Lightweighting injection molded parts has never been more popular than it is now, according to machinery OEMs.
The ability to optimize the material used to create a particular part depends on several factors, including cost and desired mechanical properties. But a number of developments, including advances in molding fiber-reinforced parts, foaming agents, machinery and part design software, have meant that manufacturers have not yet hit the limits of lightweighting.
“The goal always is to make a lighter part that also is cheaper and better in mechanical properties,” said Manuel Wöhrle, senior sales manager of lightweighting at Arburg. “The best way to lightweight is to start very early in the part design to think about how to improve the part. Adapt the part design to a special process or a special material. Optimize the part, reduce the wall thickness and produce the part with special processes to get good mechanical properties on a lighter part. After the part design is finalized, it is too late to achieve lightweighting. You don’t have all the possibilities to reduce the maximum amount of part weight.”
Lightweighting techniques include foaming and the substitution of relatively heavy materials with lighter-weight ones.
OEM representatives said that automotive, transportation, logistics, medical and electronics products are key targets for lightweighting. According to Wilmington Machinery President Russ La Belle, consumer products and footwear makers also are keenly interested in lightweighting. His company is working to design a lightweight component for an athletic shoe.
Consumer goods such as electronics are ideal for lightweighting, according to industry experts.
“Many of the parts inside [a] printer are made of foam material and lightweight materials,” said Wolfgang Roth, head of application engineering and exhibitions at Wittmann Battenfeld. “The surface quality of those parts is not important because nobody sees them.”
La Belle agreed and said the housings for laptop computers weigh considerably less than earlier versions. “Today’s version is like a feather in your hand compared to the first laptop,” he said.
At Engel, most lightweighting activities address the needs of the automotive industry, said Norbert Müller, head of the company’s Centre for Lightweight Composite Technologies. The company works with a large group of Tier 1 automotive suppliers, as well as with car companies, to design and build lightweight parts.
“We contact the original equipment car manufacturer and they discuss what part might be in the next generation of lightweight components,” Müller said. “The real development normally is done in cooperation with Tier 1 suppliers. They have to produce some concepts for how they might view the next generation of a part. They are taking a close look at composite technology solutions. Most of the development work we are doing now is focusing on thermoplastic materials. We also have solutions for thermoset composite components, based on epoxy resins or polyurethanes. You also can have a fully automatic running line in thermosets, but the cycle time is longer, usually a couple of minutes.”
Engel has about 20 employees in its lightweight technology business group.
How low can you go?
“Since many years ago, customers have been using long-fiber technology and foaming to achieve lightweighting,” said Mike Uhrain, technical sales manager of packaging for North America at Sumitomo (SHI) Demag. “Lightweighting has always been a trend in the automotive and packaging industries. One of the differences is that with packaging today it’s getting lighter and lighter and we are almost reaching a limit. But we are not there yet.”
New lightweight parts will continue to be developed and existing lightweight parts will continue to be made even lighter, as long as the process does not affect functionality, experts said.
“There always is technology that comes out that allows parts to be thinner and lighter-weight that were not previously possible,” Uhrain said. “For example, injection compression molding is a very mature technology that has been used for more than 30 years to lightweight vehicle parts such as splash shields and other parts that had been made out of metal.”
Adding long fibers allows processors to produce stronger, lighter parts. That’s even helped injection compression molders, who previously could not make thin-wall parts. “But in the last three to four years the market has been investing a lot of resources into this technology on the machine side, the mold side and the part side. So, you can even injection compression mold thin-wall containers now. It is an existing technology that was repurposed for a different market, but the machine and the mold technology have to evolve to be able to implement that,” Uhrain said.
Foaming agents, which once were corrosive to molds and generated heat that increased cycle times, also have evolved. “Now with new foaming agents, it’s an endothermic process, so it is absorbing the heat and it can actually shorten cycle time and you can get a good surface quality on the part. Some of the reason for that is, if you can inject faster, you can get a better surface quality,” Uhrain said.
Improved machinery also contributes to lighter-weight parts.
“You can use a machine with higher injection rates, inject faster, get more foam in the part and get a better surface quality,” Uhrain said. “That didn’t exist many years ago. It was a different process, and processors regarded foam as giving a very poor surface quality to the part. Today, you can even lightweight parts that have a high aesthetic finish requirement.”
