Milacron, a manufacturer of extrusion and injection molding equipment, auxiliaries and IIoT technologies, foresees increasing demand for versatile manufacturing solutions.
“The market traditionally suffered from a lack of standardized and flexible manufacturing solutions,” said Eric Hallstrom, business manager for low-pressure injection molding technologies at Milacron. “Machines today can address multiple process types, mold widely varying part geometries and mass in the same shot and can be easily converted to run parts across a broad spectrum of the marketplace with very low incremental cost of tooling. This will continue to advance, along with data-driven knowledge to assist processors to make the most of their OEE [overall equipment effectiveness].”
What new capabilities will be introduced?
New demands will be placed on OEMs as customers aim to reduce waste and new materials are developed to meet consumer demand.
“Advancement of materials [is] inevitable for injection molders and extruders as the circular economy trend grows, based on newly developed materials and consumer preferences,” said Mike Puhalla, director of engineering and technology for Milacron’s extrusion division. “The introduction of these materials will likely be the driver of innovation in machinery, equipment or barrel and screw designs to process these materials.”
OEMs will need to develop extruder screw designs to handle a wider spectrum of post-consumer resins, Hallstrom said.
Industrial Internet of Things (IIoT) platforms and adaptive molding technologies will help processors develop the best methods to process new resins. For example, iMFLUX is a process for injection molding high-quality parts using dramatically lower pressures and clamping forces. Milacron recently integrated iMFLUX control software into its machine controllers; the process is proprietary to Procter & Gamble's iMFLUX subsidiary, located in Hamilton, Ohio.
IIoT, which involves connecting devices on the production floor, will take on greater importance, Puhalla said. He foresees increased communication among automation systems that make production faster and more reliable, while reducing the workload for the operator.
“There are numerous opportunities in setting up full work cells with specialized jobs, including assembly, dispensing and sealing, machine tending, material removal, painting and coating and part transfer,” he said.
These connected, automated systems could help operators manage and streamline process settings into one screen or one point of connectivity to increase safety and reduce changeover times, Puhalla said.
As companies adopt cloud computing to manage their IIoT needs, they will be able to manage their equipment fleet globally and expand processing knowledge and solutions to common problems by sharing it among their various locations. More data scientists will be needed to discover the deep insights within this data, Hallstrom said. Milacron is expanding its workforce that supports M-Powered, Milacron’s IIoT analytical service. In addition, processors may want to make better use of their data by hiring data scientists onsite, according to Milacron.
Intelligence from IIoT platforms will allow customers to keep equipment running with an OEE of greater than 95 percent, according to Milacron.
“With the addition of IIoT or cloud computing, we believe the labor force will become more versatile as they learn from data derived from these platforms from powerful dashboards,” Puhalla said.
What will processors want?
Processors increasingly will look for machines that can handle recycled resins but also make sense for their bottom line.
“As material costs rise, processors will require the ability and flexibility from technology providers to process more recycled materials. Also, processors are engaging in a circular economy, and low-pressure machines typically excel at running up to 100 percent reprocessed or post-consumer resin,” Puhalla said.
Processors will want more assurances of performance and uptime than ever before, placing greater demand on OEMs’ engineering and quality-control systems, Hallstrom added.
Control units will continue to improve and offer additional functions.
“Controllers can perform many tasks, including running integrated systems and communicating externally to other systems and transmitting data,” Puhalla said. “These types of tasks will continue to expand and help operators and leadership in the decision-making processes.”
Improvements to control units also may boost efficiency.
“Control enhancements will allow equipment to become more adaptive to changes in resin rheology, temperatures and other parameters to help lower scrap rates and improve processing of mixed post-consumer resins,” Hallstrom said.
Plantwide connectivity can improve on-demand scheduling and lean manufacturing, he said.
“We expect data-driven production and equipment management to be key contributors to optimization of operations in the years to come,” Hallstrom said.
Bruce Geiselman, senior staff reporter
Contact:
Milacron LLC, Batavia, Ohio, 513-536-2000, www.milacron.com
Bruce Geiselman
Senior Staff Reporter Bruce Geiselman covers extrusion, blow molding, additive manufacturing, automation and end markets including automotive and packaging. He also writes features, including In Other Words and Problem Solved, for Plastics Machinery & Manufacturing, Plastics Recycling and The Journal of Blow Molding. He has extensive experience in daily and magazine journalism.
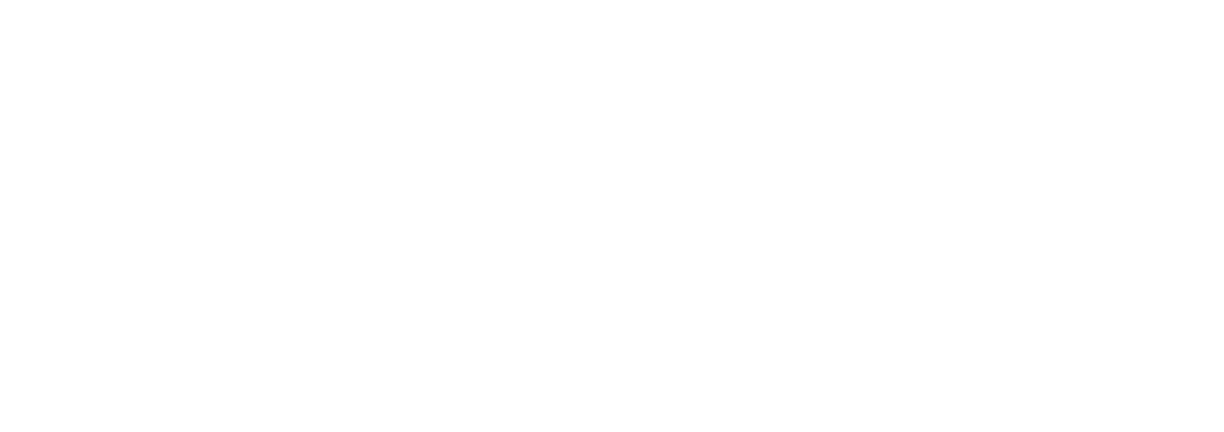