Len Czuba: A leader in medical device design and manufacturing
Czuba has 15 patents for materials or designs for medical devices and is a veteran trainer. He discussed his career with Plastics Machinery Magazine writer Bruce Adams.
How has the evolution of machinery and equipment, particularly of all-electrics in injection molding and blow molding, contributed to the advancement of medical devices?
Czuba: Improvements in injection molding presses, as well as ancillary equipment for molding machines, help processors make better parts with better tolerance control, tighter process windows, reduced scrap and far less material property degradation as a result of the processing. Many molders are locating their machines in clean rooms or in molding suites that are entirely enclosed as certified clean rooms. The evolution from hydraulic to all-electrics significantly improves the long-term cleanliness and reliability of the equipment to exist in cleanroom environments, eliminating the inherent contamination that comes from the non-electric presses.
While everyone understands the need for cleanliness in medical devices and device components, other industries, such as electronics, computer hardware, pharmaceutical and telecommunications also require extreme cleanliness and purity in their plastic parts. The issue is not only maintaining cleanliness.
Newer evolving machinery brings better process control and, for some extreme materials, the tighter control of temperatures, pressures, shear stresses and residence times all help maintain the material properties, avoiding the typical degradation of physical properties typical of older equipment. Better controls mean tighter process windows and better properties in the components and finished parts. This results in better functioning medical devices, improved reliability, faster medical procedures with fewer complications and better patient outcomes. The miniaturization of medical devices is made possible by, and often relies on, the advances made in robotics, vision systems and telecommunication approaches.
Many machinery manufacturers, both primary and auxiliary, have attempted to make building a clean room as smooth as possible with compliant systems. Do you see that as helping medical device manufacturers, especially with FDA compliance?
Liquid silicone rubber (LSR) has received a lot of attention in recent years. This is a three-part question: What has played a bigger role in advancing this material — the primary equipment or the mold designs? How effective are bolt-on injection units for this material? How has the material contributed to better design of medical devices?
Czuba: The development of LSR with extremely good properties started this evolution. The ability to be molded faster, easier and at lower temperatures and shorter cycle times has led to the development of newer device designs and the machinery and equipment that allow design engineers to take advantage of the new material properties. Although much of this has been concurrent development, I would proffer it is material first, then the equipment to process that material and finally the device designs that take advantage of the materials in the newly designed medical devices. I don’t know much about the bolt-on units but I am aware that there are now hybrid devices being made in which a thermoplastic is molded in one step and then in an over-molding second step, silicone is being molded over the plastic part. These parts then bring to the product the advantages of each type of polymer being used.
How did you become involved in plastics engineering? How did you become involved in medical devices?
Czuba: My first job after my degree was working in a polymer and chemistry support lab for a company making high-voltage switches and fuses. Plastics were just entering the traditional metal and ceramic products offerings. At that company, I learned about mixing and molding liquid epoxies, compounded thermoplastics and operating the various mechanical testing and analytical equipment needed to support the use of the various materials. Within a year or so, I was lucky enough to get an offer to join Baxter Labs working in the polymer synthesis lab of one of the most talented polymer scientists in the world, Dr. Dean Laurin. I jumped at the chance to work on polymers for medical devices, which fit well with my training in biosciences. For years as Dr. Laurin’s assistant, I learned polymer synthesis (wet chemistry), most types of polymer processing from compounding to molding and extrusion. We did the early phase new-product development for plastic IV bags, blood bags, various tubings, catheters, connectors and all sorts of devices and accessories. It was very exciting! Dr. Laurin encouraged me to get involved with SPE and attend some of the training courses they offered, which I did.
During my 20 years at Baxter, I developed quite a few new polymeric materials and devices, many of which are still in use today. With 15 patents and a long list of attending training courses, I became an expert in some medical devices and the materials of construction. I started getting invited to give presentations on my work and the developments that resulted in the patents and the new medical devices. As an SPE volunteer, I participated in organizing many technical conferences for industry professionals worldwide. Although I don’t consider myself an expert in the field of medical devices, I can do a good job giving introductory training to others interested in learning about the device industry and the many exciting aspects of this industry such as material selection, device component manufacturing and assembly, product packaging and sterilization. I am still involved with new product development for several companies, but I’m also involved with producing training programs in all aspects of the plastics industry from injection molding to extrusion, blow molding, thermoforming, making and using thermoplastic foams and an assortment of polymer analysis courses.
What was your first major breakthrough in medical device design/manufacturing?
