By Karen Hanna
At the end of a difficult year, maybe it helps to glance at the future: Turn off the factory lights, turn on the machines, check the locks, walk away. Get in your car (or hovercraft, if you’re living the sort of life that makes others envious) and go home.
Human-free manufacturing has arrived. At least that’s Niigon’s vision of the next 10 years. Representatives of other injection molding OEMs provided more ideas in interviews with Plastics Machinery Magazine focused on their outlook for the next decade. If the past year is any indication, the future could be a wild ride.
Advances could include more automation, greater reliance on the Industrial Internet of Things (IIoT), a focus on sustainability and the development of new materials. Buoyed by the surprisingly strong demand for machinery, OEM representatives also look forward to a resurgence of manufacturing in the U.S.
Flying on autopilot
At its Canadian manufacturing facility, OEM Niigon makes not just processing equipment but some PET preforms for certain customers under contract.Tony Colangelo, Niigon’s global director of business development, said the company’s operations could be a template for the future.
“The plastics industry’s workforce is aging, and it can be difficult to attract the younger generation to fill the gap,” he said. “If this continues, we at Niigon expect that unmanned production cells will become increasingly popular.”
In the future, plants could have human-less work cells, modeled after how Niigon itself operates. “These cells would be similar to our LightsOut cell and would feature complete control and monitoring of the process,” Colangelo said.
One of Niigon’s LightsOut setups includes an NPET150 injection molding machine [IMM] outfitted with a 24-cavity mold. Named for its clamping-force capability in tons, the standard machine has been operating 24 hours a day for 3.5 years without a night-shift attendant, said Robert Sicilia, VP for PET technologies. It has produced more than 8 million preforms without a single rejected part.
In another cell, an NPET300 press equipped with a 72-cavity mold also runs unattended.Featuring automatic lubrication systems, both presses are hybrid machines with a combination of electric and hydraulic functions and on-demand servo pumps. Critical components are easy to access, simplifying maintenance, Sicilia said.
The LightsOut setups are furnished with auxiliary equipment, including dryers, chillers and dehumidification units, and other technologies, such as preform inspection machines, automated guided vehicles and conveyors, Sicilia said.
According to Niigon, the LightsOut setup reduces the total cost of ownership, as well as maintenance requirements and energy consumption.
Niigon’s development projects include auto startup and shutdown, cycle completion, emergency shutdown and one-hour mold change.
The company offers consulting and industrial design services for factory automation and engineering processes.
“In 10 years, we expect integration of automation to be the focus. This is already happening to an extent,” Colangelo said. “However, by 2030, we expect that many auxiliary processes will be effectively integrated into the injection molding cell, incorporating in-mold operations, robotics, assembly, inspection and more, which will be controlled by a common control system.”
Unmanned operation would lead to greater reliability, Niigon said.
At the other extreme is Alfred Rak, president and CEO of Bole Machinery, who commented that much of the industry still is getting by with far less sophistication.
“I find companies that have no Wi-Fi,” he said.
He views widespread lights-out production as a vision of a sci-fi future that’s a little further off. And he’s not alone.
“Right now, there’s only a very few companies that have capability to do lights-out production,” Boy Machines President Marko Koorneef said.
While molders of sophisticated products like medical parts already are tracking every data point and managing operations by cell phone or PC, others get by using jury-rigged, in-house solutions, such as cardboard boxes turned into funnels and chutes to handle the cheap parts they produce, Rak said.
Rather than running without workers, a majority of these molders will continue to look for ways to augment human labor, as cost concerns and a workforce shortage force them to adopt new technologies.
“Another big trend I see is up- and downstream automation,” Rak said.
Brian Bishop, VP of new machine sales for Krauss-Maffei, said that in many shops, parts-handling equipment upstream still is directing parts downstream to operators standing along a conveyor belt.
Krauss-Maffei can work with customers to tailor the downstream equipment they need.
“We can design automation systems around the parts that they’re making,” he said.
