Problem: Requirements for post-consumer content in packaging have put pressure on manufacturers and brand owners to maximize recycled-resin use.
Solution: Using co-injection and a specially built mold, M&M Industries has produced 5-gallon pails with up to 40 percent post-consumer resin.
By Karen Hanna
The 5-gallon pails injection molded by M&M Industries can contain a variety of goods, including cat litter, bird seed and oil, but lately, the focus has been on how to cram them full of post-consumer resin (PCR).
With states such as California adopting increasingly stringent PCR-content requirements, the company and its partners, OEM Engel and mold maker Top Grade Molds, have been working together to find ways to maximize their use of PCR in pails.
“There’s been some different processes that have looked at this, but none that really get up to the PCR volumes that are needed. So, if you look at a state like California, they require 25 percent PCR in products that are being distributed in the retail market, and that’s not easily accomplished unless there’s a good process,” said Darrell Davis, VP and COO at M&M Industries.
“One way to do it is just run all-black pails with PCR resin, but that’s not necessarily what the marketing groups like,” Davis said.
But, with the expertise of Top Grade Molds and Engel, M&M Industries has so far achieved up to 40 percent PCR content within the body of the pail. That allows it to meet and exceed current requirements, even when accounting for the weight of separate components, such as lids, that might contain only virgin resin.
And it’s gunning for more.
So far, the approach taken by M&M Industries and its partners outperforms even other co-injection processes, Davis said.
“The co-injection process typically can get up to, say, 30 percent, and, if you put that in the pail, you don’t get your 25 percent by weight volume between the pail and the cover, so your overall package doesn’t meet the requirements. So, it requires a better mousetrap, a better co-injection process, to maximize the amount of PCR that can be used in the package,” Davis said.
Jim Overbeeke, business development manager for packaging for Engel North America, said M&M Industries uses two standard, single-stage injection units — one for processing PCR for the pail’s core layer and another for the virgin resin at the skin layer.
“Engel’s co-injection barrel head, together with TopGrade’s co-injection hot runner, provide an economical and reliable two-material melt-stream process control, allowing a multilayer part with an encapsulated gate,” he said.
The key, Davis said, is the “tie-in between the machine and the mold.” Other mold makers M&M Industries approached couldn’t meet the company’s goals, he said.
"It’s not just a machine; you can’t just throw any mold in there,” he said. “It’s aIn order to maximize PCR content, M&M Industries and its partners continue to experiment to improve the process. But they already have discovered one serendipitous advantage of pails that incorporate both virgin and recycled materials over pails produced with a more conventional process.
“If we even use the exact same material on the core and the skin, we get a stacking-strength-performance increase [in a] 5 to 10 percent range, which is nice,” Davis said. “And what’s better is that you can actually, if you’re looking for higher stacking strength than what you normally get out of resin, you take a PCR that’s got a different melt or different properties, and push that into the core, and get better stacking properties.”
With Western states leading the charge to increase PCR content, Davis said M&M Industries intends to market its pails out West. While it’s conducting testing at its headquarters facility in Chattanooga, Tenn., where Davis works, the company plans to ship the co-injection machinery setup sometime around December to its Phoenix plant, where it plans to commercialize the pails.
Davis expects the pails will get plenty of attention, once they hit the market.
“We’re getting more questions and requests, but the reality of it is there really should be a lot more questions and requests because … [in] California, you’re required to be doing this now. And many, many accounts, whether it be ours or our competitors, are not meeting the requirements of CalRecycle, which is a California recycling group,” Davis said.
Also known by its formal name, the California Department of Resources Recycling and Recovery, CalRecycle is the enforcement agency for the state’s Rigid Plastic Packaging Container Program.
So far, because regulations target only containers with volumes of 5 gallons or less, M&M Industries has focused its runs on 5-gallon pails, along with 2- and 4-gallon pails. But the process could someday be used for both bigger and smaller containers, as well as PP containers, Davis said.
“We’re just playing with the different sizes at this point in time,” Davis said.
Eventually, he believes the process could yield even bigger rewards.
“I would love to target better than 50 percent of the pail,” he said.
Karen Hanna, senior staff reporter
For more information:
Engel Machinery Inc., York, Pa., 717-764-6818, www.engelglobal.com
Top Grade Molds, Mississauga, Ontario, 905-625-9865, https://topgrademolds.com
Karen Hanna | Senior Staff Reporter
Senior Staff Reporter Karen Hanna covers injection molding, molds and tooling, processors, workforce and other topics, and writes features including In Other Words and Problem Solved for Plastics Machinery & Manufacturing, Plastics Recycling and The Journal of Blow Molding. She has more than 15 years of experience in daily and magazine journalism.
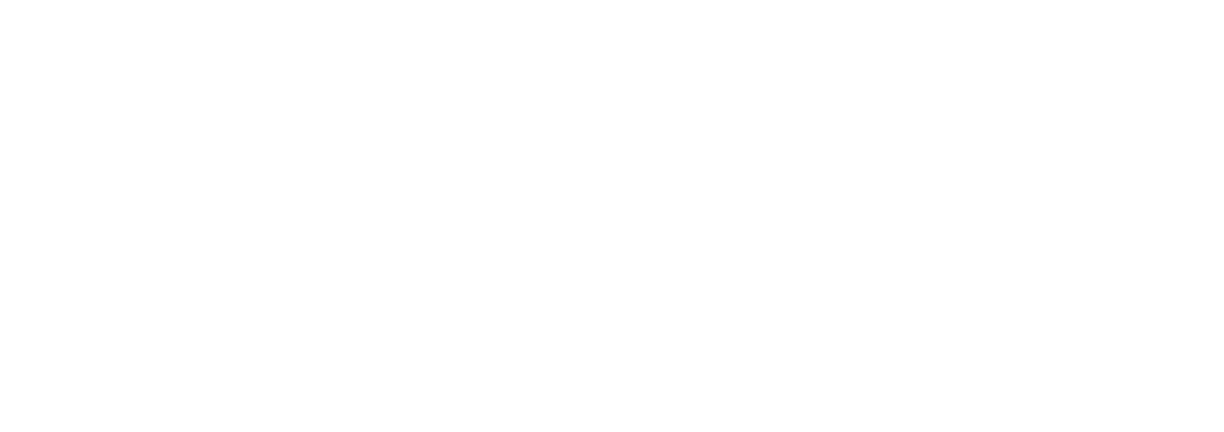