Problem: A custom molder was looking for ways to better use its employees’ skills.
Solution: A used six-axis robot has been assigned to part separation, while employees are being redeployed.
By Karen Hanna
Just days after flipping the switch on Champion Plastics’ newest technology, company President Mike McDermott already had bright plans for the future of the new-to-him Kawasaki robot currently humming along separating mirror-image parts out of the mold.
“The new six-axis robot has been running for just about a week and has already exceeded our expectations,” he said. “We had no issues with implementation, and we have had zero downtime. As such, we are already making plans to have additional projects run on this cell to eliminate the need to use repetitive labor with the goal of expanding it to run in a ‘lights-out’ scenario.”
The Auburn Hills, Mich., custom molder, which makes clips, fasteners and retainers for the automotive industry, has been focused on optimizing the work of its 25-member staff as it juggles new jobs in the pipeline. The plant — named in honor of founder and three-time Olympian Terry McDermott, Mike’s father — recently made the leap from Cartesian three- and five-axis robots into its first spherical robot with its adoption of the Kawasaki, an RS010N A, in anticipation of future orders.
Champion Plastics runs 11 injection molding machines (IMMs), with clamping forces ranging from 85 tons to 300 tons.
In the spring, it landed a new job that would involve molding left- and right-sided components. Mike McDermott also knew other jobs were in the works. But, with robot supply tight due to ongoing supply chain problems, a conversation with an industry source proved propitious.
At the time, McDermott was touring JH Automation, a Port Huron, Mich., automation supplier and integrator that was making end-of-arm tooling for Champion Plastics.
As luck would have it, JH Automation automation engineer Jeff Hendrickson had a robot he was looking to unload. He recounted the conversation that introduced McDermott to the Kawasaki.
“ ‘Are you interested in a six-axis [robot] instead of the top mounts that [you’ve] been using?’ Hendrickson recalled. “And he said, ‘Yeah, we’ll give it a whirl.’ ”
That solved a conundrum for Hendrickson, who had taken the Kawasaki back from a Flint, Mich., molder that had used it for only a year and a half. At its first home, the robot had been pressed into service in a role that didn’t quite fit.
“It was a production thing. It was almost a prototype; they were trying to experiment with something, and they were just trying to run it faster and faster and faster, and it got to the point where it just really never did what it was supposed to,” Hendrickson said.
He and McDermott both expressed optimism the Kawasaki — which has a reach of nearly 5 feet and a payload of 22 pounds — would prove a winner at its new home at Champion Plastics.
Back in April, Hendrickson was anticipating setting up the robot and teaching Champion Plastics’ personnel how to use it. Proof of success would come not in the robot’s initial setup — which Hendrickson handled — but in the planning of the subsequent jobs Champion Plastics already hoped to take on.
“The training is about another day to get them used to starting it, stopping it, moving it around, that type of thing. I don’t know that they want to get involved in programming, but if they do, then it would be additional training. But pretty much, you can learn how to run one of these things and maneuver it in a day,” Hendrickson said.
Given the robot’s history, Hendrickson also had a warning for any company taking steps toward robots with so many axes: Learning to use them takes some expertise.
Compared to gantry robots, “it’s a totally different animal,” he said.
An integrator of ABB, Fanuc and Kawasaki robots, Hendrickson is partial to Kawasaki.
“To me, it has a simpler form of language for programming. Some of the other ones, they’re a little bit, a little more difficult to operate. … They’re all about the same, but they have their quirks,” Hendrickson said.
In the spring, the labor shortage was keeping him busy.
“We have people that basically don’t want to go to work; they don’t show up. So the customers ask, ‘Hey, can you put a robot on here?’ ” Hendrickson said.
At Champion Plastics, where the Kawasaki is now installed on a 200-ton Toshiba IMM, the freedom the robot offers goes beyond the movements its arm can achieve — it’s going to give the plant the flexibility to juggle more work, too.
“We’ve redeployed labor, that’s, I don’t want to say less meaningful, but pretty repetitive and non-value-added. And we can move our very valuable employees to do something that is more valuable, more value-added on the floor,” McDermott said.
The changes are ongoing.
“We do have more jobs in the pipeline, mostly left-hand/right-hand separation, and, with that in mind, cell packing, packing the part, removing an operator. The robot helps with labor, and labor is a big issue right now,” McDermott said. “So, that’s why we went with the robot.”
The Kawasaki RS010N A robot will be busy — eight more programs are headed Champion Plastics’ way.
Karen Hanna, senior staff reporter
Karen Hanna | Senior Staff Reporter
Senior Staff Reporter Karen Hanna covers injection molding, molds and tooling, processors, workforce and other topics, and writes features including In Other Words and Problem Solved for Plastics Machinery & Manufacturing, Plastics Recycling and The Journal of Blow Molding. She has more than 15 years of experience in daily and magazine journalism.
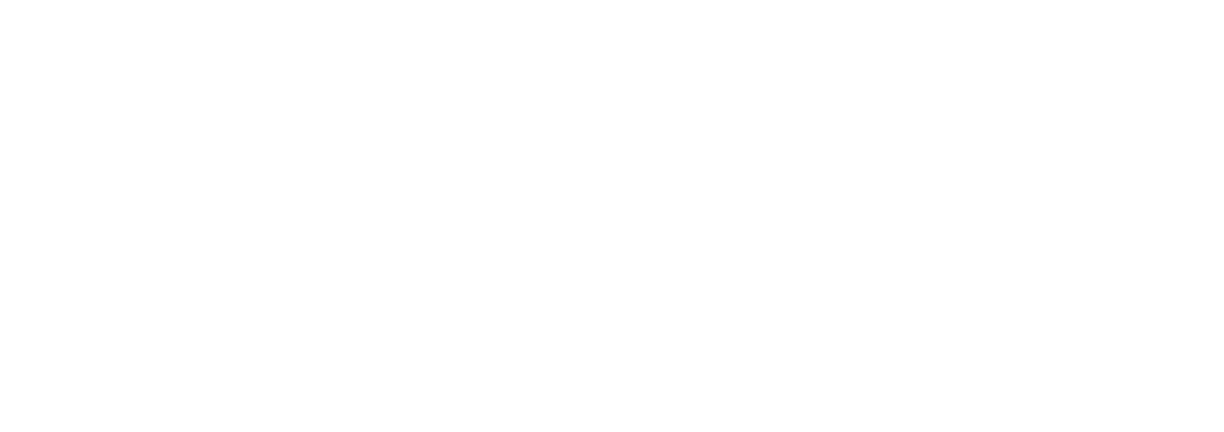