Koorneef said the technology isn’t the only thing holding back lights-out manufacturing. It’s a people problem, too.
“If something goes wrong in the middle of the night, you’re always going to need somebody there, so you need somebody 24/7 available on call, and I think that might be something that is for some people still the hiccup,” he said.
Help wanted: Jobs available to humans, robots
Finding workers will remain a challenge, said Kevin Bruce, VP of sales for the plastic injection molding division of Maruka, which distributes FCS and Toyo IMMs in the U.S., Canada and Mexico.
“Finding quality labor is a concern in the plastics industry. Customers seem to have lost some of the expertise in their plants, and we all need to work together to bring in new younger workers and train them in the science of molding,” he said.
Monotonous, low-skilled jobs are the toughest to fill and the most likely candidates to be replaced with automation, said Glenn Frohring, one of the owners of Absolute Haitian.
“It used to be a lot of our customers, they dropped parts in a box, they didn’t use automation, they just used people. Now they’re like, ‘We can’t find people,’ ” he said.
Milacron’s Eric Hallstrom, business manager for low-pressure injection molding technologies, said aspects of molding that hold particular potential for future automation include the handling of large parts for a range of tasks, including placement, assembly and inspection.
To attract workers, Rak said molders will have to offer more perks, such as stock options.
Automation could be key to the ’20s.
Bruce said molders will look to expand beyond just parts removal, to find automation systems to handle downstream work as well. “Customers want to see plastic pellets put in the machine and a finished packaged part out of the cell with minimal employee participation,” he said.
Industry 4.0 grows up
From one extreme of the technological spectrum to the other, molders are becoming accustomed to burgeoning quantities of data.
“I think what we’re going to see in the future over the next 10 years is obviously more automation,” Koorneef said. “I hope it means that Industry 4.0, which is the data collection, etc., is going to be more and more ... a valid point for our customers.”
Krauss-Maffei's Bishop related his personal experiences as a molder in explaining how data has improved life for molders — and will continue to do so.
“I had the opportunity for 5 years to run an injection molding facility before I took this job, and I can absolutely tell you that there were many times when I came in the next morning [to work] on a critical part that I was running only to find out that someone turned off the water from the temperature control unit, or the dryer wasn’t set right,” he said.
Now, the entire process can be integrated, though Bishop acknowledged that compatibility between machines, based on their age or model, is one issue still holding molders back.
“As they replace older equipment and buy integration, it’s the responsibility of the auxiliary companies and the machinery companies to jump on a common platform,” he said.
While most aren’t leveraging everything that’s available to them in our Information Age, the influence of Industry 4.0 technologies will only continue to grow, alongside automation, Bishop and others said.
Data and artificial intelligence can help shops track molds, manage inventory and identify maintenance issues before they result in downtime, Bishop said.
“As we continue to analyze the data, it’s going to allow us to predict failures in older equipment before they happen so that we can have the parts there for our customers, so they have minimal downtime,” Bishop said.
Data-technology acceptance varies by plant and industry, said Wittmann Group Managing Director Michael Wittmann. IIoT protocols and technologies allow users to connect their machines to condition monitoring systems, or MES or ERP solutions, but whether they do so is up to them.
“Every new-generation machine incorporates more IIoT technology than previous models,” he said. Machines are getting smarter, which means that there are more capabilities to exploit — or ignore. Even now, he said, factories might operate their machines outside their network, but the sensors on the machines ensure their users still are enjoying some of the benefits of Industry 4.0 connectivity.
The availability of Industry 4.0 tools is expanding, but this comes with costs as well as benefits, Koorneef said. Finding people willing to work in a factory — and in possession of the high-tech skills the future demands — will get harder. Fortunately, some of the technologies are becoming more accessible.
“The integration into a regular PC or a factory network, I do believe that will continue to grow because the technology is available and it becomes more of a plug-and-play type of thing, not a special development that costs tons of money,” he said.
