Robot makers emphasize speed, safety, versatility
Speed and safety were among the buzzwords on the show floor of K 2019, as new and upgraded robots strutted their stuff, revealing new levels of sophistication and advanced features. Designed for greater flexibility, versatility and user convenience, the innovations displayed by automation equipment makers Sepro, Wittmann Battenfeld, Brink and AGS Automation provide new options for injection molding machine operators.
Sepro
Sepro is redesigning its popular Success three-axis robot line by adding a two-axis servo wrist, a feature generally found on more expensive and sophisticated robots.
The French manufacturer showed a prototype and announced the Success line redesign at K 2019. The new models — with a two-axis servo wrist co-developed with Yaskawa Motoman — are expected to be available in the third quarter of 2020. The Success line is Sepro’s best-seller.
Sepro also announced a partnership with Universal Robots (UR) that will allow Sepro to incorporate UR collaborative robots in work cells it designs for plastics processors. Sepro does not build cobots.
The Success 22 X model shown at K 2019 had a sleek, streamlined look and featured an extended strip stroke that can sometimes allow a robot to be paired with a higher-tonnage molding machine than currently possible.
Claude Bernard, Sepro’s product marketing director, said the servo wrist “can be easily adapted with simple digital commands, guaranteeing greater flexibility and faster production changeovers. We believe this represents the future of Cartesian robots.”
Bernard said that compared with a three-axis robot with a pneumatic wrist, Success Line X robots will be able to adapt more easily for quick mold changes, secondary operations and other situations requiring flexibility. He said the sensors in the wrist servo motors will allow the robot to know exactly where its wrist — and attached grippers — are positioned.
Success Line X robots will be able to move along all five axes at the same time. Bernard said this makes it easier for the robot to extract a large, complex part with minimal clearance between mold halves and tie bars, or to position parts for secondary operations.
Complex part-manipulation tasks have traditionally required a six-axis articulated robot. But Bernard said the five-axis Cartesian robot will be faster getting in and out of the mold, which will reduce cycle times.
He said setup and operation are intuitive and especially designed for injection molding operations.
The redesigned line will use cam follower bearings for linear motions. Sepro patented cam follower bearings several years ago that handle heavier loads and longer strokes on larger robots. They provide more-even weight distribution and smoother operation than linear bearings on the current three-axis Success robots.
In another development, Sepro officials explained that they are not becoming a comprehensive distributor of UR’s cobot products but can now include them in automation solutions, where appropriate. Sepro regularly designs automation systems for molding cells that include multiple robots, specialized end-of-arm tooling (EOAT), feeders, inspection devices, secondary operations, box-filling automation and other equipment.
Bernard said that “cobots are perfectly adapted to peripheral operations that require human-machine interactions increasing in demand in the plastics industry. By combining’s Sepro’s experience in plastics molding with the collaborative technology of Universal Robots, we can offer our customers even greater flexibility and performance in these systems.”
Wittmann Battenfeld
Wittmann Battenfeld launched a new robot series, added models to its Primus robot line and upgraded its R9 TeachBox controller with wireless technology.
The company introduced the first three models of its new Sonic series of ultra-high-speed parts-removal robots: the Sonic 131, Sonic 142 and Sonic 143, for use with injection molding machines with clamping forces from 165 tons to 550 tons.
The Sonic 131 has a payload of 6.6 pounds, the Sonic 142 payload is 15.4 pounds and the Sonic 143 payload is 11 pounds.
Sonic robots can be used for parts removal with cycle times as fast as 4 seconds. Gripping times faster than 1 second also improve productivity for tasks other than parts removal.
The series offers safer parts removal with a feature that only allows the mold to close if all parts remain in the gripper. The robots can also count and stack parts in containers.
To facilitate movement in and out of the mold area, the electric and pneumatic power supplies for grippers are located inside the vertical axis. Gripper valves and inlets are seated directly on the vertical axis to speed up response time.
The wiring for communications between the robot and end-of-arm tooling is inside the Y-axis.
Wittmann said Sonic robots have acceleration rates of 213 feet per minute squared.
Wittmann also introduced two Primus series robots at K 2019, the Primus 16T and the Primus 48, which also has a telescoping version, the 48T.
The Primus 16T is based on the 2-year-old Primus 16. The Z- and X-axes are the same, but the 16T has a telescoping Y-axis. It is designed for use in confined spaces.
Payload for the Primus 16T is 11 pounds, which lets it safely handle the large grippers needed for molds with six or eight cavities.
The Primus 48 and 48T are designed for use with injection molding machines with clamping forces ranging from 550 tons to 1,323 tons.
The robots’ maximum horizontal stroke is 29.5 feet. This means that the robot can access several pallets arranged beside the molding machine. The demolding axis has a maximum stroke of 47 inches and the vertical range is from 55 inches to 78.7 inches. Load capacity is 44 pounds.
Wittmann upgraded its R9 TeachBox robot controller with wireless technology.
For years, Wittmann has offered its standard TeachBox as a separate operating terminal with a cable connection to the robot’s control system. This offers the operator the ability to operate the robot from a safe distance.
However, with the standard cable connection, the operator’s maximum range from the robot was limited by the length of the cable. Longer cables could be used, but those might interfere with travel paths. The cables can also become damaged or present trip hazards, the company said.
The R9 WLAN TeachBox is designed to solve those problems by eliminating the wired connections. Safe data transmission occurs through radio transmission, combined with an active link to the base station.
Wittmann said it uses an isolated, safe protocol to transmit data.
Brink
The injection molding machine produced a 250-gram, square food container in an eight-cavity mold with a 3.9-second cycle time.
