Contact lens storage-system assembler sets sights on perfection
Problem: A supplier of storage trays rejected many of the products because their color was off-spec.
Solution: The supplier took manufacturing in-house, and it uses a new Ampacet LIAD color system to ensure quality control.
By Karen Hanna
It’s a lesson every college student learns simply by doing laundry: A small amount of red goes a long way toward contaminating all your whites.
For an assembler of injection molded trays used by eye doctors, it’s one of the persistent mistakes that argued for drastic changes.
Elevate recently partnered with auxiliary equipment experts Vismec and Ampacet to achieve repeatability, accuracy and control, as it took over manufacturing operations to ensure quality.
Called “sample kits” in the industry and assembled from components made from polyolefins and PS, Elevate’s products resemble old-fashioned card catalogs. Elevate employees pack them with thousands of sample contacts, arrayed according to the various options — including daily disposable lenses, monthly and weekly replacements, and spherical and multifocal lenses. New doctors get a full complement of them when they open an office; lens makers ship out kits when they introduce new products to the market — sometimes more than once a year.
Too often, Elevate’s suppliers were sending trays that weren’t up to snuff.
“Probably 15 percent of all the parts that we purchased went unused due to quality problems or obsolescence,” Sinclair said.
For the job to be done right, Sinclair decided with co-owner Mike Shippel that Elevate would just have to do it itself.
He and Shippel found a vacant 160,000-square-foot manufacturing plant in Austell, Ga., around 20 miles from Elevate’s assembly operations in Atlanta. Then, in September, they turned to Chip Hembree, owner of Plasticpro, a company that provides consulting to molders, to help them fill it with the machines that could meet their quality expectations. The company, which had formerly performed molding before specializing inFor stakeholders in the health-care industry, including lens makers such as Elevate customers Alcon, Johnson & Johnson and Bausch + Lomb, there is no substitute for sterile white.
“These things reflect on their reputation and their brand. My business partner and I take that very seriously,” Sinclair said. “That's the charge that we gave Chip was these things have to be perfect.”
Hembree, who has about 40 years of experience in molding, has started plants from the ground up five times. The newly leased Elevate Manufacturing, which had been a molding company until about a year earlier and still had silos and some conveying lines in place, represents startup No. 6.
The first decision — ordering presses — was easy.
“The injection molding machines were the first piece. And we've had parts molded for 20 years and paid attention to what people were using, and so we knew the machines we were going to use,” Sinclair said. Elevate chose a half-dozen Nissei machines, with the smallest clocking in at 240 tons, the largest at 720 tons and two pairs with clamping forces of 400 and 500 tons each.
James Jamison, CEO of Vismec America, who joined the project to help Hembree outfit the plant, said the facility’s existing conveying lines posed a challenge to the team, which set out to ensure that Elevate not only could produce sample kits to Sinclair and Shippel’s standards — but that it might take on additional jobs.
“We did select some equipment that will grow with [Elevate] in the future, as well,” he said.
Because color quality is critical to Elevate, Hembree and Jamison took pains to identify the best auxiliary equipment.
“They had no bones about you searching out quality equipment and pretty much gave me carte blanche to go out and pull what they needed to do this, so we went with the best,” Hembree said.
“One of the things we touched on earlier was that this is a cabinet composed of several different molded parts, so when molding on four different injection molding lines, you've got four different processes going on. Everything has to match when you put it together, or you’ve got a hodgepodge of white colors,” Hembree said.
Once the team understood Elevate’s requirements, Hembree said they could narrow down their choices.
“It had to be gravimetric, it had to be very repeatable. And it had to be something that we could look at data continuously and track and know that we were on target,” he said. “It’s all about quality here.”
With accuracy to within 0.1 gram, Ampacet’s LIAD Smart ColorSave 1000 gravimetric feeder was one important choice.
The technology tracks the amount of resin from the time it enters the system until it leaves the press as a part. According to Doug Brownfield, commercial director for Ampacet, it removes the possibility of human error.
The system’s Smart-Clean purging feature completely pushes out the colors used in one cycle before an operator starts the next.
“Right now, they're just using one color, the white,” said Vince Paskie, business development manager for Ampacet. “In the future, when they switch to other colors, the Smart-Clean system will be able to automatically purge all the material from the hopper in the screw, with just the push of a button on the control. Not only will it be accurate and repeatable, but it will also be a big timesaver and a lot safer than [having] people climbing up on the machines to clean out the units.”
Besides preventing waste, the system provides real-time calculations about recyclate use, automatically compensating for variances in color. This helps the company reduce its environmental impact by allowing it to reclaim runners.
“Keep in mind with resin prices being high, which [means] white masterbatch prices are higher now than before, being able to control your usage rates precisely is critical to controlling your cost,” Brownfield said.
Elevate now has color quality under control.
“When you hear somebody say, ‘I received pink parts, and they should have been white,’ [that] means the contract molder they were using most likely wasn't purging their line well,” Brownfield explained. “They weren’t perhaps purging their feeder lines; they weren’t purging their injection molding lines efficiently. So now, with their equipment today, we can be assured that they can purge quickly and efficiently.”
Jamison’s Vismec supplied a materials-handling and bulk storage system consisting o“I love how clean Vismec is, compared to some of the other places I've been in. They're incredibly quiet, incredibly efficient, and just the biggest thing for me was how quiet this equipment is. We have a line out on our shop floor, we haven't had to put a wall around it. ... You can actually stand out on the floor and carry on a conversation without earplugs in and not have to scream at each other,” Hembree said.
