Evosys laser welder provides seamless solution for emissions-tank maker Dynacert
Problem: Dynacert's special add-on for trucks needed an impermeable seal to facilitate an electrolysis process that enhances the efficiency of diesel engines.
Solution: Dynacert uses the Evosys Evo 1800 laser welder to produce a perfect bond to seal its Hydragen HG1's constituent ABS parts.
By Karen Hanna
A welder that creates bonds between plastics is sealing the deal for a technology designed to cut truck emissions.
Dynacert Inc., a Toronto company established with the goal of making technologies for cleaner-burning engines, offers a suite of devices that reduce fuel requirements. Its Hydragen HG1 units, available in a variety of sizes, use potassium hydroxide to turn distilled water into pure oxygen and hydrogen gases, employing them to increase efficiency of the combustion of the diesel fuel.
Dynacert says its carry-on suitcase-sized HG1 units are portable and simple to install on a vehicle, where they perform “simple electrolysis.” But making the vessels isn’t so easy. To achieve exacting tolerances, each half of an HG1 unit must be injection molded, then the two parts must be sealed together.
The process has to be seamless — a requirement that has brought Dynacert together with laser-welder maker Evosys. Evosys’ Evo 1800 welder’s compact size, flexible tooling, advanced user-friendly programming tools and safety-focused design make it an ideal fit for the application, said Denis Wittmaier, CEO of Evosys North America.
The HG1 units use an electrolyte — an acid that could compromise an imperfect seal — to break water down into its constituent parts, said Robert Maier, COO and chief engineer for Dynacert. Keeping the gases and electrolyte separated in the HG1 units requires a perfect, impermeable weld.
“These two-part tanks are used to carry the electrolysis fluid and water. It also holds the gases, which cannot be allowed to leak,” Maier explained.
Designed for use with trucks with commercial diesel engines, the HG1 units improve fuel economy by 10 to 15 percent and cut emissions in half, based on average results obtained by third-party testing. Without modifying the engine’s computer or control system in any way, they reduce fuel consumption by 6 percent to 19.2 percent.
“Our technology reduces that NOx by up to 88 percent right at the combustion, right at the burn within a diesel engine,” Dynacert President and CEO Jim Payne said.
The unique requirements of the HG1 units, which are made from ABS, put pressure on Dynacert to identify a suitable bonding strategy.
The tanks’ functional requirements presented limitations on the types of approaches that might work, Wittmaier said.
“The design of the tank and its lid is very precise, as the assembly requires maximum tank size in the allotted volume,” Wittmaier said. “The tank-to-lid joint had to be minimized, not allowing for a glued joint.”
In addition, glue simply isn’t reliable enough, Maier said.
Compared with alternative processes, welding is more cost-effective and requires no expensive auxiliary materials. The process achieves a high degree of accuracy and strength, produces virtually no waste and requires no post-welding trimming or scraping.
Laser welding heats and joins plastic in one step simultaneously.
For Dynacert, an Evosys laser welder was the perfect choice.
“Laser welding provides a low-heat and 100-percent bonded solution for the two-part tanks to become one,” Maier said.
Dynacert uses the Evo 1800 welder to perform quasi-simultaneous welding to join the two components of the HG1 units.
Due to the requirements of the tanks, the process is slightly modified from conventional welding. Normally, a material that is transparent to the wavelength of the laser emitted by the welder is combined with an absorbent material. The laser beam is focused through the laser-transparent molded part onto the absorbent joining partner, which melts on the surface; as that happens, the transparent/transmissive component is also plasticized, creating a bond between the two surfaces. For the HG1 units, the color arrangements have been swapped, and the assembly is welded upside down to have the carbon-black lid absorb the laser, Wittmaier said.
As part of Dynacert’s process, the Evo 1800 uses galvanometric mirrors, together with a special optical setup, to guide a laser beam along the contour of the seam at very high speeds of up to about 3.3 feet per second. In this way, it retraces the weld along the seam several times, compensating for possible inconsistencies caused during the molding process.
Dynacert uses component-specific fixtures and a high-strength device to ensure exact positioning of the parts before the welding process; a pneumatic cylinder presses the entire assembly from below against the clamping device and applies the necessary forces.
According to Evosys, the Evo 1800 is particularly suitable due to its intuitive operating concept, and the process monitoring and ease of changeovers provided by Evosys’ process software. Using the welder’s HMI, operators can perform the process almost immediately without extensive training — a benefit that has been especially important because of the pandemic, which prevented Erlangen, Germany-based Evosys from providing on-site commissioning. With the HMI, operators can quickly program the welding contour, feed speeds and laser power.
The HMI also handles the visualization and evaluation of process data; the storage of data records; and other system functions.
“The built-in quality check for weld collapse in the Evosys machine helps us ensure that the weld is sound and continuous,” Maier said.
With a clean weld thanks to the Evosys lasers, the HG1 units can help users operate their trucks with less pollution.
“We have a technology right now that can make such a significant difference in the world and at the same time pay for itself. I mean, I think that’s a very, very attractive solution,” Payne said.
Karen Hanna, senior staff reporter
Contact:
Evosys North America Corp., Auburn Hills, Mich., 248-973-1703, www.evosys-laser.us
Karen Hanna | Senior Staff Reporter
Senior Staff Reporter Karen Hanna covers injection molding, molds and tooling, processors, workforce and other topics, and writes features including In Other Words and Problem Solved for Plastics Machinery & Manufacturing, Plastics Recycling and The Journal of Blow Molding. She has more than 15 years of experience in daily and magazine journalism.
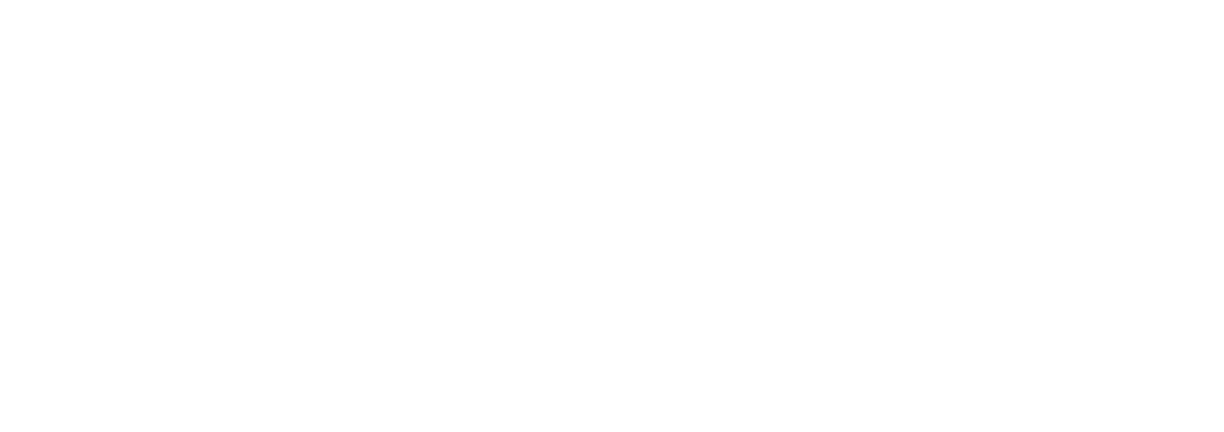