Problem: An injection molding shop needed to meet demanding part requirements and add labor at a time when labor’s been in short supply.
Solution: Following the lead of its corporate sibling, mold maker Industrial Molds, Pyramid Plastics has been adding Yushin robots.
By Karen Hanna
As corporate relationships go, mold making shop Industrial Molds leads its sibling — custom injection molder Pyramid Plastics — in an unlikely category: automation.
“We all kind of grew up at Industrial and worked at Pyramid, which is something we own,” Peterson said. “But a year and a half ago, we rebranded Pyramid Molding Group and really are trying to focus on the plastic side of the business.”
Paired for decades under a variety of names, Pyramid Plastics and Industrial Molds offer customers the ability to oversee part evolution, from concept through tooling design and manufacturing.
In August, 44 people were working at Industrial Molds, which creates some of tooling that Pyramid Plastics uses at its campus 10 minutes away. Automation allows the tool shop to perform some lights-out operations, so production doesn’t have to stop when the staggered shifts that run from 5 a.m. to 5 p.m. are over. The companies serve a variety of markets, including the automotive, consumer, medical and water-metering markets, Peterson said.
But while Industrial Molds has long had automation, Peterson said Pyramid Plastics at times had different leadership and priorities.
“[At] Industrial, we’ve been doing automation since early 2000s, everything from graphite-cutting, high-speed milling and electro machining, or EDM,” he said. “With it, we really have incorporated to be more than just a tool changer or workpiece changer, but it’s part of our whole quality process, integrated into howAs an example of how robots are now helping the molder, Peterson pointed to a YCII-400 take-out robot Pyramid Plastics added in February to handle a clear part made from Tritan copolyester and Lexan PC.
The appearance of the part — used for shelving in appliances — is important to Pyramid Plastics’ customer, but workers originally tasked with removing it from the press struggled to maintain its good looks.
The robot has provided a way to avoid marring the surface of the part, Peterson said.
“It is pulling clear parts out of the press using special suction cups, so, there’s no [finger]prints or marks on the part,” he said. “It goes into high-end components, and they can’t have any fingerprints or scratches.”
Shepherding Pyramid Plastics through its automation journey is Steve White, Central/Midwest regional sales manager of for Yushin America Inc., Cranston, R.I. In the last year alone, Yushin has supplied the molder with four robots, including the YCII-400 and a robot for each of three new LS Mtron One IMMs, added as part of a long-term upgrade that's so far required an investment of $1 million.
With the company’s purchase of a CT 500 traverse robot and two YCII-800 take-out robots for the presses, Pyramid Plastics is following a trend Yushin has noticed over the last few years. Robots are hot. White repeated a discussion he’s had frequently: “I need a robot because people aren’t showing up. I need a robot. ‘What are you going to use it for?’ I don’t know, I just need a robot.”
But while Pyramid Molding Group initially sought to address labor needs with automation, it’s now anticipating a different sort of result — a new generation of workers won over by robots.
In tours the company has hosted for students from nearby Rockford Public Schools, robots have made a big impression, said Becca Peterson, director of sales for Pyramid Molding Group.
New technologies make a compelling case to youths already interested in manufacturing, she said.
“We’ve been showcasing our automation to all the local high schools. We’ve had a few in for job shadows and plant tours because we want them to see that there’s just a lot of new technology; plants are bright and clean and organized,” she said.
Andrew Peterson, Becca Peterson’s husband, agreed. A sibling rivalry to add automation can only pay dividends for both Industrial Molds and Pyramid Plastics.
“Originally, it definitely decreased our labor and headcount,” he said. “But, then, as it's matured and gotten better, it’s actually adding headcount, because we’re able to be competitive. We’re obviously growing from that standpoint, so today I don’t see it as a thing that replaces jobs; it actually enhances and adds jobs.”
Karen Hanna, senior staff reporter
Karen Hanna | Senior Staff Reporter
Senior Staff Reporter Karen Hanna covers injection molding, molds and tooling, processors, workforce and other topics, and writes features including In Other Words and Problem Solved for Plastics Machinery & Manufacturing, Plastics Recycling and The Journal of Blow Molding. She has more than 15 years of experience in daily and magazine journalism.
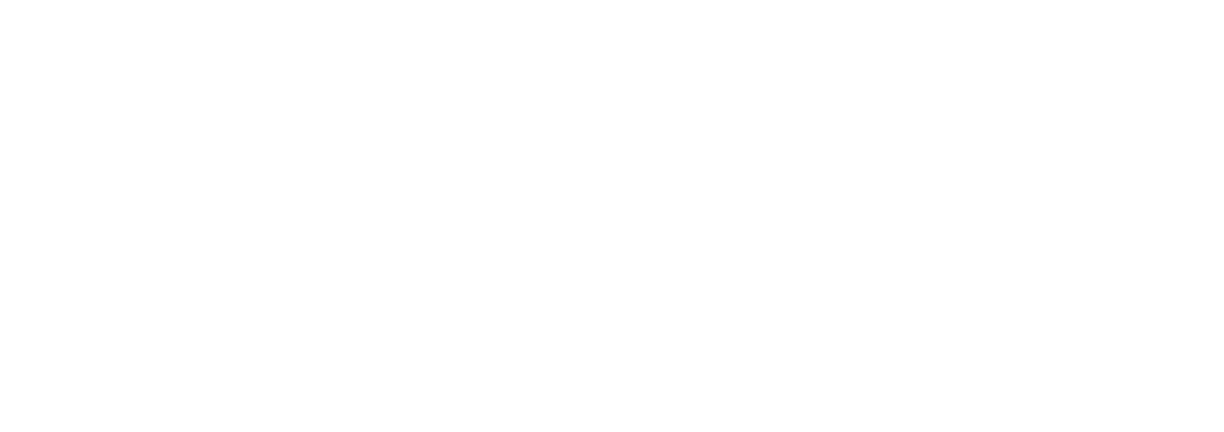