At custom injection molder and contract manufacturer Ferriot Inc., bigger is better — and necessary.
Officials there have been working mightily to install its largest injection press ever — a 2,250-ton Negri Bossi Bi-Power, parts for which arrived in January and required a fleet of five 18-wheeled trucks, the company said.
Ferriot poured a new concrete foundation to accommodate the weight of the machine; just one of the machine's components, for example, weighs 70 tons. The entire machine weighs 231,480 pounds. Now the cell is complete, equipped with a Conair Carousel Plus W400 dehumidifying dryer, a Kuka six-axis robot and a conveyor. The entire system illustrates sophisticated integration for a company whose clients demand precision parts that are as close as possible to perfect.
A FIRST IN THE U.S., WELL-INTEGRATED
The Kuka robot isn't an unusual addition, especially for an injection molding operation whose end goal is to equip each of its machines with robots. The robot is capable of removing structural foam panels sized 30 inches by 36 inches, which make up the front of gas pumps used in commercial gas stations. The novel step that company officials took was to integrate a Sytrama SCP2 control with the Kuka, and this is the first combination of its kind in the U.S.
It is a universal robot controller from a sister company of Negri Bossi, and the goal is to see if Ferriot can make programming the robot easier for its technicians, said Bob Brook, maintenance manager.
President Craig Ferriot said that internal and external components came integrated with the Negri Bossi machine, and that was by design. The controls are very intuitive, Brook said, so that technicians within their shop do not need a lot of training to work comfortably on them.
The Bi-Power press has an integrated Columbia industrial PC with two CAN bus outputs. Negri Bossi sourced and assembled this unique mix of off-the-shelf components, which include a 32-zone hot runner control, six hydraulic valve gates, six air valve gates and extra core sets. Intuitive controls for workers makes for a smooth learning process.
"I think we're getting smarter and smarter, not only at the machine level, but at the mold level, with things that you have to build into the mold as well," Ferriot said. "Today we run some highly complex tools that, if you do not have a tight control on your process, you are not making a good part. When you're making a part that then requires secondaries like paint, you are talking about part prices that are $85 to $100 a piece. You do not want to make too many mistakes on something like that. You have to know what you're producing; otherwise you are generating an awful lot of scrap."
The key with injection molding production today is how quickly the machine can be changed over from part to part, and that is where intuitive controls play an even bigger role.
"When you bring up the control, you can set everything off of those controls so it is much easier to recall your process and set up your process instead of going around to a bunch of auxiliaries that you have to then set up," he said. "It is all about how fast you change over, get the next part in if you're going to try to take advantage of extra capacity."
The company does not buy standard machines, Ferriot said, and that is due in large part to the demands it faces in product design. Think about the front portion for a gas pump housing that is molded from structural foam but then requires 87 inserts front and back; or a structural foam part that makes up the housing of a laser etching machine that is used in the consumer and professional engraving markets. Ferriot is under pressure to add more molded-in features to the plastic parts to reduce the cost of assembly, for example.
"It forces the product design to be more complex, requiring more complex tooling, that then in turn requires more complex machinery to produce the part," he said. "With the new machines, we have a lot of integrated controls within that system that allow us to manage different features within that tool set. That is not only core pulls, but valve gating, whether they are hydraulic or pneumatic; we've got temperature controls that are part of the machine so that instead of buying all these auxiliary pieces, they are all completely integrated.
"The integration allows us to do a lot more at the control level to make it easier and quicker for us, but also more price competitive when they integrate things versus when you buy them separately," he said. "In fact, we have four or five different styles of Negri Bossi [machines], so we've aligned ourselves purposely to truly try to look at one or two, maybe three, machine controls. They are different levels, different ages, and about every five years they go through a redesign on the control level. But you do not want to get too many different types of machines out there. You are trying to train your people, and if they have to remember all the idiosyncrasies between controls that makes it more complex and now it requires a higher-skill-set individual to deal with it."
Ferriot said his company retires older assets and brings on a couple of new presses every year or two. The management team works with the board and the sales team to compare notes on what they see ahead. They gather the intelligence and decide what strategically makes sense for the company.
Officials carefully consider long-term viability. "We like relationships that are not fly-by-night," he said. "Ferriot has been very fortunate to have long-standing relationships that span over 10 years, with close customers. When we are looking at growth, we are looking at large growth in large ranges. If we're going to invest our time and effort we're looking at those customers where we can return on those investments many fold, we're talking seven-digit numbers. We know that not everything fits into a large press, but we look at their product portfolio plus a portfolio of other customers to decide what is perhaps a better fit for that asset. That all goes into the decision-making in terms of what we want to invest in. It's also the infrastructure in the company; how large of a press can we support, building-wise, in terms of cranage and building structure. We are at our limit now without putting some more reinforcement into the building. This is about the largest press we can put into this facility."
Brooks said that every time the company buys a new machine, it means purchasing an entire cell. "We are into making cells," he said. "And everything will have a robot on it."
Among its 20 injection molding presses, there are a lot of different flavors, he acknowledges. These include Arburg, Niigata and KraussMaffei.