Wittmann touted his company’s advances in this area. Hardware improvements have come online at the same time as the standardization of software protocols and interfaces such OPC-UA and Euromap specifications.
“Our company is leading this development with our Wittmann 4.0 ‘plug-and-produce’ technologies,” he said. “Thereby, we allow our Wittmann Battenfeld molding machine with [Unilog] B8 control to become sort of a control center for the entire work cell,” including auxiliary equipment such as dryers, blenders and temperature controllers. The interconnectivity allows one MES solution — Wittmann Battenfeld’s TEMI+ — to oversee an entire complement of equipment supplied by the company.
That’s especially the case for medical molders or auto-parts suppliers that need the traceability that only Industry 4.0 can provide, but over time, change is going to come for all molders, OEM representatives predicted.
Among manufacturers that benefit from the technologies are molders that ship directly from their plants to customers linked along the supply chain by Amazon, a novel arrangement under evolutionary pressures created by the pandemic.
“The machine, the product that comes out of the injection machine, it’s all tied together, and it goes out the door in a box, and the drone drops it in your yard,” Absolute Haitian’s Frohring said.
Not all customers demand that level of traceability, but for those that do, greater connectivity has been a boon. “If you’re in a competitive environment, in automotive, that’s the sexy stuff that sells to your customers,” he said.
3-D printing still occupies second string
One technology unlikely to reach full maturity in the next 10 years is 3-D printing, OEM representatives said.
Because of costs and slow speeds, Koorneef said the thought of 3-D printing overtaking injection molding doesn’t keep him up at night.
“That’s for my kids to worry about,” he said.
The technologies offer the possibility for fast prototyping and customization, but still lag well behind injection molding.
“The production of custom-made products splits production into smaller batches, which makes the production process and therefore the final product more expensive,” said Wittmann, who predicted users might turn to 3-D printers to make replacement parts. “With growing purchasing power, consumers might be willing to spend more on custom-made products. However, I doubt that this will reach a significant volume for products at the beginning or middle of their life cycle."
But, should a 3-D printer ever come along that can push out parts as quickly as a press, “that would revolutionize the whole industry,” Koorneef said.
A greener tomorrow
“As a manufacturer, it’s our responsibility to try to improve the environmental conditions for plastics,” Bishop said. As part of KraussMaffei Group, Munich, Krauss-Maffei provides both IMMs and extruders. It’s a good niche, at a time when environmental solutions are in demand.
“We have the ability to design systems that can reprocess materials and put it back into a molding process,” Bishop said.
Some OEMs see a silver lining in the green push, as the demand to lessen the footprint of both the plastics industry and the parts it produces seems likely to inspire machinery changes, and, to a greater extent, innovations in materials and end products.
“Environmentally, yes, the trend is going toward the right direction,” said Bole’s Rak, who believes the industry will continue to pursue more-sustainable solutions, in terms of materials and the recyclability of parts. “I would wish theThe machinery plastics plants use might require some upgrades.
For example, Milacron’s Hallstrom said, “there will be increased demand to run a wider spectrum of post-consumer resins, placing more demand on suppliers to develop and offer a wider range of extruder screw designs and melt delivery options.”
Foaming technologies, as well as increasing acceptance of plastic pallets and returnable packaging, could continue to see a boost from companies and customers interested in reducing their environmental footprints, Hallstrom said.
The problem extends outside the plastics plant, though, and solutions will require a holistic approach across industries, several OEM representatives said.
“I believe you are going to see a bigger push to sustainability in the plastics industry. A push for a combination of material development, machine enhancements and new technology to focus on new ways to reduce waste by reducing the weight in plastic parts for cars, aircraft, packaging and medical devices,” Maruka’s Bruce said. “This is a challenge to the plastics industry, but I see it as a huge opportunity.”
Stefan Engleder, CEO of the Engel Group, said his company already is working across the entire supply chain.
