By Karen Hanna
KraussMaffei Group continues to expand its GX injection molding machine series, with its latest addition, the GX 1300, the largest model in the line. In all, since 2019, the Munich company has added six presses and 27 new possible machine configurations.
The portfolio encompasses presses with clamping forces as low as about 450 tons and topping out at the GX 1300’s capacity of 1,460 tons.
Unlike the earlier, smaller models in the line, which can use injection units no larger than size SP12000, the new models can be equipped with bigger units, up to SP17200, in some cases.
The series is designed for the needs of the packaging and automotive industries, as well as the production of technical components. The GX 1300, for example, is designed with double-cavity molding in mind. It can handle large throughputs and short cycle times and is useful for making products such as buckets or sturdy, reusable, thick-walled crates.
Other 2020 additions include the GX 1200 and the wider-platen GX 1101, which have clamping forces of about 1,300 tons and 1,200 tons, respectively.
The GX-series presses feature KraussMaffei’s patented locking system, GearX. Besides fast interlocking, this arrangement provides space savings and accessibility to the ejector area. Meanwhile, the company’s smart pressure pads ensure accuracy of the moving mold platen.
“We are talking about the most space-saving design on the clamping unit side compared to toggle-machines,” said Bastian Eberle, an IMM product and technology manager for KraussMaffei Technologies GmbH, Munich. “With a locking system and, in addition, pressure pads, which ensure the required clamping force, you have a shorter machine.”
The GX 1101, GX 1200 and GX 1300 all have approximate vertical clearances of 5.2 feet and horizontal clearances of 4.2 feet.
The machines employ KraussMaffei’s HPS screw technology, which allows for much greater outputs than other machines. The technology forces the melt forward through two channels and guarantees that it is mixed evenly to produce parts with streak-free surfaces. This contributes to short cycle times.
In addition, the presses can be equipped with KraussMaffei’s BluePower servo-drive technology, or customers can opt for an asynchronous drive, if that better suits their needs.
“Our BluePower drive technology is based on a modular synchronous drive setup. Therefore, we achieve reduced energy consumption compared to asynchronous drives, which are our standard,” Eberle said. The BluePower technology lowers the energy requirements of a machine in idle mode, he said. “Especially for applications running thick-walled products, the energy consumption can often be reduced by more than 60 percent.”
Also, as an option, users can specify a machine with APC plus. This feature, which stands for Adaptive Process Control, compensates for external influences, such as fluctuations in material quality, ambient temperature or humidity, by regulating the changeover point from injection pressure to holding pressure in real time.
APC plus ensures consistency in the weight of individual parts, even those made from recycled material, and better guarantees part quality and minimizes waste.
“Our patented APC technology analyzes and continuously regulates the injection molding process by itself,” Eberle said.
Also available as add-ons are KraussMaffei’s in-mold-labeling feature and Speed option. The Speed option takes advantage of KraussMaffei’s GuideX, a precise, force-absorbing system that increases the life of molds. The Speed option provides extremely fast clamping movements and reduces the cycle time for large opening strokes.
Karen Hanna, associate editorContact:
Krauss-Maffei Corp., Florence, Ky., 859-283-0200, www.kraussmaffeigroup.us
Karen Hanna | Senior Staff Reporter
Senior Staff Reporter Karen Hanna covers injection molding, molds and tooling, processors, workforce and other topics, and writes features including In Other Words and Problem Solved for Plastics Machinery & Manufacturing, Plastics Recycling and The Journal of Blow Molding. She has more than 15 years of experience in daily and magazine journalism.
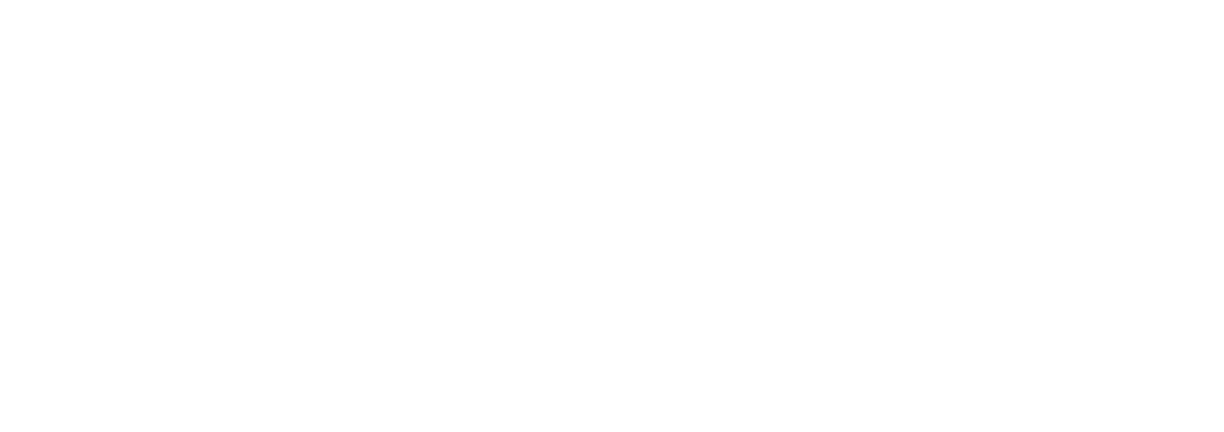