Problem: A custom injection molder began seeing its lone coordinate measuring machine (CMM) struggle to keep up with demand for part inspections.
Solution: Adding a structured blue light scanner, which increased capacity and gave new capabilities to the company’s metrology lab.
Companies that use Total Quality Management principles to create products need to be able to “show their work” to customers. George Popov, quality supervisor at Akron, Ohio-based Ferriot Inc., is one of the people who makes sure his company meets those standards. Ferriot is a full-service contract manufacturer and injection molder with more than 150 employees and 20 injection molding machines running in its 200,000-square-foot facility.
As demand for inspections grew, Popov saw it begin to strain his department’s capacity. “We became the bottleneck … to getting throughput,” he said.
“We had just one major piece of inspection equipment. And so even though the CMM is very accurate and a very precise piece of inspection equipment, just knowing we didn’t have a backup piece of equipment … was a huge concern to us,” Popov said. “So, if the CMM went down for any reason, we would have to farm out the inspection activities to an outside metrology company, which would be very costly to our organization.”
Popov's quality department is responsible for performing part inspections whenever a mold is received at Ferriot, or when parts undergo engineering changes — a volume of work that made expanding its capacity a necessity.
He said that as the team at Ferriot began researching new equipment, it considered portable scanning arms as well as laser scanners and vision systems.
“And not to say those other products wouldn’t have worked, but a number of factors really aided us in our decision” to choose the Aicon SmartScan from Hexagon Manufacturing Intelligence, he said. One SmartScan competitor “had proprietary software, whereas [SmartScan] has third-party PolyWorks software — that was a big one for us,” Popov said. Those considerations, combined with a lower year-over-year maintenance cost and a sale promotion, helped solidify the decision to choose SmartScan.
Ferriot has been using the scanner for almost two years now, and while the scanner is faster than the CMM, each has its own strengths. “What the scanner can’t see, it can’t scan,” Popov said. “The CMM is able to get into deeper pockets and areas that the scanner cannot get to with the cameras.”
The two pieces of equipment complement each other. “You can use the scanner in conjunction with the CMM, scanning and measuring everything you can, and leaving the rest to the CMM,” he said. Using both has allowed the metrology lab to increase throughput, and “gives us the flexibility to complete more tasks than we ever have been able to do before the scanner acquisition.”
As an example of the difference in speed, he said a part that has 50 dimensions to be checked could take from four to eight hours to be physically probed by a CMM, while that same part can be scanned relatively quickly, and the inspection conducted in the PolyWorks software in potentially half the time. While it’s tough to quantify how much SmartScan has helped his company, Popov estimated they have seen “anywhere from, I would say, 40 to 50 percent increase in throughput, which is what we were promised.”
The scanner also offers flexibility. While parts are usually put on a turntable to be scanned, the SmartScan can be rolled onto the shop floor for such tasks as scanning tooling inserts or larger molds. Ferriot has conducted this type of inspection to determine if steel was cut properly in cases where it is investigating what has caused large dimensional discrepancies.
Another advantage is its ability to scan and store 3-D part data. “That helps us reduce space used up at our facility, space we wouldn’t have if we had to store every physical part we produced and inspected,” Popov said.
While CMMs and scanners function differently, the biggest difference may be how they can present their results. Popov said CMMs are very accurate and precise, “but it’s a lot of numbers. It gives good, accurate data, but it doesn’t give you an image. And you know … in our minds, a picture’s worth a million numbers, right?” he said.
With the PolyWorks software, users can introduce a color map to the scanned image, showing where and by how much it deviates from the CAD model of an ideal part.
This pays off when communicating with customers.
Popov told the story of a medical customer with problem parts. The customer had questions about the data Ferriot was providing and requested a meeting. “They wanted us to present to them and prove to them that the numbers are legitimate,” he said. Using color maps and virtual inspection tools, Popov was able to overlay the scanned image on the CAD model and show exactly where the problem was.
“You can see it’s warped over here, it’s fine over here. They were able to see all that. You can’t explain that with CMM numbers.”
“And without those pictures … we would have a much harder time delivering that message,” Popov said. “So, they left that day very pleased — not with their part, but with the fact that yes, our inspection is doing exactly what we told you it would do.”
David Tillett, associate editor
Contact:
Ferriot Inc., Akron, Ohio, 330-786-3000, www.ferriot.com
Hexagon Manufacturing Intelligence, North Kingstown, R.I., 800-274-9433, www.hexagonmi.com
David Tillett
Associate Editor David Tillett writes and edits for Plastics Machinery & Manufacturing, Plastics Recycling and The Journal of Blow Molding. He covers new products, industry news, patents and consumer and business equipment. He has more than 20 years of experience in daily newspaper, online and magazine journalism.
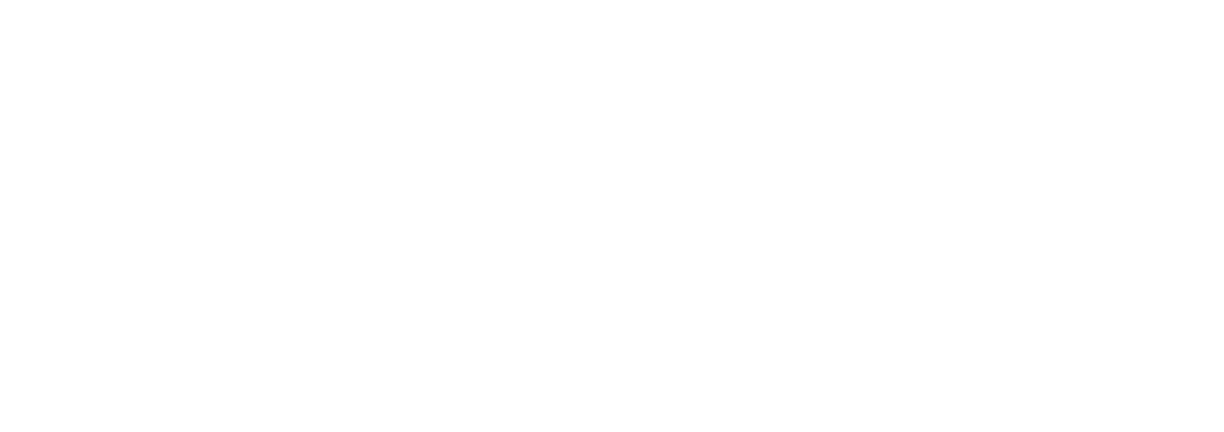