Creativity, interdisciplinary approach bring results for part designer
If you draw lines from companies that make plastic parts to companies that build machinery to make those parts, they intersect at the person who designed the part. Kenneth Pawlak is one of those product designers who uses his encyclopedic knowledge of processing machinery, resins, mold making and component functionality to bring groundbreaking medical equipment to market. Imagination, necessary in figuring out a better way to accomplish a task, is an essential part of the process.
Pawlak, who in 2016 was inducted into the Plastics Pioneers Association and in 2018 received the University of Illinois College of Engineering Outstanding Achievement Award, is semi-retired and operating the consulting business he started in 2002. He has worked with numerous medical device companies, designed dozens of medical devices and machines and won engineering and design awards. Along the way, he developed some plastics processing techniques we now take for granted.
Pawlak recently spoke to Plastics Machinery Magazine Editor Ron Shinn from his home in Vernon Hills, Ill., and shared his thoughts about his career, several of his innovations and the current generation of designers.
How did you get on your career track?
Pawlak: I was technically inclined, a geek at heart, but I did not much care for pure science. I had a good counselor at the University of Illinois at Chicago who suggested I check out the new biomedical engineering program. I liked what I saw. I was in the program’s second graduating class.
My first job was at Rush-Presbyterian-St. Luke’s hospital in Chicago in medical radiation physics. Rush had a government grant to train hospital radiation physicists due to a shortage. Then, when the aerospace industry went down, aerospace Ph.D. physicists went looking for hospital jobs. All I had was a B.S. in engineering. It didn’t seem to me that I had a future there. The hospital’s grant money ran out, and I left.
How did you get into plastics?
Pawlak: A start-up venture in EKG electrodes got me into plastics. Though not successful, it was quite an education. I had to learn to design, mold and heat-seal plastics. I enjoyed that very much. I actually had a workbench in a multi-slide tool shop to build our equipment.
What was your first plastics design challenge?
Pawlak: I had heard a presentation from a Cook County hospital Ph.D. chemist who demonstrated a prototype EKG electrode consisting of tin contact with a liquid tin chloride electrolyte in a membrane pouch. That struck me as interesting. The price of silver was going bonkers, so people were looking for alternatives to a silver contact with a silver chloride gel.
After several conversations, the start-up venture BICO was established. I designed a shallow PP flanged cup with internal PP leaf springs. The mouth of the cup had a microporous PP membrane heat-sealed across it. The membrane was new at the time, very thin, very hard to handle and cut. We came up with a technique to simultaneously heat-seal and strip the excess membrane off, leaving a smooth finish. A hole in the bottom of the cup was used for filling and plugged with a tin-plated contact. I also designed and built the filling and sealing equipment — learned quite a bit doing that. Two patents were granted for the electrode.
What was the state of the art at that time?
Pawlak: Everything was still 2-D, paper and pencil on the drafting board. CNC machining had not arrived yet. The "Modern Plastics Encyclopedia" was my plastics textbook. Sixteen-cavity molds were considered large molds then.
What was your next job?
Pawlak: Abbott Labs, in the hospital products division. They took time to train and mentor young engineers. One evening, my manager took me to a local SPE meeting and told me to start taking SPE seminars. Abbott also sent me to a North Carolina disposables assembly plant where I got to sit on the production lines. It was the type of experience young engineers don’t get today.
We had a machine shop and two injection molding machines for product development at Abbott Park in North Chicago. I got to work closely with a mold maker and machinist.
What was your toughest challenge as a designer?
Pawlak: Usually, it was to convince marketing managers that the cheapest parts do not necessarily make the most cost-effective assemblies or products, and for corporate managers to let me do things my way. I’ve been fortunate to have changed several industries with my ideas and solutions.
At Abbott, I came up with the world’s first thermoplastic overmolding patent. We had a 170-micron nylon mesh, insert-molded blood filter. During the insert molding process, molten ABS flows through the mesh, interlocking it onto the frame. We needed a 100-micron filter. The 100-micron mesh was too small for the molten ABS to penetrate. I came up with a design where we tack-molded a 100-micron nylon mesh sleeve onto the outside of the ABS frame with the first shot, then overmolded the ABS frame and mesh with a second shot in a second mold. The two ABS shots fused together. It worked very well on the first try. Abbott was granted a process patent in 1978.
During that era, trial-and-error engineering projects were supported and encouraged by Abbott. I was too young to realize the significance of overmolding. The injection molding industry embraced it years later. It was the gateway to two-shot, two-color and multishot molding, as well as overmolding different materials.
What was the most fun you had designing a new product?
