By Bruce Geiselman
MTD Micro Molding is a manufacturer of micro-molded medical components.
All tooling is manufactured in-house at MTD, resulting in a shorter and robust development process, she said.
Having a tooling department next to the molding department helps with timing, and if changes are needed, they are essentially immediate, she said.
Related: Micromolders find their fit
MTD launched in 1972 as a manufacturer of miniature tools and dies.
“Our late president Dennis Tully’s vision was that miniaturization of medical devices was going to be the wave of the future,” Executive VP Gary Hulecki said. “Then we turned to making smaller tools and brought molding in-house.”
In 2003, the company brought its first medical molding machine online. It has grown so much since then, it announced in September it had completed an 11,700-square-foot expansion of its facility that effectively doubled its cleanroom manufacturing space.
MTD’s core competency is completing projects that other molders find too challenging, Hulecki said.
“MTD practices advanced micromolding, and to us, this means projects other molders struggle with or are unable to complete successfully,” he said.
One thing to keep in mind is that micromolding does not always involve molding microscopic parts, Mann said.
“This has been proven to be one of the greatest myths of the micro medical device industry,” Mann said. “In many instances, micro part features that can be seen with the naked eye require more specialized tools and techniques than what’s required for a microscopic part with simple geometry. In micromolding, some of the most difficult parts to manufacture are larger parts with micro features.”
“Even at 100X [magnification], the part is hardly visible,” Mann said.
The market for less invasive micro medical implants and components is growing worldwide, she said. Bioabsorbable technologies also are growing. Micro medical devices manufactured by MTD support a variety of medical applications including orthopedics; sports medicine; drug delivery; catheter-based technologies; devices for ear, nose and throat care; wound closure; and diabetes care.
“One of the biggest developments in the med device world is wearables for neurostimulation/pain management and POC [point of care] diagnostics testing including wearables for insulin delivery for diabetes care,” Hulecki said. “Devices and components are getting significantly smaller, improving convenience and comfort for patients.”
Molding parts with microscopic features introduces a host of challenges foreign to most injection molders. “Depending on how demanding the details of a given part geometry is, micro parts can begin to push the limits of how an engineer might expect a typical non-Newtonian fluid to behave,” said Patrick Haney, an R&D engineer at MTD Micro Molding. “Once you have surpassed the threshold of extreme shear and cooling rates, the resulting product (unless expertly manipulated) will rarely demonstrate the properties that are forecasted for the given material and mechanical functions. Due to these phenomena, successful micromolders must find creative and alternative ways to optimize their processing parameters to ensure that the resulting process is grounded in as much scientific data as possible.”
Additional challenges processors face when micromolding parts relate to material selection, part geometry and gate freeze.
“Material issues specifically for MTD are related to the lack of technical data available about the material from the suppliers,” operations manager John Clark said. “It is up to our engineers to use the analytical equipment we have in house to determine the best melt temperatures and mold temperatures prior to beginning to mold.”
Part geometry can cause issues in filling the part, especially when gate location restrictions do not allow for MTD’s designers to put the gate in the optimal location.
“Since the parts we deal with are so small, the best gate location at times is on a critical surface that we have to avoid,” Clark said.
Gate freeze is another common complication.
“Keeping the gate open long enough to fully pack the part is sometimes an issue,” Clark said. “We see gate freeze in less than 300 milliseconds, which isn’t a lot of time to fill the part and pack.”
“To start, our molding machines are not the traditional reciprocating screw design,” said Jared Cicio, molding and production manager. “Instead, ours have a screw that feeds an injection plunger. This gives us the ability to have small shot size and allows us to have better control of our injection velocity and transfer position. This allows us to have a lot of consistency from shot to shot and better melt uniformity compared to a reciprocating screw machine. This design also allows us to be ‘gentler’ with our sensitive materials.”
MTD also has different types of specially made screws for their machines that the company selects based on the material running in the machine.
“As an example, if a part weight is measured in hundredths of a gram, the shot-to-shot consistency on the machine must be perfected as to prevent massive part-to-part variation,” Haney said.
MTD often uses a picker-style end-of-arm tool (EOAT) to retrieve molded parts from the injection molding machines. However, to use that style EOAT, the part needs to be edge-gated, so it cannot be used with all parts.
“Instead, we need to build our own custom EOAT’s to help demold the part,” Cicio said. “Most of the time, this is achieved by creating a ‘nest’ that the part can fit into, sometimes with a vacuum assist. We also use these EOAT’s to position parts in front of our checker and in-line inspection cameras.”
MTD produces custom EOAT for each part design it manufactures.
The company uses Wittmann-Battenfeld and Mitsubishi robots, along with Cognex camera systems, for inspecting and handling parts.
When parts need to be trimmed after molding, MTD often uses specialized trimmers with micro-cutting tips, he said.
“Sometimes we need to create custom fixtures to trim the small amount of gate vestige created on our parts,” he said.
MTD uses a fluidized sand bath to clean internal areas of the flow path in injection molding tooling instead of using drills or wire brushes, which eliminates risks of contamination.
Measuring parts for quality control can be a challenge, and MTD has developed its own fixtures for holding parts while they are measured.
When measuring parts, tiny parts mean tiny tolerances, which can be challenging, Beauregard said. Lighting can heavily influence the ability to accurate measure dimensions using optical measurement systems, she said.
“We are seeing increasingly intricate geometry in the micro products we produce,” she said. “This includes thin walls, small holes and radii, etc. Accurately capturing these dimensions can be challenging.”
MTD manufactures all its tooling in house at its facility in Massachusetts.
Contact information:
MTD Micro Molding, Charlton, Mass., 800-998-5549, https://mtdmicromolding.com
Bruce Geiselman
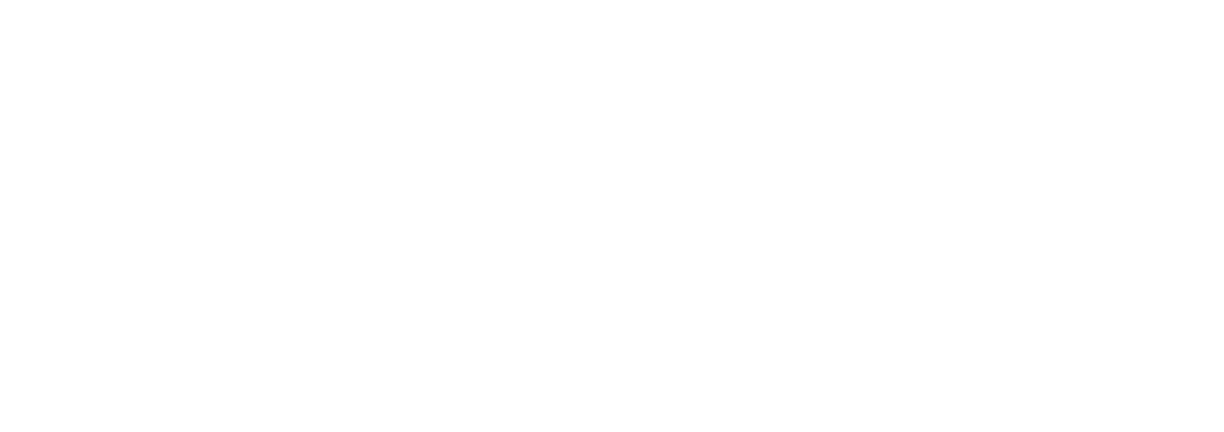