By Roger Landman
Head of product management, SYSPRO
The challenges that the global pandemic created have demonstrated the urgency of digital transformation within the manufacturing industry. Almost half (47 percent) of manufacturing businesses depended so heavily on on-premises systems that they were unable to function and six out of 10 suffered from disruptions to their supply chain, according to a December 2020 survey of manufacturing leaders from SYSPRO.
Unsurprisingly, the study found that manufacturers are evaluating new approaches that could help them avoid similar disruptions in the future. More than four in 10 (42 percent) plan to reshore manufacturing operations to regain control of their full supply chain, and just under three in 10 (29 percent) are evaluating cloud technologies to gain agility and flexibility. Furthermore, more than half (56 percent) are looking into a dual sourcing strategy, which should make the supply chain more resilient, but also makes supply chain management far more complex. Real-time reporting and business intelligence is required to get the full benefit from dual sourcing.
Broadly defined, digital transformation — which entails adapting processes such as digital-twin capabilities, real-time asset tracking and automated equipment monitoring — is critical for enabling a modern manufacturer to become nimble and efficient.
But the digital transformation process is not quick. It’s an enormous undertaking and, with technology advancing so quickly, the process will continue to evolve. To ensure that manufacturers are able to keep up, it’s critical that their core systems be flexible and future-proofed with the ability to interoperate and integrate with future innovations.
Before an organization can implement smart factory technologies this foundation has to be in place, and an enterprise resource planning (ERP) platform is a key part of that foundation. Technology such as ERP can support manufacturers to overcome industry disruptions by providing the systems and platforms that resolve the biggest areas of impact, including: remote workforce enablement, implementation and automation of business systems to handle procurement and sourcing policy changes, distribution and lead time planning; and analytics providing data real-time to support improved decision-making. While there has been downtime, manufacturers have the opportunity now to make a change to improve operational efficiency and thrive now and into the future.
Laying the groundwork for digital transformation
Machinery manufacturers in particular face unique challenges, many of which are long-standing but have been exacerbated by the effects of the global COVID-19 pandemic. Fortunately, a number of these can be addressed as part of any digital transformation effort. For example:
- Customer quotations: One of the leading industry challenges is the cost of generating quotations and improving conversion rates. Manufacturers spend a substantial amount of time calculating costs to generate quotes, which, in turn, creates substantial costs of its own. Ideally, the process will be automated, pulling in costs in an intelligent manner to sharply reduce the amount of time required to generate accurate quotes. Today, there are manufacturers generating quotes for the requestor within an hour of receipt. Without a digital transformation, this would not be possible.
- Ensuring collaboration through the supply chain: The pandemic made it clear to manufacturers that engagement and connectivity in real time between suppliers and customers has never been more important than it is now. One example of this need is increased client demands on the principal contractors. There is an expectation for subcontractors to supply assurances that quality will exceed minimum standards. As a result, subcontractors are increasingly compelled to implement and maintain full-fledged quality-management systems that align with the supplier’s quality-management system.
The right ERP platform can help address the issues by providing manufacturers with standardized processes, and, ultimately, visibility into core financial and business processes. This provides a clear and comprehensive view of activities, so managers can track exactly how their operations progress towards objectives.
Also, a well-designed ERP system can significantly advance manufacturers’ progress toward digital transformation and address functions such as business process automation, remote workforce enablement, procurement and sourcing policy change management, and real-time analytics.
Specifically, plastics machinery manufacturers should look for the following characteristics in the ERP they choose for their digital foundation:
- An integrated Manufacturing Execution System (MES): Planning and scheduling work orders, tracking time and materials, recording output, measuring KPIs — a ton of data flows off the floor. There are many MES systems on the market that do this, but usually, they are separate from the ERP system, requiring the creation of complex integrations that are still limited. An ERP with a pre-integrated MES makes that data openly available to everyone who needs it, when they need it, in one place, and it can be easily fed into artificial intelligence (AI) or analytics for additional insights.
- Seamless CAD integration: If CAD designs are in one system, and the bill of materials in another, engineers often manually enter data between the two systems, which also causes errors and delays. Integrating the two systems makes better use of engineers’ time and also ensures accuracy downstream to production and purchasing.