"We wanted to not necessarily pick one manufacturer but mostly our thinking is that we're probably going to stay with Negri Bossi," he said.
WIRELESS COMMUNICATION FOR EFFECTIVE ERP
An IQMS machine interface unit (MIU) adorns the top of the Bi-Power, allowing the machine to communicate wirelessly with Ferriot's IQMS enterprise resource planning (ERP) software. Officials said that transmitting data in real time is critical, both for the ERP system and for statistical process control (SPC). The data can be viewed both on the production floor and in offices with regard to the state of jobs that are running on the press. The
supervisors can monitor the press performance and react to issues that arise, minimizing downtime and scrap.
Ferriot implemented the ERP system in 2015 as part of its overall business strategy from front office to back office, said Dave Harman, director of sales and marketing. All the machines on the plant floor are tied into the ERP. The MIU allows the Bi-Power to have onboard, remote diagnostic capability. Via the Internet, Negri Bossi can look at each one of its machines, examine any alarms, and watch the process run from afar to help diagnose the problem.
"If they are sending a service guy in, they can come prepared with some spare parts, and try to minimize any downtime," Harman said. "If we have any downtime issues that we are experiencing, they can come through the MIU system and that allows them to troubleshoot."
Executing a plant floor redesign
Construction of the cell is part of the company's longer-term plant redesign that will allow it to use floor space more efficiently, boost labor productivity, simplify movement and flow of work, and ease supervision, officials said.
The goal of the master redesign, which is scheduled to be completed over the next 16 months or so, is to create more efficiency and give the company the ability to make the best use of the space — about 100,000 square feet of space is dedicated to housing 20 injection molding machines and the requisite equipment.
"We feel that by rearranging the equipment, not only will we have better product flow, but better ability to manage the floor because you do not have to walk as far in order to manage what is going on across all those assets," Ferriot said.
NEED SPURS IN-HOUSE INNOVATION
Think about the gas pump panel that requires more than 80 inserts. How does a molder ensure that all of those inserts are in place and that nothing is missing? A sophisticated vision inspection system would be needed, but Ferriot couldn't find one to meet its needs. The company needed to make sure it had a fail-safe way of ensuring that every one of those inserts is installed in the proper location. In-house innovation led to a vision inspection system that examines different quadrants and identifies when something is missing in a given area.
"We started down a path where you had people checking people, but operator accuracy is not 100 percent, as much as you might think," Ferriot said. "It was born out of a need, and we needed a way of detecting whether all the inserts were in their proper locations. Our engineering, manufacturing and quality teams got together and started to use some of the technology available today and put it together in such a fashion that allowed us to quickly insert the bezel and look at both sides and tell the operator exactly if something was missing, and in what location was it missing."
In addition to its custom products, Ferriot also has a line of its own proprietary products. Its American Original injection molded siding, which comes in shake and scalloped styles, is used in construction, primarily residential, and it is growing and expanding that brand.
"We have dedicated sales forces expanding our brand, and we actually are investing in research and development of brand-new products right now," Ferriot said. "We plan to introduce a new product this year, to expand our product portfolio, plus we also are looking at other private-label opportunities."
Angie DeRosa, managing editor
Contact: Ferriot Inc. Akron, Ohio, 330-786-3000,
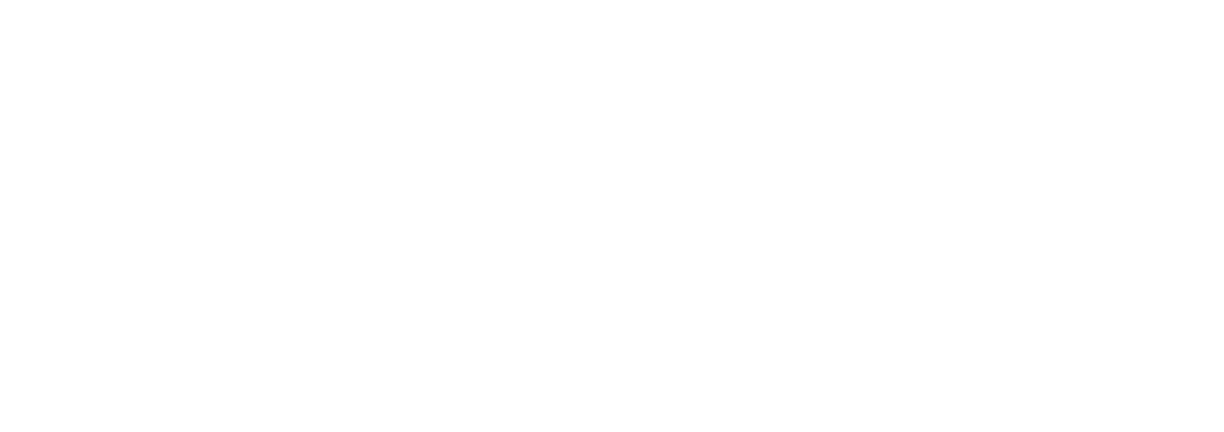