Makuta says clients ask micromolders to push the boundaries of what is possible
By Bruce Geiselman
“In terms of controlling precision, the requirements for both the mold and the processing parameters are magnified tremendously compared with traditional injection molding,” Kaplan said. “A minuscule change in material viscosity, for example, that might be irrelevant when molding a standard part could have serious implications in a micromolded part.
“We also frequently have customers bring us projects that push the envelope on size, precision, new engineering resins, etc. You have to enjoy challenges to be a micromolder, and we do.”
The smallest part Makuta has produced was an ultra-small polyoxymethylene bobbin used in miniature electrical devices. It weighed 0.0003 gram and measured 1.11mm by 0.96mm by 0.64mm.
Related: Micromolders find their fit
Makuta specializes in micro injection molding and micromold tooling, producing millions of micro- to small-sized parts each month for customers in the medical, pharmaceutical, microfluidics, electronics, office automation and automotive industries.
“Our micro injection molding capabilities include clean-room[Class 8], high-temperature, thin-wall, two-shot and overmolding, and theHe identified several areas of growth for micromolding technology.
“Medical and wearables have been very big for us, and we are also experiencing significant growth in two-shot micromolding, plus components for diagnostic devices including those that require optical clarity,” Kaplan said.
To deliver precision micromolded parts, Makuta uses all-electric Sumitomo machines in the 15- to 75-ton range, many with the SL (Spiral Logic) screw assembly, which reduces shear heat, improves molding stability, prevents burn spots and stagnation of the melt in the barrel, and allows exceptionally fast color and/or resin change-out, according to Sumitomo. Makuta’s two-shot machines also are electric Sumitomo machines.
Micromolding requires specialized primary and auxiliary equipment, Kaplan said.
“In order to develop and monitor a scientific process, molders need the proper tools,” he said. “This requires scales, pyrometers, calipers, microscopes and others. We also need our molding machines to monitor a wide range of parameters within extremely tight tolerances to ensure shot-to-shot consistency. If any of thoseMicromolding technicians require specialized skills and training. The process occupies a distinct niche within injection molding.
“Our technicians are trained in-house using methods that have been developed by us over the last 20 years,” Kaplan said. “Micromolding requires a different line of thinking, so we prefer that our technicians have less experience in other molding facilities. We train them in process development and how to implement our proprietary process building techniques.”
Contact:
Makuta Inc., Shelbyville, Ind., 317-642-0001, https://makuta.com/
Bruce Geiselman
Senior Staff Reporter Bruce Geiselman covers extrusion, blow molding, additive manufacturing, automation and end markets including automotive and packaging. He also writes features, including In Other Words and Problem Solved, for Plastics Machinery & Manufacturing, Plastics Recycling and The Journal of Blow Molding. He has extensive experience in daily and magazine journalism.
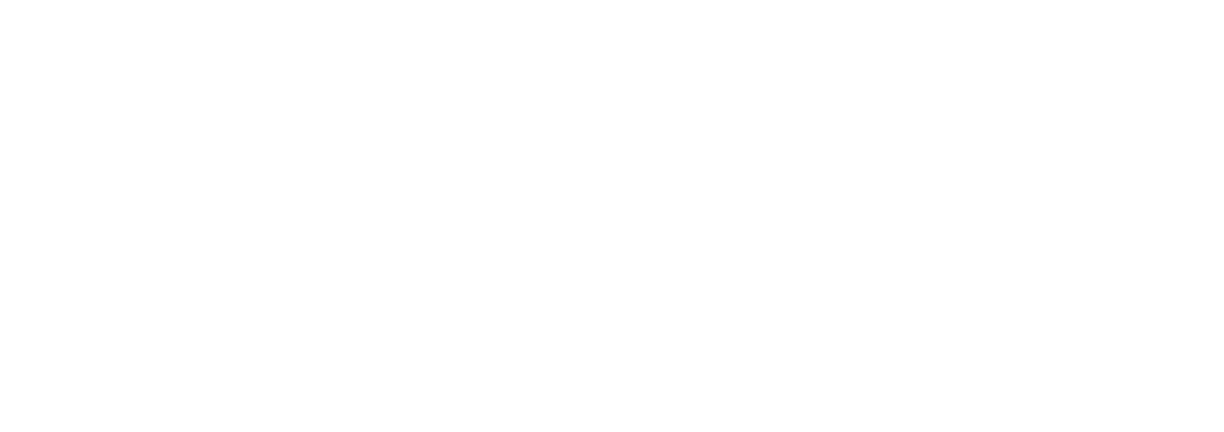