Each of the six lines includes a Gammaflux hot-runner controller, Star Automation robot, Harvard Factory Automation conveyor and AEC TCU.
In commissioning all the new equipment, part color remained paramount, Hembree said.
“When we were doing our color trials, coming into this, that probably chewed up more time than anything,” Hembree said.
In all, the process to transform from an assembler, known as Elevate Solutions Group, to a manufacturer, known as Elevate Manufacturing, took just 90 days from the time the first equipment arrived till it started up.
Hembree — who's still working part-time as a consultant — officially joined the company as VP of manufacturing in February, and molding started just a few weeks later, on March 18.
He and Sinclair credited their suppliers and Elevate employees for making the process seamless.
“For me to be able to get on the phone and talk through a phone call looking at numbers and come up with particular models and specifications on equipment, that's all up to those guys. They know what they're selling, they know what they’re doing. … That's invaluable,” Hembree said.
About 85 people work for Elevate, most in assembly operations.
Sinclair needed little time to explain how his company has managed to fill the positions at a time when Help Wanted signs have become ubiquitous:
“Care about every single one of them. Let them know they're valuable. Let them know what's expected of them every day. It's family. This is family,” he said.
The company relies on its workers for quality control — at least four stages in the process require visual checks of parts or labels that change regularly with each project.
Experience with the assembly process has prepped the workers for additional responsibilities.
“We took some long-term assembly workers and moved them to become operators in the manufacturing area. I think it's one of the reasons it's gone so well is they're inspecting the parts coming off the machines, and they can see something immediately that's not right because they've been assembling that stuff for a year and a half, so they can spot something that's wrong,” Sinclair said.
He lauded workers’ efforts.
“They're incredibly attuned to any defects. They're really good. Not just a happy workforce, a productive workforce,” he said.
Hembree agreed.
“There were already just an outstanding group of people here. That's what drew me — the people. I can mold plastic anywhere,” he said.
With the new plant, Elevate has taken control of the supply chain. According to Sinclair, to compensate for outside molders’ other priorities, the company once relied on parts with monthslong lead times. Because of this, parts often were obsolete by the time Elevate received them. Now, Elevate can enjoy the benefit of a just-in-time manufacturing approach.
“We're constantly evolving our product, our kits, and evolving the design, evolving the ways that the trays snap together and the way the labels go on and things like that. And, so, in some cases, we would have ordered parts four or five, six months ago. And then we evolved the design. We had some inventory here; that was our own obsolescence,” Sinclair said.
Having returned to manufacturing, Elevate already is exploring other possibilities, beyond the sample kits.
“We can do more injection molding, but we don't want to just do every kind of injection molding for anybody. We're going to have the same kind of focused approach. And be selective. We're not desperate, so, we're going to pick a few select things and do it right,” Sinclair said.
While Elevate’s customers might not realize the company now does its own manufacturing, he said he believes the results will speak for themselves.
“They're going to realize they’re getting a better product. It’s perfectly white, and our lead time is going to improve. They’re going to see benefits like that. They’re going to see the benefits of having the most reliable equipment here,” Sinclair said.
Karen Hanna, senior staff reporter
Contact:
Ampacet Corp., Tarrytown, N.Y., 914-631-6600, www.ampacet.com
Plasticpro Services LLC, [email protected], www.plasticproservices.com
Vismec America Inc., Spartanburg, S.C., 833-847-6321, www.vismec.com
Karen Hanna | Senior Staff Reporter
Senior Staff Reporter Karen Hanna covers injection molding, molds and tooling, processors, workforce and other topics, and writes features including In Other Words and Problem Solved for Plastics Machinery & Manufacturing, Plastics Recycling and The Journal of Blow Molding. She has more than 15 years of experience in daily and magazine journalism.
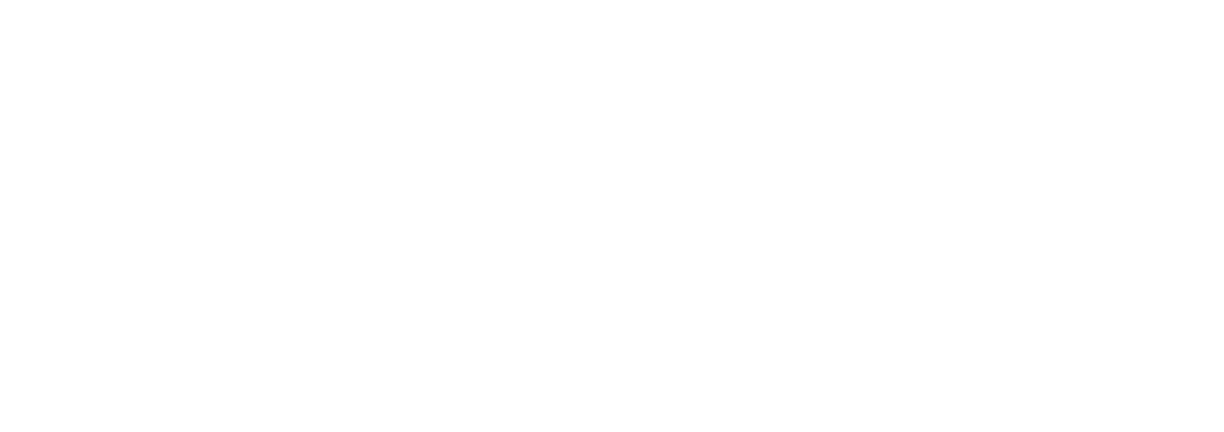