“We are supporting more and more customers throughout the entire product life cycle, from the design phase through the production phase to recycling at the end of life,” he said. “Integrating solutions along the entire value stream also contributes to greater sustainability. If we want to solve the challenges that come along with the establishment of a circular economy, we need the companies along the value chain to pool their know-how.”
One constituency compelling change will be consumers themselves, predicted Bill Duff, GM of sales and marketing for Yizumi-HPM.
“Packaging needs to be and will be, it will have a transition,” he said, as users of products rebel more and more against throwaway bottles.
Regulations in Europe, and high energy prices in manufacturing centers outside this country also will continue to spark innovations that will find their way to the U.S.
Increasing scrutiny of energy consumption creates possibilities within the automotive sector, said Engleder, who sees big changes looming for cars in the future.
Engleder, like others, acknowledged that the automotive industry had taken a hit in the past year. But he said continuing demands to lessen vehicles’ carbon footprint, as well as innovations brought about by digitization and the circular economy, will present new opportunities for plastics manufacturers. Leading the way could be self-driving cars and electric vehicles.
“In the long term, however, the industry will retain its importance and will grow again,” he said.
Getting a glimpse of the future, today
If you want to know what it would take to survive massive change, you could look at the varied responses to the upheaval experienced this year. Most OEM representatives found reason for hope, thanks to conditions that favored reshoring and sustained activity within the packaging and medical products markets.
“No one could have predicted the COVID crisis we are in and what it did to our economy. I believe it has challenged us all to be able to adapt and excel in this extraordinary time,” Maruka’s Bruce said.
At a time when physical interaction has never been more fraught, companies continued to find ways to build connections via the cloud. Several are gearing up for a return to boom times.
“The injection molding industry has reached a very exciting point,” said Engleder, just weeks after Engel hosted a virtual trade show that attracted thousands of customers and partners from 90 countries.
In the U.S., several OEM representatives applauded the effects of tariffs imposed on goods from China. Speaking just days before the U.S. presidential election, Frohring said mold work is returning to the States — and he didn’t expect that to change, regardless of any new faces that join the government in January.
“My opinion is, once you extract money out of companies in the U.S., like a tariff, they’re not going to give it back,” he said. “[President] Trump’s the one that did the dirty deed and imposed all these tariffs and, now that the government has the money, they’re not going to give it up.”
The situation makes U.S. manufacturing more competitive, Frohring and others said.
“This year has been I would say so far a record year for us,” Boy Machines’ Koorneef said. The pandemic, combined with the rancorous election — an event that every four years submerges industry in uncertainty — created headwinds that still buffet the global economy.
But, in the U.S., Koorneef witnessed something different.
“It seems to me that COVID has had a negative impact in the rest of the world, but not here in the United States, at least not for us,” he said. Sales were up, especially for machines for manufacturers of packaging and medical products. And jobs were coming back.
Maruka’s Bruce and Yizumi-HPM's Duff saw it, too.
“We are seeing molds being returned from overseas so that U.S. companies have control over parts production. This trend seems to be focused in the medical field, which has resulted in highly elevated sales for Maruka with Toyo and FCS machine sales,” said Bruce, who projected the trend will continue “for the next five years or so.”
The U.S. can’t compete on low-skilled jobs, and what remains of less-sophisticated manufacturing work in this country won’t be around forever, Duff said.
Because of that, Yizumi-HPM has turned its sights on molders willing to invest in technology, including automation. Considering the ages of already-installed machines in the country, the company is projecting growth, and gearing up to burnish an image as a technology leader.
“We’re trying to move more into providing solutions for our customers than just ‘here’s a piece of equipment,’ ” said Duff, noting that the company opened a technical center in Ohio about three years ago to help customers navigate their particular business problems.
“We’re trying to shift to that middle and upper category and move away from just supplying a squeeze-and-squirt low-cost machine. I think that, from our standpoint, you can’t make any money in that business, in my opinion, so you have to provide solutions,” Duff said.
