Molding lightweight parts requires the right injection molding machine and auxiliary equipment combined with the right process and materials. Most manufacturers say a wide range of their presses can be used to make lightweight parts.
Arburg
“You can do lightweighting with every Arburg machine by using high-performance materials,” said Manuel Wöhrle, senior sales manager for lightweighting at Arburg. “For special processes like physical foaming or Fibre Direct Compounding, we have a special adapted injection unit to produce lightweight parts. In Fibre Direct Compounding, we bring in glass fiber, cut it and feed the cut fibers directly into the melt, so we get longer fibers in the part.”
The company’s series of Allrounder injection molding machines can be adapted to various complex lightweighting processes. Several Allrounder machines are available at the Arburg Customer Center in Lossburg, Germany, to test different processes.
Arburg’s ProFoam process creates fiber-reinforced foamed parts with high-quality surfaces, the company said. A gas blowing agent is added to the resin pellets upstream of the injection unit, which makes them flow faster. During plasticizing, the blowing agent diffuses into the melt. The ProFoam process requires an injection unit with a position-regulated screw and pressure accumulator.
If the component being made is appropriate for foam-molding, manufacturers can experience benefits beside lightweighting.
“The physical properties of the blowing agent and foam-appropriate component and mold optimization often enable the cycle time to be reduced,” Wöhrle said.
Engel
Engel touts its organomelt process to produce lightweight thermoplastic components. Fiber-reinforced thermoplastic prepregs, such as sheets and tapes, are heated, inserted into the mold, formed and overmolded. Precise process control is key to organomelt because the process normally involves multiple robots and infrared ovens. At K 2019, Engel used the organomelt process to make an automotive part.
“The heating and shaping are a core aspect of the organomelt process,” said Norbert Müller, head of Engel’s Centre for Lightweight Composite Technologies. “You cannot have continuous fiber reinforcement with pure injection molding, so you need to bring the heating and shaping option to it. The heating must be done quickly but without harming the materials. When you have different-thickness components in one process, the thin one is heated quite quickly and cools down very fast. The thicker one needs a longer time to heat up before you bring it into the mold. These need to be adjusted to each other.”
A variety of injection molding machines from Engel can be used to perform the company’s organomelt process. “The machine itself has specific capabilities concerning process control to run additional modules, such as robots and infrared ovens, but it is very similar to a typical injection molding machine,” Müller said.
“There is the opportunity to combine multiple parts into a single part that might cost less, do multiple things and weigh less than all the parts it is replacing. This needs to be done in close cooperation with the part designer. Talk to the designer and stay within the cost constraints.”
Wilmington Machinery
Wilmington Machinery recently introduced the Lumina MP800R injection molding machine. This medium-pressure press offers greater extrusion capacity, greater shot capacity and a higher injection pressure than the previous MP800. The machine can mold much thinner walls than the company’s previous model, Wilmington Machinery President Russ La Belle said.
“The MP800R was developed with lightweight parts in mind,” La Belle said. “It offers direct gas injection into the barrel. It is a foam injection machine with physical foaming agents, including nitrogen or carbon dioxide for direct gas injection. It also can be used with chemical foaming agents.”
The machine features a separate mixer that mixes the gas with the plastic. The gas is injected by high-pressure pumping or compressing. The gas improves melt flow into the mold and reduces the density of the component for thinner-walled parts.
Mike Uhrain, technical sales manager of packaging for North America at Sumitomo (SHI) Demag, recommends the company’s hybrid El-Exis SP machines for high-speed injection molding, including thin-walled packaging.
“As parts get thinner and lighter, the cooling time decreases, so you need to make them a lot faster and have a very high injection performance and a very fast-running machine,” he said. “As you thin out products, the cavity pressure increases and puts a lot of pressure on the surface of the platens. You need very stiff platens so you don’t have any platen deflection or core shifting. The El-Exis is a very stiff and robust machine that is very fast-cycling.”
The company touted the fourth generation of its El-Exis SP range as “the fastest injection molding machine in the world” at K 2019. Key to the machine’s fast cycle time is its hydraulic accumulator, which achieves injection speeds of up to 1 meter per second, the company said.
Wittmann Battenfeld
Wittmann Battenfeld offers its proprietary Cellmould foaming technology and Airmould gas-assist technology for lightweighting parts. With Cellmould, gas is directly injected into the melt with a physical foaming agent (usually nitrogen), producing structural foam parts. The parts are characterized by a compact outer layer and a foam core. Cellmould can produce thin-walled and thick-walled foam parts that are rigid and have no sink marks, according to the company, which provides all needed equipment for lightweighting parts.