At the end of the year, about 10 of the company’s customers operated the machine during a benchmark testing period, according to Max Zinnemers, international sales manager for Brink. The new system is an upgrade of the company’s Standard IML system, which also was operating at K 2019, on a Stork Food-Line 4400 injection molding machine.
While both systems feature fast, high-precision robots with servo-driven motors, the Versatile IML system offers several improvements over the Standard IML system.
“The Versatile IML is meant to be versatile for customers who use more than two different products on one injection machine,” Zinnemers said. It is possible to run multiple labels on one Versatile IML system when those labels are applied from the same side.
The Versatile IML is compatible with IMMs producing a round container with a wrap-around label in a two-cavity mold; a square container with a five-sided label in a four-cavity mold; a duo cup with a wrap-around label and a bottom label in a six-cavity mold; and lids with a top label in an eight-cavity mold, he said.
“Any other example that you can imagine is possible as long as the labels fit in the drawer size of 1,000mm by 1,000mm,” he said.
The magazine on the Versatile IML includes two drawers, so one drawer can be refilled with labels without stopping production. The drawer that is fully stocked will automatically replace the empty drawer without any operator intervention.
The Versatile IML includes a camera monitoring and correction device. The machine automatically adjusts labels that get out of alignment, he said.
It corrects itself by measuring the dimensions on the part and adjusting as needed, Zinnemers said.
AGS Automation
AGS Automation Greifsysteme Schwope GmbH, Bergisch Gladbach, Germany, has developed a new series of arms that affix end-of-arm-tooling (EOAT) to robots that remove parts from injection molding machines.
The lightweight, spring-loaded gripper arms are made entirely of aluminum. They are used in combination with vacuum cups or sprue grippers.
The vacuum cups screw directly into the head of the gripper arms. Sometimes, suction cups must be adjusted to different angles to provide an optimal grip, so the company offers a version with an adjustable head.
For use with sprue grippers or gripper fingers, the company offers a model with a prism clamp.
In certain applications, it is important that the gripper arm not rotate. The shaft of the gripper arm contains four grooves with ball bearings inside that prevent rotation.
“If we use, for example, an oval vacuum cup for an elongated part, the vacuum cup should not rotate,” AGS GM and CEO Marc Schwope said.
AGS offers the gripper arms in diameters of 10mm, 14mm and 20mm diameters; each size is capable of both short and long linear strokes.
Separately, AGS has developed a way of quickly changing EOAT. It now offers grippers with bases that have hole patterns that accommodate an ISO flange; ISO flanges are a standard way of mounting EOAT on six-axis articulated robot arms. The flanges include screw holes and a pinhole that serves as a rotation lock.
AGS grippers now can be mounted directly onto the robot, whereas in the past, grippers needed an adapter that fit the robot flange, Schwope said. Schunk distributes AGS products in the U.S.
Contact
Brink Group, The Netherlands, 31-318-452500, www.brinkbv.comSchunk Intec Inc., Morrisville, N.C., 919-572-2705, www.ags-automation.de/en/
Sepro America LLC, Warrendale, Pa., 412-459-0450, www.sepro-america.com
Wittmann Battenfeld Inc., Torrington, Conn., 860-496-9603, www.wittmann-group.com
Bruce Geiselman
Senior Staff Reporter Bruce Geiselman covers extrusion, blow molding, additive manufacturing, automation and end markets including automotive and packaging. He also writes features, including In Other Words and Problem Solved, for Plastics Machinery & Manufacturing, Plastics Recycling and The Journal of Blow Molding. He has extensive experience in daily and magazine journalism.
Ron Shinn | Editor
Editor Ron Shinn is a co-founder of Plastics Machinery & Manufacturing and has been covering the plastics industry for more than 35 years. He leads the editorial team, directs coverage and sets the editorial calendar. He also writes features, including the Talking Points column and On the Factory Floor, and covers recycling and sustainability for PMM and Plastics Recycling.
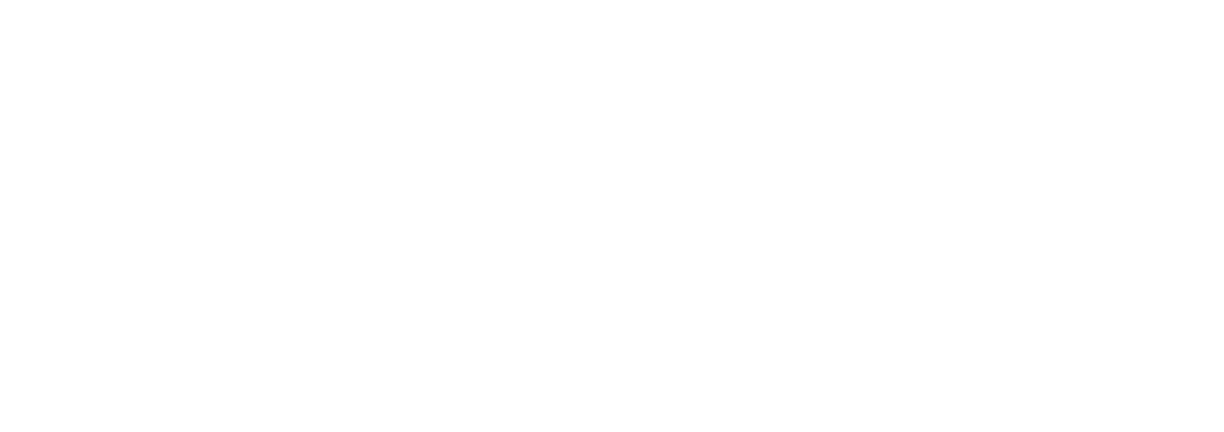