Skye Automation system helps automotive supplier inspect several types of part
By Skye Gorter and John DeWaal
When a Tier 2 automotive supplier’s inspection system experienced too many errors due to feeding problems and jamming, the company tasked system integrator Skye Automation to develop a flexible new solution.
The supplier’s system used vibratory bowl feeders that sorted and oriented parts for a robot to pick; introducing a new part into the system required adding another bowl feeder. Doing so created issues with floor space and the number of bowl feeders required for the job. Furthermore, parts were often misfed or became jammed in the bowl feeders, so Skye Automation started from scratch on a new system.
Mixed Model Inspection
An operator sets up a recipe in the human-machine interface (HMI) for the correct part inspection and selects the number of boxes to fill and the total number of parts to run, and then loads a shift’s worth of boxes onto the load station. The operator hits “start” when the software loads the job, and the machine begins to run.
A magnetic feeder loads the plastic parts into two hoppers in the robotic work cell, and the parts enter vibratory feeders, and then two programmable FlexiBowl feeders (Figure 1). These flexible part feeders from ARS Automation separate the individual parts, allowing a robot to make picks using grippers and automatic tool changers from Schunk.
Five VCXG-51M 5-megapixel GigE cameras from Baumer comprise the vision portion of the system, with two of them used in the inspection station (Figure 2). One camera looks down from the top and another from the side to provide two views of the same part for inspection. Two cameras look down on the FlexiBowls to provide pick location information for the robot, while the last camera provides barcode verification at the end of the process. Lighting in the system consists of coaxial diffused lighting, off-axis ring lighting, backlighting and a barcode reader light, all from Metaphase Technologies.
When a part enters the field of view of the cameras looking at the FlexiBowls, the system captures images, and the robot picks the part and places it onto the inspection table. The table then shuttles in front of the inspection system, and the two cameras capture part images and transmit the data via GigE cable to a Neousys Technology Nuvo-7006DE fanless industrial computer (Figure 3) running Q.Vitec machine vision software.
An air jet blows the part into a sorting chute, where a pneumatic cylinder moves a flap and directs the part in one direction or the other based on a pass or fail determination from the software. Parts either pass into a box sitting on the conveyor or go directly into a reject bin for disposal. When the box fills with a predetermined number of parts, it indexes up an elevator and rolls down a gravity-fed conveyor. The system then indexes the next empty box in front of the load station.
An inkjet barcode printer synchronized to the conveyor motion directly prints codes onto the filled boxes and the last camera reads the code data, ensuring that boxes have been filled with the correct parts and that the barcodes match the current recipe loaded into the software.
In order to inspect multiple part types, the operator chooses the correct recipe before inspection instead of having to change processes or add new hardware. Initially designed to inspect 12 plastic parts, the system now handles 15 different models.
A programmable logic controller (PLC) operates a variable frequency drive (VFD) from Lenze. It helps elevator, pusher and linear motor actuators from IAI America provide motion for the system. Even though the system uses a PLC, a PC sits at the heart of the process.
The proprietary software provides a full visualization of the entire system — including all five cameras in a single visualization — allowing operators and technicians to pinpoint areas of concern directly from the HMI. The PC enables this, along with the ability to be Industry 4.0-ready and to integrate into a customer’s OPC-UA framework.
Industrial PC Helps with COVID-19 Concerns
Since the system was developed during the COVID-19 pandemic, remote access became a major consideration, which led to Skye Automation designing around a PC.
The global pandemic prevented all travel, so Skye Automation commissioned and shipped the machine without anybody ever stepping foot in the plant. The industrial PC delivers a full view into the system’s performance, which would not be possible with a PLC-based system.
Additionally, the PC’s 8-core Intel i7 processors allowed Skye Automation to separate out different processes and run them autonomously without them interfering with one another. PLCs also cannot match PCs in terms of central processing unit (CPU) power and the corresponding price and performance tradeoffs. With the PC, the vision task runs on multiple processers, allowing visualization on one and Windows on another.
From an efficiency standpoint, a PLC that accomplishes the same or similar tasks would be much more expensive, but also more rigid in its programming environment. A customized visualization program would also be required, in addition to the PLC program.
Designing for the Future
Should a particular application ever require something beyond rules-based machine vision, such as deep learning capabilities, PCs provide a foundation for a control system. Skye Automation now designs all of its machine vision systems with the idea that deep learning or machine learning tools can be added on in the future.
In the past, when a machine vision system began running after installation, it never got any better. But a machine vision system from Skye Automation gets better over time because integrators or OEMs can use graphics processing units, tensor processing units and visual processing units to convert an industrial PC from CoastIPC — Skye Automation’s industrial PC supplier — into an edge artificial intelligence device.
Machine vision and automation solutions must adapt to the ever-increasing needs of today’s manufacturing environments. Designing a system up front that can flexibly expand its capabilities as needed offers one efficient method for doing so.
For more information:
Skye Automation, Stirling, Ontario, www.skyeautomation.ca
ARS Automation, Arezzo, Italy https://en.arsautomation.com
Baumer, Frauenfeld, Switzerland, www.baumer.com
CoastIPC, Hingham, Mass., www.coastipc.com
IAI America, Torrance, Calif., www.intelligentactuator.com
Lenze, Aerzen, Germany, www.lenze.com
Metaphase Technologies, Bristol, Pa., www.metaphase-tech.com
Neousys Technology, New Taipei City, Taiwan, www.neousys-tech.com
Q.Vitec, Wunstorf, Germany, www.qvitec.de/en
Schunk, Lauffen am Neckar, Germany, www.schunk.com
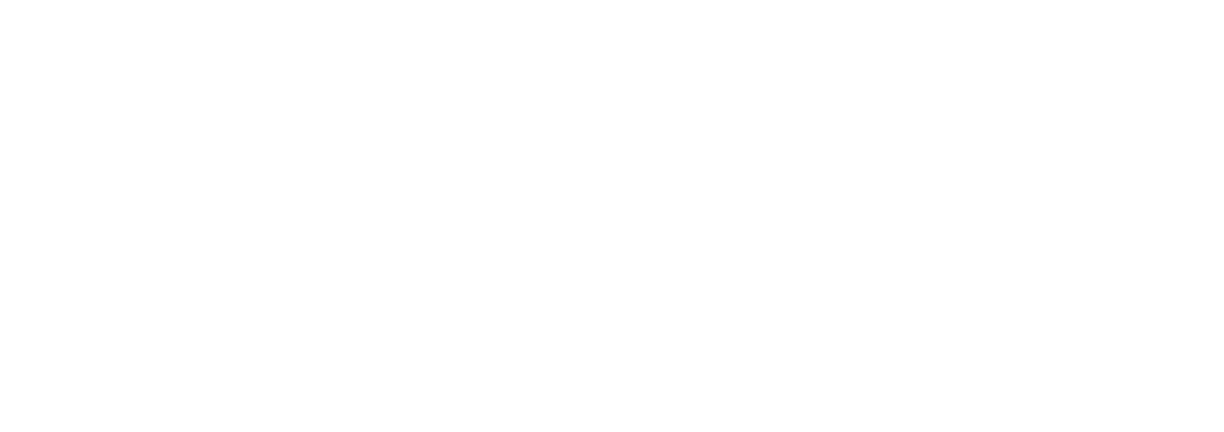