“We produce auxiliary equipment in-house so we can offer customers a nitrogen-generating unit, a pressure-generating unit and all the modules to control the gas flow for the gas-assist technology and for the foaming technology,” said Wolfgang Roth, head of application engineering and exhibitions for Wittmann Battenfeld. “Our gas injectors for Airmould technology are mounted in the mold. For Cellmould, they are mounted directly in the barrel of the injection molding machine.”
Wittmann Battenfeld presses from the EcoPower, SmartPower and MacroPower series can be combined with additional equipment to manufacture lightweight parts using the Cellmould technology. The best machine to use depends on the part. One modification required by the Cellmould technology is a special screw that’s different than screws on standard injection molding machines.
“For lightweighting, normally you start at 100 to 150 tons of clamping force and go up to 2,000 tons. We have a wide range of machines in that profile,” Roth said. “We have special injection units for special materials like reinforced polymer materials where you have glass or carbon fibers.”
Different types of parts and machine sizes require different gas-pressure equipment. To meet all types of requirements and conditions, Wittmann Battenfeld developed the Airmould module system. It consists of a pressure generator, a process controller, gas-pressure controller and gas injection equipment.
The pressure generator compresses nitrogen and is available in different sizes and capacities to supply a single machine or multiple machines. For applications that don’t use much gas, the company recommends nitrogen bottles or gas cylinder manifolds. For high consumption of nitrogen, the pressure generator can be combined with a nitrogen generator. The process controller can be monitored and controlled by the machine’s control system or via the touch screen of a separate control cabinet or a manual control unit. The gas-pressure control module can be mounted near the mold to keep gas pipes as short as possible. Gas is injected either through the Airmould machine nozzle or by gas valves inside the mold. The nozzle’s connection dimension is the same as a standard nozzle so it can be retrofitted to fit any machine.
The Airmould module system can be used on presses made by other companies.
Bruce Adams, senior staff reporter
For more information
Arburg Inc., Rocky Hill, Conn., 860-667-6500, www.arburg.com
Engel Machinery Inc., York, Pa., 717-764-6818, www.engelglobal.com
Sumitomo (SHI) Demag, Strongsville, Ohio, 440-876-8960, www.sumitomo-shi-demag.us
Wilmington Machinery Inc., Wilmington, N.C., 910-452-5090, www.wilmingtonmachinery.com
Wittmann Battenfeld Inc., Torrington, Conn., 860-496-9603, www.wittmann-group.com
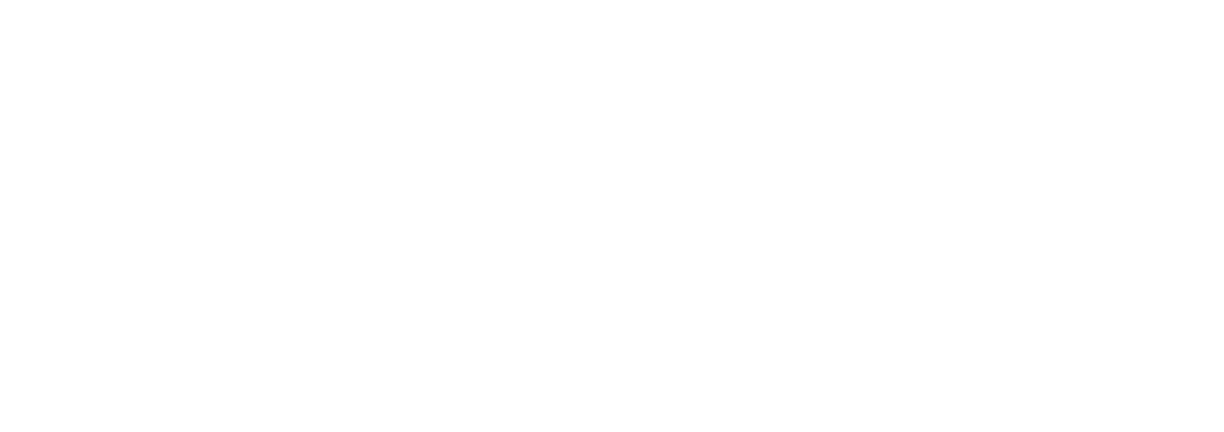