By Logan Montgomery
Technical Sales Manager for Versa Pullers
Hollywood, Fla. – Engineering Resources Group (ERG) is a product and process development company which specializes in automated processes for fabrication, assembly, inspection and testing operations. By working closely with clients to determine the best ways to meet their needs, ERG provides optimal solutions to improve their processes and reduce cost.
As the cost of shrink tubing used in the production of catheters has increased, and supply chain issues caused delivery delays, FEP (fluorinated ethylene propylene) shrink tubing has become a very expensive throwaway item for medical device manufacturers. FEP shrink tubing is used in the manufacturing process for reinforced catheters. Some manufacturers have turned to ERG for machinery to enable them to make the tubing in-house.
It can be a painstaking process working with a delicate feedstock. ERG engineers have developed a fully automated, self-contained process that is simple to operate. One key to their success is a unique puller assembly that adeptly handles the fragile tubing as it enters and exits the process while providing the ability to automate the system.
How the system works
Engineering Resources Group has developed a way to create shrink tubing from regular tubing, through a process that includes pressurization, lubrication, heating, expansion, cooling, washing and drying. The first step of the process involves a Versa caterpillar puller with pneumatic belt closure, pulling the tubing from a spool in a controlled way and presenting it to the process.
Powered by servo motors with planetary reduction gearboxes, the model C-22 pullers are well suited for the task because they provide uniform pressure and consistent feed rates. ERG uses a 40-durometer neoprene belt that is FDA approved, though there are a variety of belt material options to choose from. Although this model can handle speeds of up to 450 feet per minute, the ERG process generally runs at between 10 and 20 feet per minute. Maintaining that speed is critical so that the tubing isn’t stretched or deformed.
After passing through the first Versa puller, the tubing is lubricated to ease its passing through the other system elements. It is heated, then pressurized with nitrogen, which allows the pressurized tubing to expand, then it passes through a water bath for a controlled cooling process where it hardens in its expanded state.
Next it enters a drying chamber, before it is pulled by another Versa C-22 caterpillar puller on the back end, which presents the finished tubing to a special automated cutter where it is cut to the desired lengths while maintaining the upstream pressure in expansion process.
The C-22 pullers apply just enough pneumatic pressure to convey the tubing through the system without deformation. The input and output puller speeds are controlled by the machine controller with the output puller being primary, and the input puller speed offset as needed to prevent stretching of the tubing.
The caterpillar design applies uniform pressure over the entire traction length. Pressure is adjustable, allowing a different grip on tubing with thicker or thinner sidewalls, for example. This adjustable, uniform pressure moves the tubing through the process without any elongation or other deformation. Compact C-22 pullers fit nicely within the machine’s overall envelope, as well.
Pneumatic actuation is key
In addition to the uniform pressure and compact size, a key aspect of the puller design was its pneumatic actuation. Engineering Resources Group chose the Versa caterpillar pullers in part because they open and close pneumatically, allowing the process to be automated for control and safety.
“Whenever there’s an alarm or an error in the system, the expander’s controller sends a signal to open the pneumatic cylinders without stopping the belts,” said ERG President Chris Ross. “Then, once the situation is attended to, we send another signal to close the pneumatic cylinders and get back into production.”
Ross is pleased with the Versa Pullers’ functionality and their longevity. The C-22 has a 2-inch-wide belt with a 9-inch traction length, and a maximum opening of 2 inches, which is plenty large enough for the tubing that ERG uses. Should ERG opt for a larger size, Versa Pullers’ C-44 features a 4-inch-wide belt, a 4-inch opening and a 9-inch traction length, while the model C-418 provides a 4-inch-wide belt, a 4-inch opening and 18 inches of traction length; both are available with pneumatic opening.
ERG began testing them around 2016 and has been using them ever since. Several other pullers they initially considered use hand cranks to manually open and close the feed belts. Though functional, these would not easily allow the automation which is ERG’s hallmark.
Ross knows that Versa Machinery is the ideal companion to Engineering Resources Group’s process automation. “We’ve used them on every machine of this type that we build here,” Ross said. “We use them exclusively. We looked at others, but even if the form and fit were right, without the pneumatic belt opening we couldn’t use them.”
In addition to being ideal for automation, the Versa pullers are built to last. All their pullers include heavy duty steel tables with 3/8-inch-thick steel plate and ¼-inch-by-2-inch angle iron. Custom stainless-steel guarding was added for this medical application. That, along with a durable powder coat paint, ensures they can work for years in some of the toughest environments imaginable. “We’ve replaced some belts as needed, but we’ve never had to repair or service a puller,” Ross said.
With this combination of durable, automated machines from Versa, and Engineering Resources Group’s automation experience and innovation, medical device manufacturers are assured that their shrink tubing will be made efficiently and cost effectively.
Logan Montgomery is the technical sales manager for Versa Pullers, which manufactures puller assemblies and drop-in pullers for OEM and end-user applications, as well as puller systems. For more information, visit www.VersaPullers.com.
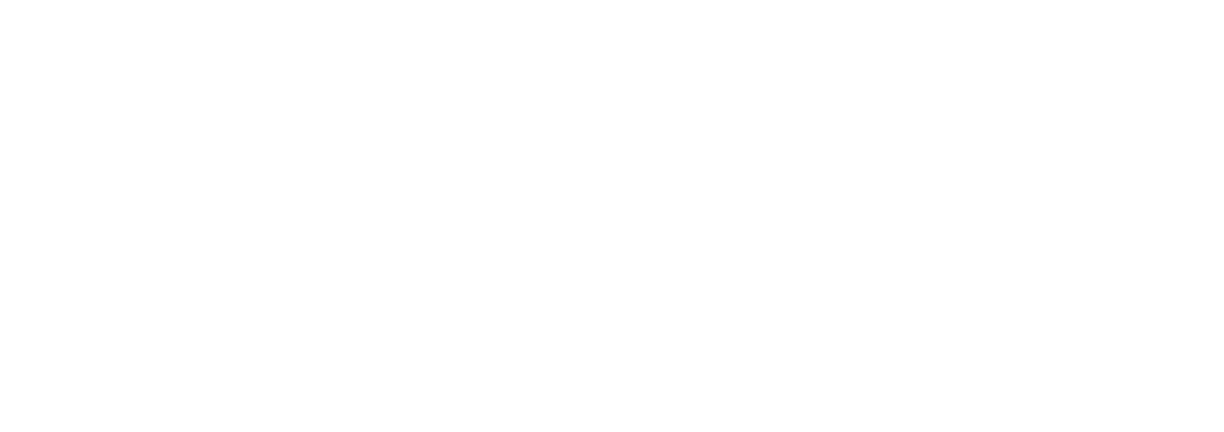