Pawlak: I worked at Baxter Healthcare International’s renal division in advanced development. There, our mission was to find new technology and make products out of it. We really had a free hand. Renal was having reliability problems with their 5-foot-tall, 180-pound home peritoneal dialysis machines. The machine cycles 18 liters of solution, 2 liters at a time, in and out of the patient’s gut by gravity, while the patient sleeps. The machine had a scale to weigh and control the solution volumes during treatments. Weigh scales are fragile and easily bumped out of calibration.
We found a fluid pumping and volume measurement technology that eliminated the need for gravity flow and the weigh scale. I designed the disposable tubing set, including a compact fluid-management cassette. The cassette consists of a two-sided acrylic labyrinth encapsulated in a vinyl envelope. The vinyl envelope provided the pneumatically driven diaphragms for two pump chambers and 10 diaphragm valves. The machine was reduced to the size of a 12-pound VCR. Now portable, the new cycler was revolutionary.
Baxter was also home to the first beta SLA machine. I was among the first engineers at Baxter to utilize SLA rapid prototyping. I have been an avid user and proponent of additive technologies ever since.
What has being an SPE member since 1974 meant to your career?
Pawlak: SPE taught me good plastics design practices and introduced me to the spectrum of plastic processes. Having been chairman of the Product Design and Development and Rotational Molding divisions, as well as a board member of the Medical Plastics Division, I have many contacts to help me find what I need when I need it.
How has your profession changed since you started?
Pawlak: 3-D CAD modeling, computer simulations, mold flow, finite element analysis, additive manufacturing technologies, sensing advances make more innovation possible. To be successful, knowledge of basic good plastic design practices and plastics processing fundamentals are still needed.
Today, engineering typically reports to marketing or sales. It concerns me that MBA programs cover every business function except engineering. Sales and marketing managers often think engineers are disposable. Many design engineers today have never even seen a mold or a running molding machine in person. Many employers today do not support membership in SPE.
What are you doing in addition to occasional consulting projects?
Pawlak: I am writing a book on the history of plastics in medicine. I had been researching it for years, and I now have time to finish it.
How would you like to be remembered?
Pawlak: I would like to be remembered as a creative design engineer who contributed to advancement of the plastics and medical device industries.
Ron Shinn, editor
Just the facts:
Who is he: Kenneth E. Pawlak
Home: Vernon Hills, Ill.
Current position: Owner, Pawlak Plastics Inc.
Primary focus: Plastic product design, development and failure analysis
Ron Shinn | Editor
Editor Ron Shinn is a co-founder of Plastics Machinery & Manufacturing and has been covering the plastics industry for more than 35 years. He leads the editorial team, directs coverage and sets the editorial calendar. He also writes features, including the Talking Points column and On the Factory Floor, and covers recycling and sustainability for PMM and Plastics Recycling.
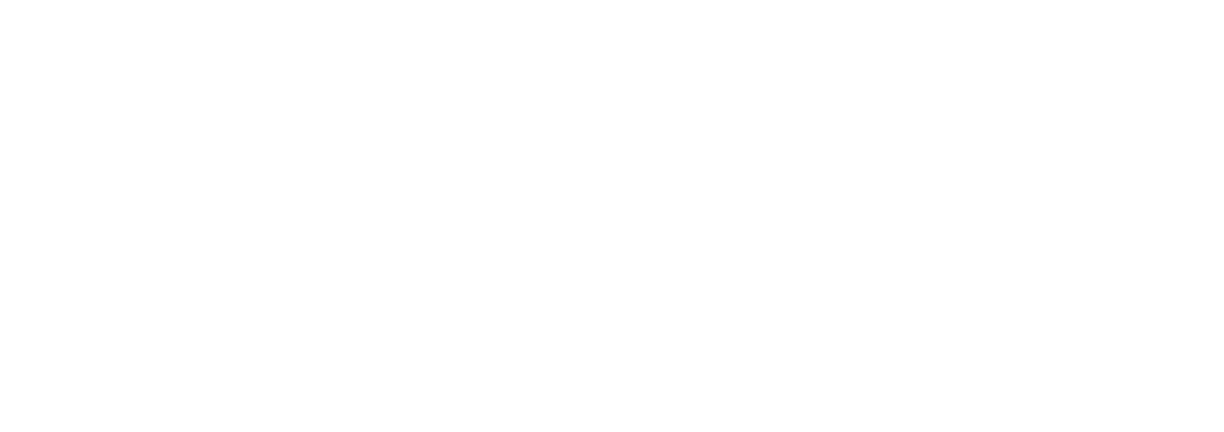