Problem: Workers at Plastic Molding Manufacturing’s plants were losing time deciphering paper startup sheets and wandering between machines and quality-control offices.
Solution: Systems created by the company allow workers to access and share more data directly at the press.
By Karen Hanna
The TPU dental parts the South Bend, Ind., plant of Plastic Molding Manufacturing (PMM) was making weren’t coming out of the machines well. The normal process to resolve the problem — which used to involve scheduling a meeting with the customer in an area away from the presses — could have taken a bite out of production time.
But the company is working on polishing up its practices — with new systems that allow it to respond to problems with fewer disruptions.
“I couldn’t get a machine to run good parts. It was rubbery parts. So, I conferenced in our customer, and I conferenced in our supplier,” manufacturing manager Ben Schelling recalled. “And I would say within an hour, hour and a half, I was able to run good parts.”
Over the past 12-18 months, PMM has upped its technology game, with two systems designed to make quality control and data sharing easier. They include real-time machine monitoring systems (RMMS) that have replaced paper logs at many of the company’s injection molding machines (IMMs), as well as the system that Schelling recently used — a mobile, real-time sampling system on a cart.
Using help from the cart’s two cameras, Schelling was able to communicate with his company’s partners to identify and address the issue, allowing all of them to collaborate quickly on a fix. The part in question was about 0.5 inch long, he said, “but then you zoom in, and it’s probably a 16th-of-an inch ring that we were looking at.”
“We basically trouble-shot as if they were standing there next to me,” he said.
Chris Klotzbier, the company’s VP of growth and expansion, said the live video feed gave everyone, both inside the plant and out, the opportunity to see firsthand what was happening.
“Prior to the carts, we would take pictures with a standard camera and email them to customers and set up a conference call in the office,” he said. “With the RSS carts, we can conduct a conference call right at the machine and use the high-resolution cameras to provide real-time video of the parts as they are manufactured and inspected.”
“It's helped move our operational efficiencies to a next level where we’re cutting down on time to do these qualifications and to ensure that parts are of good quality,” Klotzbier said.
Based at PMM’s headquarters in Hudson, Mass., where the newest two systems were first trialed, Klotzbier said the company has been focused on “optimizing efficiencies” at all four of its plants, including locations in Pennsylvania and Connecticut.
With about 200 people and 110 IMMs ranging in size from 50 tons of clamping force to 650 tons, the custom molder makes parts for customers in the medical, automotive, defense and water-filtration industries.
“We have a few different initiatives going on internally, that [are] self-driven in a way, just to make sure that we’re operating at full efficiencies and optimally,” Klotzbier said.
Both systems were born out of a desire to cut the amount of time technicians, quality-control staff and operators would need to move from one location to the next to access information.
Prior to adding RMMS to presses at South Bend, for example, operators used paper logs to access set-up sheets and information for troubleshooting.
But, Schelling said, “If the paper got lost, or got soiled, because of all the people’s fingerprints … people would have to wait till I got back into the office to print another copy.”
Now, 14 of the plant’s 29 IMMs have RMMS hookups to the company’s ERP system; Schelling expects the other 15 presses also will be upgraded.
“It’s basically putting our ERP system in the hands of our employees right at the machine itself, which is extremely helpful,” Klotzbier said
Quality-control processes, too, are more efficient, he said.
“Our technicians and our quality people can go to the actual machine where the part’s running, check the diameters, verify the critical measurements, and then document them right there at the machine,” he said. “Whereas [what] used to be done, you’d pick up the part, you’d walk into the quality room, you put it on the table and start measuring it that way.”
With easy access to machine data right at the RMMS, engineers can more efficiently identify and fix problems and optimize cycle times.
The improvements have allowed workers to spot problems sooner, Klotzbier said.
“Instead of running 100 or 500 parts that are not meeting specifications, you might only run 10, 15. … In some cases, it’s led to shorter lead times because we can find issues quicker and so we’re more prepared to solve them and get parts out the door in a much faster manner,” Klotzbier said.
Designed to improve internal efficiency, the new systems could create satisfaction both inside the plant and out.
Workers at the machines now have access to more information and might feel empowered to move into different roles. The changes come at a time when PMM, like many companies, is still struggling to fill all its positions.
“I think it gives them a way to really learn on the job above and beyond what their standard responsibilities are,” Klotzbier said.
Some machine operators have exploited that opportunity to build their own skills and move on into supervisory roles, he said.
Customers will appreciate the new systems, too, Schelling believes. Being able to work directly and immediately with the customer while it was waiting on its rubber parts, he said, was “good relationship-building” on both sides.
Karen Hanna, senior staff reporter
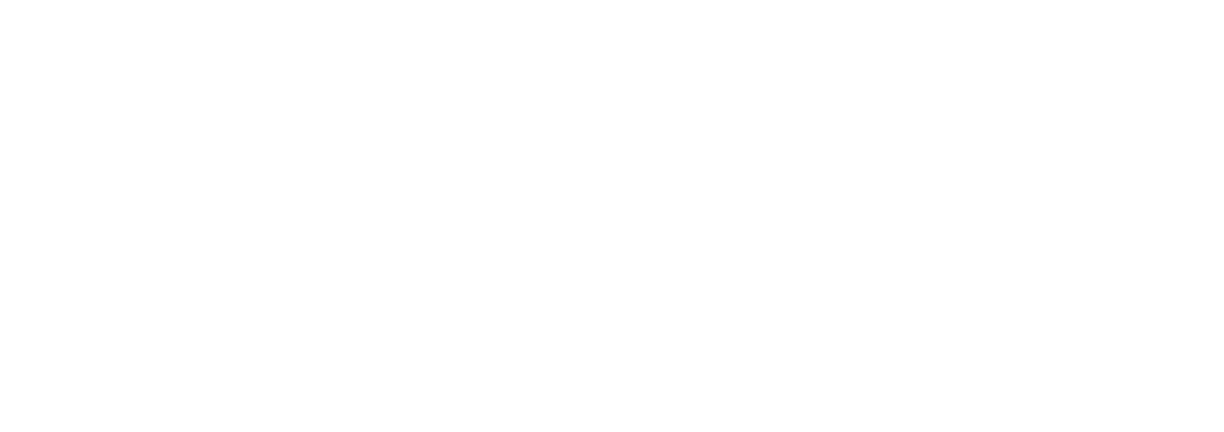