data from external sources of data including sensors and enterprise resource planning systems, Gersmeyer said.
MiVue allows customers to start their IIoT journey by connecting just one asset, such as a blender. They can then easily expand by connecting more equipment to the MiVue platform as future needs arise, according to the company.
MiVue collects data from equipment by connecting to their controllers. A router housed in a rugged enclosure sends information through a cellular signal to the cloud, where it is stored and accessed. Customers can view and analyze the data through an intuitive and colorful user interface that can be accessed remotely on any internet-connected device, such as a PC, tablet or cell phone.
“Cellular is one of the key differentiators compared to other systems that use Wi-Fi or Ethernet networks,” Gersmeyer said. “Cellular is easy in comparison because the installer doesn’t have to assign IP addresses for assets, configure firewalls or set up VPNs in the factory. Once MiVue is plugged in and turned on, it starts communicating. This speeds time to value.”
MiVue will also send email and text alerts to a user’s phone or any web-enabled device.
“We’re also providing some tools to give them [customers] some guidance, things like alarms or alerts,” Gersmeyer said. “Let’s say, for instance, that the dew-point temperature on the dryer reaches a certain level, there’s an alarm created to tell the customer that they need to take some action. We’re also working on some modules for preventative maintenance that tells the customer when they need to change a belt on a granulator or maybe change a bearing on any piece of rotating equipment. … If the platform just provides data, it’s not as useful as it could be. We’re more interested in helping our customers understand what to do with that data, and MiVue will provide some of that guidance.”
MiVue can help customers improve uptime and reduce material and labor costs, he said.
In addition to offering MiVue with all new equipment, the ACS Group offers a retrofit kit for existing equipment. Customers can consult with the ACS Group ahead of purchase to ensure their older equipment is compatible with the system and learn whether a controls upgrade might be necessary.
The ACS Group also will work with customers on custom-built integrations.
Bruce Geiselman, senior staff reporter
Contact information:
MiVue, a division of ACS Group, New Berlin, Wis., 262-641-8600, https://mivue.com
Bruce Geiselman
Senior Staff Reporter Bruce Geiselman covers extrusion, blow molding, additive manufacturing, automation and end markets including automotive and packaging. He also writes features, including In Other Words and Problem Solved, for Plastics Machinery & Manufacturing, Plastics Recycling and The Journal of Blow Molding. He has extensive experience in daily and magazine journalism.
Request More Information
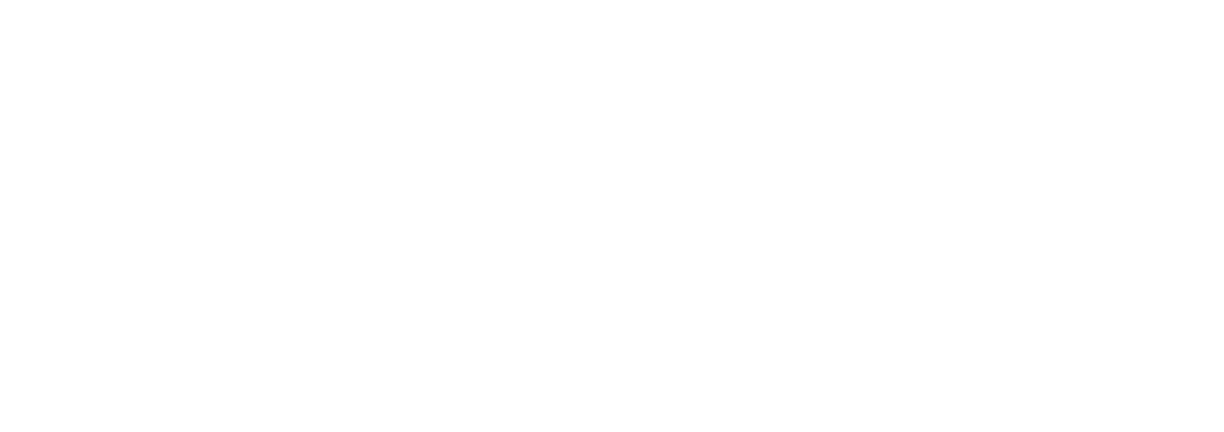