Paradoxically, the technologies that in some areas of the plant will augment — or even replace — workers are the very thing that might lure young people back into factory jobs, he said. Filling unskilled jobs is challenging in the U.S., he said, but young workers find appeal in manufacturing’s evolving technology.
“With the introduction and expansion of Industry 4.0, the monitoring system will be able to advise on the status and maintain the machine and auxiliary equipment, track quality, track material and mold changes, product delivery and final cost,” Maruka’s Bruce said. “This will be a huge asset as finding quality labor continues to be an issue.”
As the ’20s proceed, OEM representatives look to continue to innovate.
“What I can say is as long as the United States is going to try to protect local manufacturing, get manufacturing jobs here in the United States, I think that we’re going to continue to see a positive trend,” Koorneef said. “If we’re going to stop sending our jobs overseas, the United States can only grow.”
Karen Hanna, associate editor
Contact:
Absolute Haitian Corp., Parma, Ohio, 216-452-1000, www.absolutehaitian.com
Bole Machinery Inc., Stow, Ohio, 330-983-4700, http://boleamerica.com
Boy Machines Inc., Exton, Pa., 610- 363-9121, www.boymachines.com
Engel Machinery Inc., York, Pa., 717-764-6818, www.engelglobal.com
Krauss-Maffei Corp., Florence, Ky., 859-283-0200, www.kraussmaffei.com
Maruka USA Inc., Lee's Summit, Mo., 816-524-1811, www.marukausa.com
Milacron Plastics Machinery Americas, Batavia, Ohio, 513-536-2000, www.milacron.com
Niigon Machines Ltd., Vaughan, Ontario, 905-265-0277, www.niigonmachines.com
Wittmann Battenfeld Inc., Torrington, Conn., 860-496-9603, www.wittmann-group.com
Yizumi-HPM Corp., Iberia, Ohio, 740-382-5600, www.yizumi-hpm.com
Karen Hanna | Senior Staff Reporter
Senior Staff Reporter Karen Hanna covers injection molding, molds and tooling, processors, workforce and other topics, and writes features including In Other Words and Problem Solved for Plastics Machinery & Manufacturing, Plastics Recycling and The Journal of Blow Molding. She has more than 15 years of experience in daily and magazine journalism.
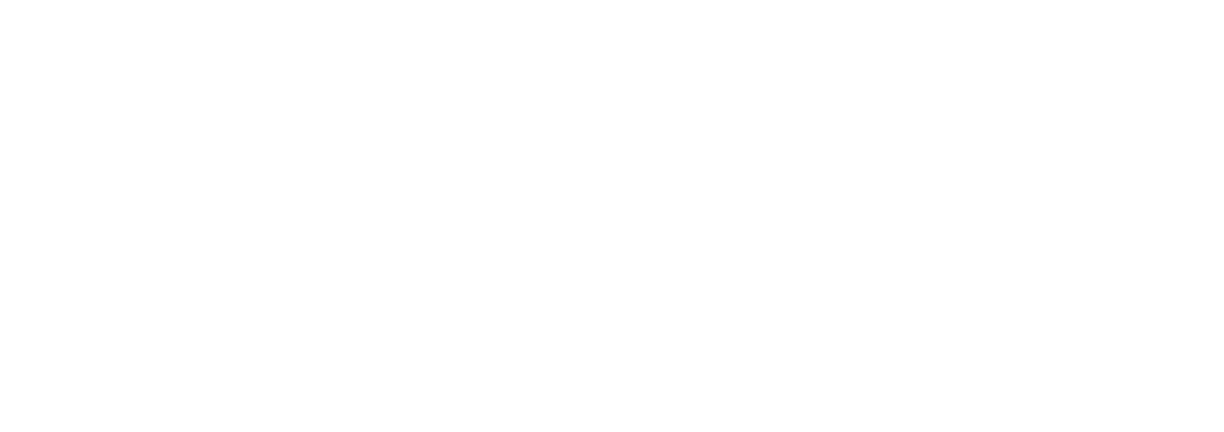