Demand for sustainable packaging gives rise to new foaming method
By Karen Hanna
Foam fortification that helps coffee cups handle the heat and gives stiffness to packaging without requiring extra plastic is the goal of a new process being evaluated by two foaming heavyweights.
Bockatech, the company that licenses EcoCore, a unique process that has used chemical foaming to foam parts as the injection mold opens, is working to incorporate MuCell, a physical foaming process, into its repertoire.
Representatives of Bockatech and MuCell maker Trexel said rising demand for more sustainably made parts, along with rising resin costs, have created an expanding market for foaming technologies. Their collaborative EcoCore-MuCell process — which could result in commercial applications next year— opens new possibilities for molders.
“Bockatech … started with chemical foam; their first few parts were done with chemical [foam],” said Trexel President and CEO Brian Bechard. “They always had a plan to look at physical [foaming] because they understood that physical has some advantages [like] volume and also being able to basically start with a thinner part.”
EcoCore’s foaming action occurs in all directions as the mold opens, rather than along just one axis, like other foaming processes, which take place within a closed mold. While one-axis foaming tends to work best with less-complex shapes and flat parts, the EcoCore process is suitable for producing a host of products, including housewares, and construction and automotive products. But packaging, including industrial products such as pails, reusable and single-use packaging for food, and caps and closures for consumer goods are Bockatech’s main focus, said Martin Blacher, the company’s director of sustainability.
Blacher said the company’s process is made possible by patented materials and molds.
With the inner wall of the part still on the mold core, the part foams outward.
“It differs from traditional foam molding because we open the mold before the resin has fully solidified. Foaming is controlled by retaining the molding on the core as the mold is opened to prevent the internal surface expanding, and controlling the expansion of the surface on the cavity side of the mold by varying the material blend, processing parameters and wall design,” he said. “This enables very large density reductions without sacrificing mechanical performance of the part.”
According to Bockatech, EcoCore provides a number of advantages over traditional molding. For example, EcoCore parts require 70 percent less material than solid-walled products and are 5.5 percent stiffer, with 1.2 times more protection against heat transmission.
In addition to the fast cycle times and EcoCore’s potential for producing well-insulated parts, Blacher cited “high strength-to-weight ratio, low cost, durability [and] low set-up cost.”
Physical foaming creates new opportunities for producing EcoCore parts, Bechard said.
“Physical foaming, which is what MuCell is, uses nitrogen, and nitrogen is a much more aggressive foaming agent, so it allows for a lot more expansion,” he said.
Because it requires a one-time purchase of MuCell equipment, physical foaming is initially more expensive than chemical foaming, but users can realize cost savings over time, because they no longer have to buy chemical agents. That makes physical foaming a reasonable choice for high-volume parts, as well as for parts that require greater amounts of foaming than chemical foaming agents would provide, Bechard said.
“This is a really exciting partnership. They’ve got a really great technology ... the parts that are being produced have some real benefits. Think of how many parts that would benefit from a little bit more thickness and insulation without needing more material,” he said.
With the EcoCore process, molders can foam even more complex shapes with shorter cycle times than the applications might have required using MuCell alone, Bechard said.
“What Bockatech allows us is a more complex shape to be molded in this way that basically you end up with a thicker part. ... For the same weight, you’ve got a thicker, more rigid part that has some insulation capabilities,” he said.
In talking about the project, Bechard stressed two main benefits: the ability to produce parts that provide a high degree of insulation without using much material, and sustainability.
While, so far, the partners are focused on PP, other resins also could work.
“I think we're getting to a point in packaging where maybe cost isn’t the most important thing, and having a good sustainability message and story, it’s important. There’s no additives here. And it’s straight polypropylene, so that it’s fully recyclable. But a lot of what Bockatech is looking at, in addition to just single-use stuff, is reusable containers, because you can make a nice, thick, aesthetically pleasing, stiff part that can be reused,” Bechard said.
As work on the EcoCore-MuCell process is still gaining steam, chemically foamed EcoCore products already have achieved a high profile — cups foamed by Bockatech’s process were on display at the 2021 United Nations Climate Change Conference, also known as COP26, where one of the company’s foamed Zero Waste Cups was photographed on the table in front of President Biden.
Karen Hanna, senior staff reporter
Contact:
Bockatech, Llantrisant, Wales, www.bockatech.com, [email protected]
Trexel Inc., Wilmington, Mass., 781-932-0202, https://trexel.com
Karen Hanna | Senior Staff Reporter
Senior Staff Reporter Karen Hanna covers injection molding, molds and tooling, processors, workforce and other topics, and writes features including In Other Words and Problem Solved for Plastics Machinery & Manufacturing, Plastics Recycling and The Journal of Blow Molding. She has more than 15 years of experience in daily and magazine journalism.
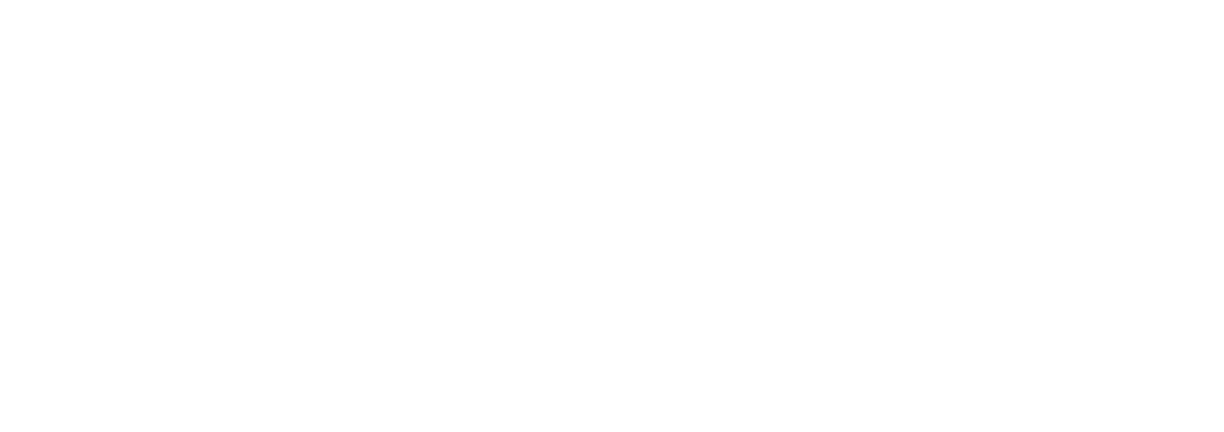