Wilmington's specialty machinery adds value to recycled materials
Part 1 of a series on injection molding machinery that tackles recycled materials and new resins.
By Bruce Adams
The unknown origin of recycled materials and contaminants included with the materials present challenges that can affect the life of machine components, according to Wilmington Machinery President Russ La Belle and Jim Boos, manager of sales and marketing.
Designing and building machines that can process a high percentage of recycled materials that some manufacturers don’t want to work with is a sweet spot for Wilmington Machinery. Earlier this year, the company introduced a new dual-mold pallet press capable of molding pallets from 100 percent recycled flake resins, including blends.
“We tout our machines as being capable of processing 100 percent recycled materials even in flake form,” La Belle said. “That means you are taking materials that have not gone through filtration, through extrusion, and you are seeking to come up with a usable material for making more utility-like products.”
Products such as pallets, storage bins, underground boxes for electrical equipment and water tanks are good candidates to be made from large amounts of recycled material because the surface quality and color of those objects are not key issues.
“Recycled materials lend themselves to utility-like products,” La Belle said. “With engineered materials, they might be looking for a superb surface quality. With pallets or a utility box, they are not looking for those qualities. They are looking for strength, impact resistance and deflection.”
Related: Engel adapts to circular economy
Another important consideration is cost.
"For a plastic pallet to compete with a wooden pallet, the key is the cost of the plastic raw material,” La Belle said. “Being cost-competitive forces processors to use recycled materials.”
“With recycled materials, we often get mixed colors,” Boos said. “We add coloring to it, but we are limited to black or very dark colors. High-quality finishes are out of the question with recycled materials in their least-expensive form because in many cases you get black. When you take a bunch of mixed colors and make something out of it, you don’t get to choose what color you want the end product to be.”
Wilmington Machinery customizes its injection molding machines to handle inexpensive recycled materials.
“We do things differently by putting a full-blown extruder, meaning an extruder that has a long L-over-D [length-to-diameter] ratio,” La Belle said. “On a high-pressure injection molding machine, you may have a very short L-over-D screw, about 18 or 20 turns. We typically are at a full 30 turns. We have put extruders on molding machines that had as many as 36 turns. That allows us to do a much more intensive job of melting and mixing — especially mixing. We also put multiple mixing sections on the feed screws.”
He said the results they achieve defy the “garbage in, garbage out” axiom.
“We are putting in recycled materials in their worst form, flake form, but getting a decent-quality melt coming out the other end of the extruder due to the long L-over-D ratio and the mixing that takes place in it,” La Belle said. “We have an injection molding machine in our lab, and we do this work routinely.
“We’ve had a lot of people come to us that want to take low-density polyethylene materials that have been recycled. As a pallet material, a lot of times that will not give you the flex modulus that you would want for a pallet, because a pallet needs good, stiff material. But what we found in our lab is that by blending that low-density material with other materials — and these blends are proprietary to our customers — we achieve hybrid materials that have phenomenal properties.”
The company also has modified its machinery in the last few years to better handle recycled materials.
“We have done two things,” La Belle said. “The metal components that go into the machines are more wear-resistant. We have changed the hardness and the types of metals to get greater wear resistance due to the contaminants. Also, the screw designs have evolved, meaning the feed screws in the extruders, their design has evolved to achieve better mixing.”
The result is that the company’s machines have been designed to create products from difficult-to-process recycled materials.
“We believe that we have the best solution for effectively dealing with recycled materials and for getting a quality melt out of something that isn’t very good,” La Belle said. “People have sent material to us that they did not believe could be processed in an injection molding machine, and we have done it. That is bragging a little bit, but it is the truth.”
Even with custom designed injection molding machines, there are times when specially designed auxiliary equipment also is needed to process some recycled materials.
“We have had success feeding powders into injection molding machines that otherwise would not be fed readily,” La Belle said. “In some cases, it takes auxiliary equipment, like crammers, to increase the extrusion rate of these materials, to make sure that the feed is consistent. We’ve also found that it takes special equipment at times to dry materials. I don’t mean off-the-shelf dryers, but dryers that are specially engineered to keep up with the feed rate.”
A crammer is a piece of equipment that’s set up at the hopper and feeds recycled material into the extruder. It forces the material down onto the screw.
“A crammer is almost like an auger that puts enough pressure on the material to force feed it to the extent that it is trying to overfeed the extruder,” La Belle said. “In doing that, you can get the extrusion rate up to where it would have been with a higher-bulk-density material.”
A crammer might be needed because inexpensive recycled material has a low bulk density and it doesn’t feed at the rate that’s needed to flow into the extruder.
“Powders get down to the screw and want to slip,” La Belle said. “The crammer puts pressure on the material to make it feed better in the extruder. The other way to overcome the low-bulk-density problem is to only run a certain percentage of the low-bulk-density material. That in turn may make a difference in the blending/loading equipment, as to whether that has the capacity to keep up with the low-bulk-density material.”
Processors often encounter this problem if the bulk density of the material they are using is less than 20 pounds a cubic foot, he said.
While a crammer increases the cost of the setup, processors benefit by being able to use less-expensive raw materials.
“Processors want to use the low-bulk-density material because it is the least-expensive material available,” Boos said. “As the machinery manufacturer, we help our customer make that decision to put a crammer onto the machine so their process will run smoothly.”
For more information:
Wilmington Machinery Inc., Wilmington, N.C., 910-452-5090, www.wilmingtonmachinery.com
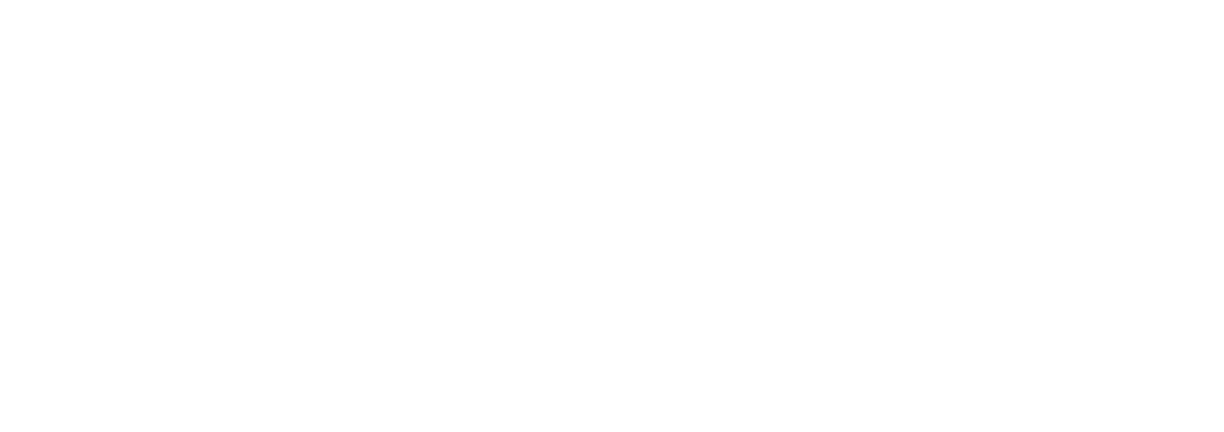