- Serial numbers tracking and parts location: In heavily regulated industries, traceability isn’t optional, but it can also be useful for tracking and management of inventory, supply chain management and business analytics.
- Product configurator: For machines that are configurable with many options and permutations, most companies only have a few people in sales and technical positions who thoroughly understand the complexities. It’s usually “tribal knowledge” that sits in their heads. This makes helping a customer through a quote a complicated, time-consuming process, with the risk of errors in the configuration that can be passed downstream to purchasing and production. An ERP with a rules-based, web-based configurator streamlines the process and enables customers to customize their own order.
But a modern, cloud ERP purpose-built for manufacturing can do far more. It can readily integrate with Industry 4.0 technologies such as Internet of Things (IoT) devices and AI to provide contextual information in real time, when and where it’s needed. All of these advanced technologies, however, must be tightly integrated into a modern, flexible digital foundation to gain a worthwhile benefit from the investment. This also offers a platform on which additional innovations can be added or built.
Take it step by step
Along with a flexible, cloud ERP foundation, manufacturers should also work with a knowledgeable systems integration partner to help guide the journey, which will most likely be an ongoing process. The partner needs a deep understanding of manufacturing in general, and industrial machinery manufacturing specifically. After all, the government and safety regulations associated with the food and beverage industry are very different from those of industrial machinery, for example, so specific domain expertise is a valuable accelerator.
To make sure the digital transformation journey goes smoothly, take it step by step. First, business managers and IT should work together closely to determine which specific function would show the largest immediate benefit from digital transformation, whether profit-based or resolution of a particular problem. Implement a pilot project in that area as a “learning experience” for the organization. Once it shows value, expand the project into a related part of the plant. Whatever the need, start small and make sure that these new technologies are fully understood before being hooked into the ERP.
Furthermore, never underestimate and certainly don’t neglect the cultural changes that come along with digital transformation. Top management needs to repeatedly communicate and model the changes to team members, explaining how these changes will benefit employees, customers, partners and the company as a whole.
The COVID-19 pandemic has presented the entire industry with a very difficult exam. By learning from the pandemic, organizations that have been slow to digitally transform have new incentives to start their journey. Manufacturers can emerge even stronger than before as long as they first build a strong digital strategy, work with a knowledgeable partner and take a long-term view. The entire industry will be better for it.
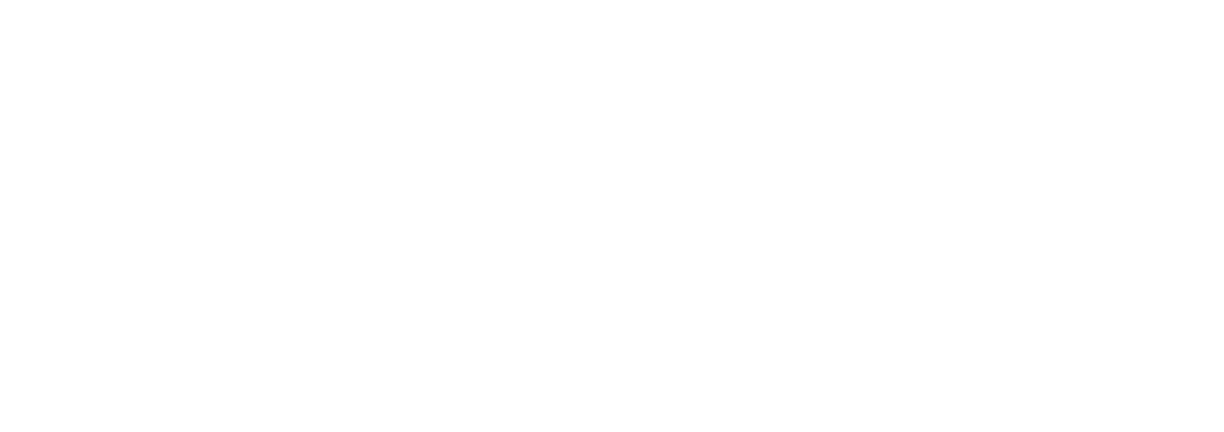