ProAmpac sees flexible packaging as a sustainability solution
Consumer packaged goods (CPG) manufacturers increasingly are switching to flexible packaging in part to improve sustainability, according to ProAmpac, a global flexible packaging company.
Switching from rigid to flexible packaging, such as from detergent bottles to pouches, can reduce the amount of plastic required by 40 percent to 90 percent, and the reduction typically is in the 80 percent to 90 percent range, said Sal Pellingra, VP of global application and innovation development at ProAmpac.
“A lot of brands and retailers have goals of reducing packaging and, more specifically, plastic,” Pellingra said. “Reduction is one of the first priorities of the Ellen MacArthur Foundation as well.”
The foundation is an international organization with a mission to accelerate the transition to a circular economy. Numerous major brand owners and packaging companies are partnering with the foundation on sustainability efforts.
The recent trend, accelerated during the pandemic, of consumers switching from in-store purchases to e-commerce also has accelerated the trend toward flexible packaging, Pellingra said.
Flexible packaging is better suited for e-commerce because it is lighter, occupies less space and can reduce product damage, he said.
Recent interruptions in the supply chain and shipping container shortages are fueling interest in flexible packaging since companies can ship more product in the limited space available onboard ships and in trucks. In addition, the interruptions are driving brands toward regional supply vs. offshore.
However, sustainability remains the key driver.
“Every single conversation with a brand includes sustainability,” Pellingra said.
Most CPG companies have set goals of increasing their use of recycled content by 2025 to somewhere between 25 and 30 percent, Pellingra said. Even some legislation aimed at increasing post-consumer resin (PCR) in packaging aims for that percentage range.
However, one of the challenges companies like ProAmpac face is how they will obtain enough high-quality PCR to meet those goals.
One of the steps ProAmpac and other flexible packaging companies are undertaking is moving toward mono-material films, typically PE in the U.S., that can be recycled. Traditional packaging films often contain layers of different plastics that are not compatible in the recycling stream.
ProAmpac has introduced its R-2000D recyclable laminated PE film that provides a sustainable alternative to multi-material laminates. Designed to be a drop-in replacement for conventional multi-material laminates, R-2000D’s performance characteristics allow it to run at high speeds on form/fill/seal equipment, according to the company.
The company has a number of packaging designs using the film designed for frozen foods, dry foods and pet foods.
One of its most recent products using the film is its Quadflex recyclable stand-up pouch that the company says is suitable for pet food, human food and homecare products. The Quadflex recyclable is pre-qualified for in-store drop-off through PE recycling streams, the company said.
One of the challenges to recycling mono-material PE films has been a lack of recycling infrastructure. ProAmpac partnered with How2Recycle, a nonprofit recycling program, and retail partners to establish a take-back program for the packaging.
However, as of now, recycling PE films in the U.S. is limited to packaging used for dry goods.
“Wet products leave residue, and consumers just aren’t able and willing to clean wet packaging so that it’s clean and dry,” Pellingra said.
Wet, dirty packaging and mixing material packaging can contaminate the recycling stream. The How2Recycle program, which uses a standardized labeling system that clearly communicates recycling instructions, is designed to eliminate those problems.
Chemical recycling, also known as advanced recycling, could hold a key to improving the quality of PCR for plastic packaging.
“Advanced recycling is a much better option because the packaging doesn't have to be clean and it opens the door to more polymer types and combinations, and we know consumers aren't very good at cleaning or sorting packaging when it goes in the bins,” Pellingra said. “It's also infinitely recyclable, where with mechanical processing, you're degrading the product each time it goes through a heat history.”
As CPG and packaging companies adopt sustainable solutions, it will be important they take a holistic approach and realize there is not a single solution, Pellingra said.
“Some people say, ‘we don’t want any plastic,’ ” Pellingra said. “Well, if we didn’t use plastic, then packaging would be all paper or renewable based. Going 100 percent paper or renewable would lead to competition for farmland and the potential for deforestation. Some people say, ‘let’s go to glass.’ Well, glass is heavy and expensive to collect and ship around, and it drives associated increases in energy use and greenhouse gases. It’s not being recycled in a lot of places because of that.”
A combination of solutions will be needed, including reducing the amount of overall packaging, reducing virgin plastic used in packaging, driving toward structures better suited for recycling, increasing PCR content, and using a variety of packaging materials including plastic, paper, metals and glass where each is appropriate, Pellingra said. Most critical will be building an infrastructure for recycling that includes both mechanical and chemical recycling. Much of what is currently produced could be recycled today if the infrastructure were in place, he said.
Bruce Geiselman, senior staff reporter
Contact:
ProAmpac, Cincinnati, Ohio, 513-671-1777, www.proampac.com/en-us/
Bruce Geiselman
Senior Staff Reporter Bruce Geiselman covers extrusion, blow molding, additive manufacturing, automation and end markets including automotive and packaging. He also writes features, including In Other Words and Problem Solved, for Plastics Machinery & Manufacturing, Plastics Recycling and The Journal of Blow Molding. He has extensive experience in daily and magazine journalism.
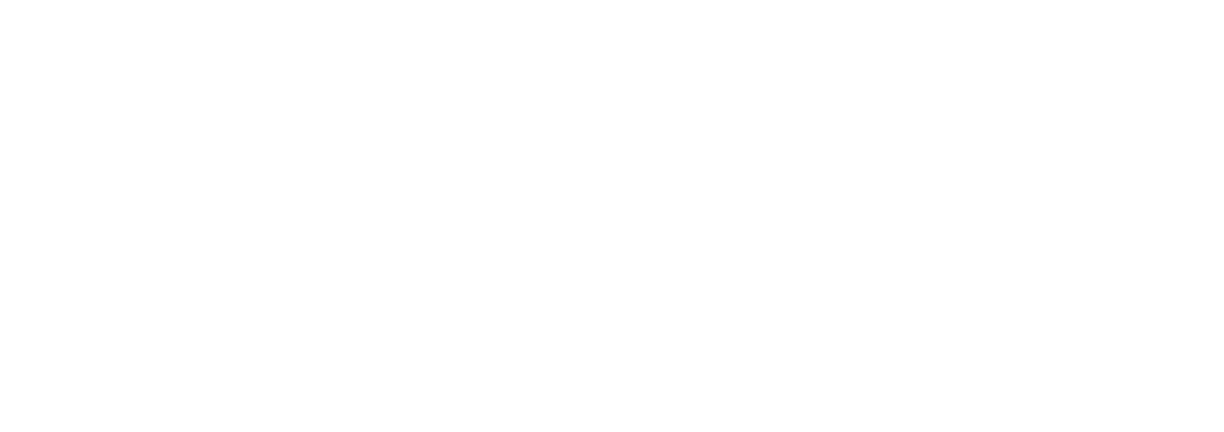