By Bruce Adams
Wilmington Machinery has introduced a structural foam molding machine for pallets that’s available as part of a turnkey system and is designed for versatility, economy and ease of use with minimal labor requirements.
The Lumina Pallateer-series Model PM-3S can mold two identical or different pallets measuring up to 52 inches by 48 inches and weighing up to 50 pounds each. It offers production rates of 48 to 72 pallets per hour, and can mold nestable, stackable or rackable pallets of one-piece and two-piece construction from a wide variety of virgin or 100 percent recycled flake resins, including blends. It can use nitrogen gas or a chemical foaming agent.
The PM-3S can be purchased as a stand-alone machine or as part of a complete turnkey system that includes the molding machine, two molds, a robot and all the required accessories and training.
“The turnkey solution includes a robot to remove both pallets at the same time. It will stack them or place them on a conveyor,” said Jim Boos, manager of sales and marketing at Wilmington Machinery. “It also includes two pallet molds, a resin blender/loader that blends and loads the material into the hopper, a chiller and a nitrogen generator. We also offer an optional granulator to grind up off-spec parts, an optional hot-plate welding system and other accessories.”
Many of the company’s pallet machine customers prefer turnkey systems because they often are not experienced injection molders, he said.
“Our pallet customer tends to be new in the plastics industry,” Boos said. “Our general-purpose machines often are purchased by contract molders who have other injection molding equipment. They have more equipment and more knowledge in plastics processing than some of the pallet makers who need a turnkey solution.”
Wilmington Machinery now offers nine pallet-making machines in its Lumina Pallateer series.
“All Pallateer-series machines are designed to efficiently make plastic pallets,” Boos said. “A pallet is typically only about 6 inches tall. The Pallateer-series machines are shorter-stroke machines and a lot less expensive. They are geared to make plastic pallets or plastic matting, or any large industrial components with a minimal height. You don’t need 108 inches of stroke that’s offered on a general-purpose molding machine to make a 6-inch-tall pallet. General-purpose machines are long-stroke machines used to make tall or deep products, such as bins or components with a lot more height.”
The PM-3S model borrowed traits from two similar Lumina Pallateer-series machines.
“The PM-3S came about as a hybrid of the PM-3 and was designed to fill a need that we thought was in the market,” Boos said. “The PM-3 is an excellent machine but is limited by pallet size and pallet weight. Key differences are that the PM-3S has a 6-inch extruder and a 100-pound plastic accumulator, which is larger than the PM-3. It also has an increased platen size.”
The company uses the extruder from its PM-4 machine, which has a larger shot capacity than the PM-3, on its PM-3S machine. The PM-4 is a longer-stroke machine for stack molding. It can make four pallets at the same time using two stack molds.
Both the PM-3 and the PM-3S have a two-stage injection unit and an L:D ratio of 30:1. Both machines can use 100 percent recycled resins and accommodate fillers and additives. The two-stage injection unit includes the extruder and an accumulator, which also is called a shooting pot.
“As the screw turns and melts the plastic, the plastic is transferred from the extruder to a crossover into a shooting pot, or plastic accumulator,” Boos said. “The plastic is accumulated in the shooting pot, in this case, up to 100 pounds of plastic. When the shot size is accumulated, the extruder turns off and the hydraulic ram pushes the melted plastic into the molds from that shooting pot. In a high-pressure machine, the plastic is generally accumulated in-line with the screw, in front of the screw. In this case, we accumulate it in a separate device located next to the extruder.”
Pallateer-series machines are available with Beckhoff or Allen-Bradley controls. A sequential ejection control system called Versafil is standard on the machines.
“Versafil gives you the ability to open and close nozzles sequentially during injection to place the plastic where you want it to go in the mold,” Boos said. “Or it will allow you to shut off the plastic to a certain part of the mold. It gives you versatility in where the nozzles place the plastic in the mold and in what order they fill it.”
The standard PM-3S machine has an injection speed of 10 pounds per second, with an optional 20-pounds-per-second injection unit available. Faster injection rates improve cycle times and part strength.
The PM-3S has 500 tons of clamping force, which might sound scant to general-purpose molders.
“Structural foam is a short-shot process because of the nitrogen gas and the foaming of the plastic,” Boos said. “The mold cavity is not filled completely with plastic. It is shot short with plastics and then the nitrogen gas expands inside the mold, forcing the plastic to fill the rest of the cavity. This allows for the use of lower-cost, lightweight aluminum molds due to the lower pressure. Cavity pressures are about 350 psi in the mold due to the nitrogen gas and the short-shot process.
