For one injection molder, an investment in robots yielded a pleasant surprise — fewer worker injuries.
“We’ve had a drastic reduction in worker complaints, I can tell you that,” said Gary Forsberg, plastics production manager for Lomanco, one of North America’s largest manufacturers of residential vents, including roof vents.
The company, which also has metal fabrication equipment, began installing robots in its molding cells in 2006. That’s when it started noticing a reduction in workers’ reports of back injuries and other pains related to poor ergonomics.
Forsberg said that while the company doesn’t have specific numbers, it’s obvious why automation reduces such injuries. Workers no longer must bend over thousands of times per shift to pick parts off a conveyor belt that runs about 20 inches off the ground.
“We started off with standardized machines with gravity drop onto conveyors,” Forsberg said. “This is the way everybody used to do it.”
Now, on each of the automated lines, a robot removes molded parts from the press, puts the parts in an automated stacking system and then delivers the stacked parts to a worker at an ergonomically correct height of 38 to 42 inches for a visual inspection prior to packaging.
“Ergonomically, the operator is not bending over to pull a part off a conveyor,” Forsberg said.
Some of Lomanco’s production lines produce 8,000 parts in 24 hours. Without automation, a worker would need to bend over up to 4,000 times per 12-hour shift to remove parts.
“That’s an extreme amount of bending for a person — it’s very tough,” Forsberg said.
As of January, Lomanco was running 12 injection molding machines (IMMs) and all but two were automated. The company planned to add three more presses, and Forsberg said any IMMs the company buys now come with robots installed. The company primarily uses Sepro beam-mounted three- and five-axis robots.
Lomanco uses robots for some assembly work, which also can improve safety. Certain parts need to be cooled before they can be handled. In those cases, robots place the hot parts into a cooling fixture, where the parts will cool for a prescribed amount of time before being removed for assembly.
In addition, the company has automated some assembly processes to reduce repetitive hand movements. It has installed two lines running automated glue systems.
“It’s a lot less hand movements that way,” Forsberg said.
When the company installed the robots, it also took steps to ensure workers were kept safe from their movements, he said. The robots operate within a caged area with door interlocks to ensure workers cannot enter while the robots are moving. Workers press a button to unlock a door, and the door will not open until the robot shuts down.
Bruce Geiselman, senior staff reporter
Contact:
Lomanco Inc., Jacksonville, Ark., 501-982-6511, www.lomanco.com
Bruce Geiselman
Senior Staff Reporter Bruce Geiselman covers extrusion, blow molding, additive manufacturing, automation and end markets including automotive and packaging. He also writes features, including In Other Words and Problem Solved, for Plastics Machinery & Manufacturing, Plastics Recycling and The Journal of Blow Molding. He has extensive experience in daily and magazine journalism.
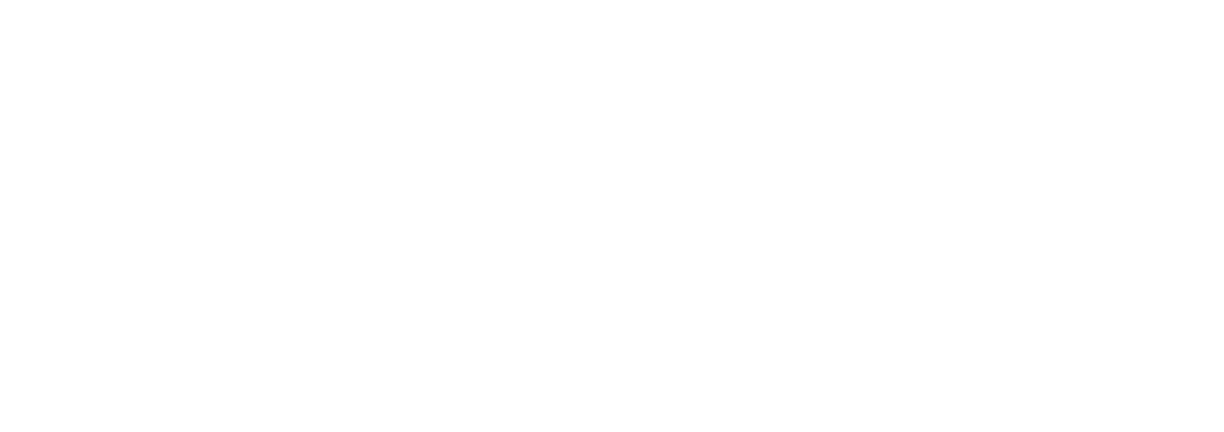