Limitations
The need to preserve the part’s mechanical properties, as well as to keep costs down, restricts how much weight a manufacturer can cut.
The part itself poses the biggest limitation to lightweighting, according to Roth at Wittmann Battenfeld.
“If you add a physical foaming agent, you have a viscosity change, so the material flows better,” Roth said. “You can achieve a thinner wall thickness than without the foaming agent. But if you go to an extremely low wall thickness, 0.2mm or 0.3mm, it is very hard to do because you have limits from the molding side and a certain weight is required for the mechanical properties of the part.”
How much weight can be cut from a part varies based on its requirements. He said one example of a part that can lightweighted to an extreme degree is a noise-reduction highway barrier wall, because there are no mechanical influences on the wall and the surface of the product does not have to be perfect. It only has to be able to withstand heavy winds and weather.
Engel’s Müller cited cost as another consideration.
“In the automotive industry, we know we can make a lightweight part that is even lighter by using carbon-fiber materials,” Müller said. “We also could use glass, fabric or non-woven material that is combined with polypropylene. But the current part is considerably less expensive than the carbon-fiber solution would be. For large-volume car parts, we usually talk about glass plus polypropylene. The glass costs less than carbon.
“There is a gap between what is possible and what is done. The most important thing is to stay within the cost region that the customer expects us to be in.”
Simulation programs that predict the performance and weight of parts designed from various materials are improving and they help part designers create lighter-weight parts, Arburg’s Wöhrle said.
Wilmington Machinery’s La Belle predicted lightweighting will continue to evolve because it’s human nature to try to improve on processes that already are good.
“Technology and raw materials will continue to improve, design will continue to improve and other techniques associated with the mold or the machine itself will continue to improve,” La Belle said. “Processing knowledge continues to grow. In the old days, people viewed processing as an art. Today, it’s still an art to find the right solution. The difference being today, once you find that solution, it becomes very scientific as to how you hold that precisely. The computer and machine controls enter into this to control the process. It will be an ongoing evolution, for sure.”
Bruce Adams, senior staff reporter
For more information
Arburg Inc., Rocky Hill, Conn., 860-667-6500, www.arburg.com
Engel Machinery Inc., York, Pa., 717-764-6818, www.engelglobal.com
Sumitomo (SHI) Demag, Strongsville, Ohio, 440-876-8960, sumitomo-shi-demag.us
Wilmington Machinery Inc., Wilmington, N.C., 910-688-3052, www.wilmingtonmachinery.com
Wittmann Battenfeld Inc., Torrington, Conn., 860-496-9603, www.wittmann-group.com
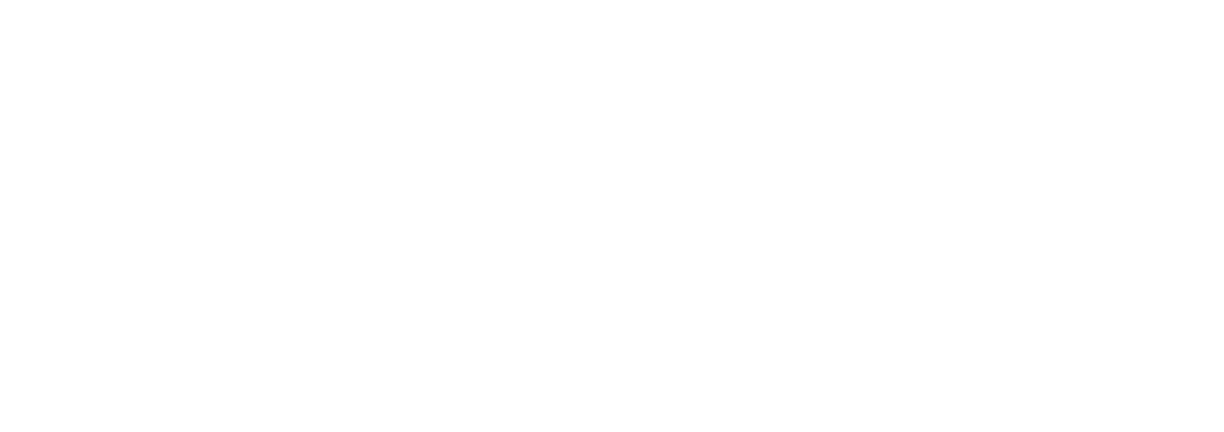