Nissei rolls out compact hybrid vertical injection molding machines
By Karen Hanna
A new clamping mechanism that takes up less space than conventional units makes its debut on the largest models of Nissei’s TWX-R hybrid vertical injection molding machines.
Overall, machine height is about 10 percent lower than conventional machines. With the new clamping mechanism, the two largest presses have the same mold mounting height as the other models in the TWX-R range, which includes units as small as 50 tons. Koido said this “allows the design and installation of automation apparatuses (for both pre- and post-injection molding processes) to be the same level across the board.”
Maintenance, mold installation and setup, work around the machine, and product insert and removal are easier, thanks to the design.
The new machines conserve space by using separate cylinders, one dedicated to high-pressure clamping and the other to high-speed mold opening and closing. Conventional machines use one cylinder for both actions, which means that the cylinder stroke must match the maximum mold-opening stroke. Nissei’s setup allows users to enjoy the advantages of a direct-pressure mechanism, including uniform pressure distribution, precision and stable clamping force that’s resistant to external factors, such as temperature fluctuations.
Because the machines use the direct-pressure type clamping mechanism, setting optimal clamping force is very easy, Koido said.
As an additional bonus, the mechanism requires about half as much hydraulic oil as conventional clamping mechanisms.
Other features include a low-pressure mold-protection technology that detects foreign objects and prevents them from causing insert misalignment during mold movements, and a three-tie-bar-wide turntable. A servomotor drives turntable rotation and ejector motion. The servomotor enables fast cycles, smooth motions and precise stopping. It can prevent the misalignment of the inserts.
According to Nissei, adding automation to the machines is especially easy because of their compact size. Depending on their needs, users can outfit the machines with a take-out robot, articulated robot or two-arm robot. The machines’ design also makes them compatible with three-stage automation, allowing a robot to handle the insert, molding and take-out stages.
The machines boast wide daylight opening, accommodating larger and more complex molds, including multi-cavity molds, and feature Nissei’s Tact IV controller, with a 15-inch color LCD touch-panel screen.
Karen Hanna, associate editor
Contact:
Nissei America Inc., Anaheim, Calif., 714-693-3000, www.nisseiamerica.com
Karen Hanna | Senior Staff Reporter
Senior Staff Reporter Karen Hanna covers injection molding, molds and tooling, processors, workforce and other topics, and writes features including In Other Words and Problem Solved for Plastics Machinery & Manufacturing, Plastics Recycling and The Journal of Blow Molding. She has more than 15 years of experience in daily and magazine journalism.
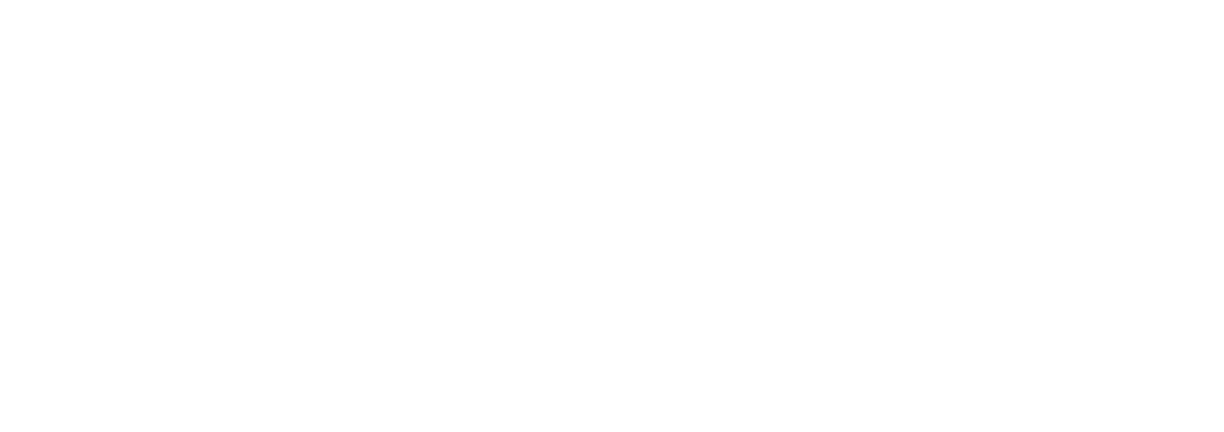