Czuba: My first patent was for a material that was intended as an alternative for non-DEHP plasticized PVC for blood and intravenous solution storage. It was found to be an excellent storage material for donated blood platelets which extended the shelf life of the platelets by more than 100 percent from three days to seven days. Having extended shelf life for stored blood platelets allows them to be used much more effectively for more patients that need platelets, including hemophiliacs. But this blood bag material was the first in a line of PVC alternative materials that I along with my Baxter colleagues developed over many years in the labs, many of them patented and later put into use. Some of these materials are still in use today and others are waiting for the day that current materials are no long the optimum polymers for the applications.
What have you been working on lately?
Who takes your training and what do they learn?
Czuba: Mostly design engineers, especially those from small or start-up companies. We also get sales and marketing professionals who are new to the industry and staff from start-up companies who are asked to develop a new device from napkin sketch to market introduction. I focus on the basics of making a new medical device covering materials, processing options, assembly, how devices can be sterilized and why each method is used. I also review all the testing that is done on medical devices to get them ready to enter the marketplace.
What evolutions in machine technology have had the greatest impact on your business or the medical device design business as a whole?
Czuba: The systems that allow control and monitoring of all aspects of a machine from temperature in each distinct location, pressure, speed and in process adjustment all makes for better product output. The ability of computer systems to track and record all the variables and the ability to provide alerts enable optimized output and far less scrap production. When there are multiple variables that need to be trimmed to optimize a process, some systems can handle the multiple inputs and adjust even when interdependence is affected. Tubing extrusion systems now include wall thickness, ovality and even surface quality.
What is the greatest challenge you faced in your professional career?
Czuba: Keeping up with my work load as a consultant and balancing my volunteer activity and home life.
To what do you attribute your success?
Czuba: By staying connected to others and by going to conferences and shows where I walk the floor and talk to exhibitors to find out what’s new. I try to stay open to learning new things. I have a wonderful network of friends and colleagues I stay connected with. SPE is a great way to stay connected.
What do you want your legacy to be?
Czuba: I would like to be thought of as a fun, happy person who enjoys his work and enjoys helping others. I believe in the motto “When you work, work hard; when you play, play hard; and when you pray, pray hard!” I have a wonderful family with a tremendously supportive wife, JoAnn, who is patient beyond belief and three adult children who are all married and now beginning families of their own. We have the blessings of four grandchildren.
Just the facts
WHO IS HE: Len Czuba, president of Czuba Enterprises
HEADQUARTERS: Chicago
FOUNDED: 2001
EDUCATION: Bachelor of Arts degree in biological sciences from Southern Illinois University in Carbondale, Ill.
EXPERIENCE: Czuba has 15 patents and is widely published.
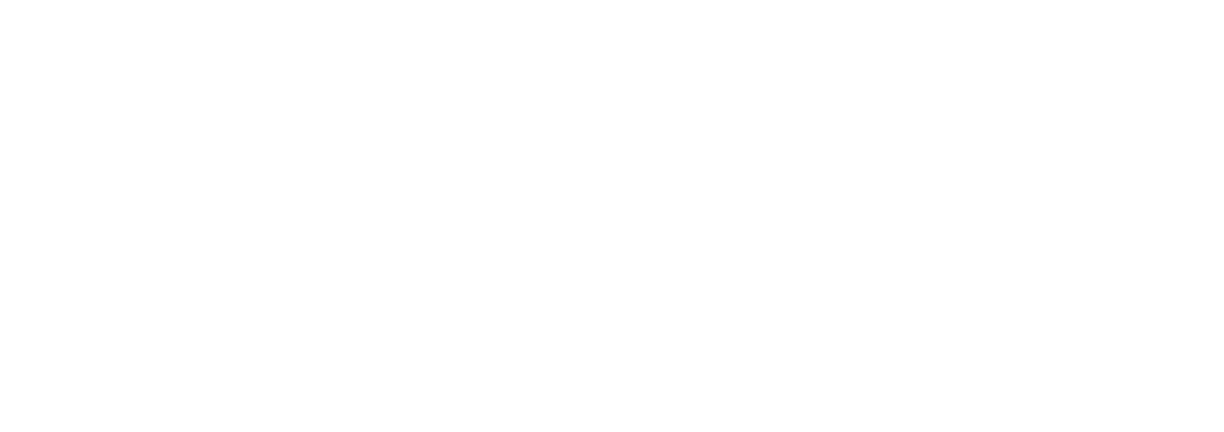