“If you were trying to fill the cavity with solid plastic, like a high-pressure machine, you would need pressures five times or more than what we use because they are not using gas to fill out the mold. They are using force. The gas allows the plastic to flow easily and the pressures are low because we don’t completely fill the mold cavity with plastic. The gas keeps the machine pressure low. If this was a high-pressure machine without gas, it might be a 3,000-ton machine. Our clamping forces are much lower because our cavity pressures are much lower due to the nitrogen.”
The company said it is not locked into offering identical Lumina Pallateer machines to all customers.
“Some customers may end up with a hybrid of one of our machines,” Boos said. “We are not trying to force customers into a machine that doesn’t fit their needs. We work off our base models and go from there.”
Wilmington Machinery also offers in-house pallet design.
“If you don’t have your own design team, we will design the pallet and turn that into a mold for you,” Boos said. “If you come to us with a picture of the pallet you want to make, we can help design the pallet and the mold to make that pallet, and we will do the complete system and turn it into reality. We can provide anything you need to make plastic pallets.”
The PM-3S is a hybrid machine with hydraulic injection and hydraulic press movement. Electric motors drive the screw and all hydraulic pumps.
“It is designed for low energy consumption with the smallest electric motors to get the job done in combination with the hydraulic valving,” Boos said. “We designed it for lower power consumption than the PM-3.”
The turnkey system was designed to operate with one person.
“Once the machine is in continuous cycle with a complete turnkey system, the operator is monitoring the process,” Boos said. “The operator needs to make sure the machine doesn’t run out of plastic resin. The machine is doing everything itself. The pallets are being removed from the machine by a robot and being stacked on conveyors. We tell our customers it takes one and one-third of a person, the one-third to drive a forklift for multiple machines running at the same time.”
Wilmington Machinery partners with Ranger Automation Systems Inc., Millbury, Mass., on its Pallateer-series machines.
“We are proud that this is a U.S. company, a U.S.-manufactured machine, and it’s consisting of primarily U.S. components,” Boos said. “We don’t buy steel machined components from overseas. A lot of the electronics are not made in the U.S., but we try to source U.S. components. The platens, the doors, all the machined steel components, we design and we procure in the U.S. and Canada. We don’t go overseas to buy our machined steel components.”
Bruce Adams, senior staff reporter
Contact:
Wilmington Machinery Inc., Wilmington, N.C., 910-452-5090, www.wilmingtonmachinery.com
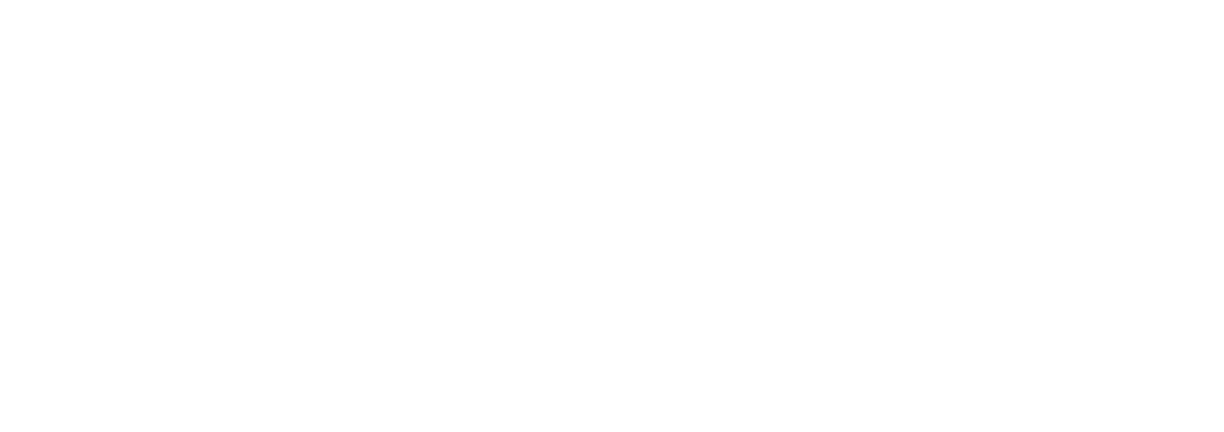