CoPilot RJG’s process-monitoring and control package includes software and sensors that perform a number of functions, including monitoring injection molding machines, managing rejects and creating process change logs. With CoPilot, users can monitor data collected by their machines.
What’s new? A new version, called CoPilot+. CoPilot+ offers features that are not available with the original CoPilot. Working along with cavity-pressure sensors, CoPilot+ can transfer an injection molding machine from fill to hold based on cavity balance. It uses in-cavity data to spot problems with parts and can help balance hot-runner molds. In addition, CoPilot+ makes possible automatic part sorting, to ensure that no bad parts are shipped.
Benefits Process simplification. Like CoPilot, CoPilot+ software displays red or green graphics on a screen so users can see at a glance if a press is performing as expected. Compared with the first version, the latest iteration offers greater process control.
RJG Inc., Traverse City, Mich., 231-947-3111, www.rjginc.com
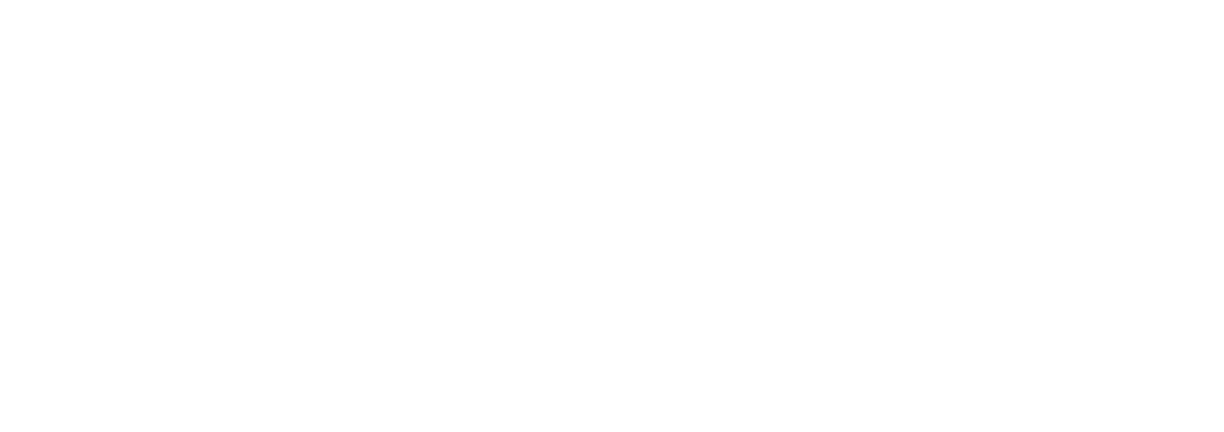