Companies celebrating the debut of new technologies turned the switch on for electric presses that churned out everything from wine glasses to cheese containers at K 2019. Among the companies taking part in the festivities were Haitian, Wittmann Battenfeld, Chen Hsong, Nissei and Stork.
Haitian
Haitian’s new Third Generation Technology includes updates on two electric IMMs — the all-electric Venus III and the Zeres III, an electric machine with hydraulic circuits for certain functions. Both machines will be available in the U.S. and Canada in the second half of 2020, the company said.
The primary difference between the two machines is that the Zeres III features an integrated hydraulic drive system to operate core pulls, ejectors and valve gates so machine users don’t have to use an auxiliary hydraulic power pack. The Zeres III series also offers larger clamp tonnages.
“Many custom molders run various parts and molds and they need a more flexible machine for things such as core pull,” said Glenn Frohring, president and co-owner of Absolute Haitian, which is the official U.S. and Canadian distributor for China-based Haitian. “The Zeres III provides them with a broader range of processing options.”
The Venus III will be available with clamping forces ranging from 45 tons to 899 tons. The Zeres III will be available with clamping forces from 45 tons to 1,551 tons. Most of the Series III machines have more distance between tie bars to accommodate larger molds than the Series II machines.
Also, compared with their predecessors, most of the Series III machines will be slightly shorter in length. Size differences range from about 4 inches on smaller machines to 3.3 feet on the larger machines. This provides more room for auxiliary equipment.
Compared with their Series II predecessors, the Series III machines feature upgrades to their clamp units, injection units and controllers. The improved clamp design on the two Series III machines reduces dry cycle times by 10 percent and better protects the mold, the company said.
The new design of the electric injection units enables them to better match a range of machine sizes and makes it possible for them to be used on larger machines. The injection units move on linear guides, reducing friction. Features of the units include precise repeatability and injection speeds of up to 500mm per second. The units are available in one-spindle, two-spindle and four-spindle versions. Units with greater numbers of spindles can better accommodate larger shot sizes and parts. Depending on the size of the clamp, users can select from between one and five different injector unit sizes.
The one-spindle version is compact, with the spindle and screw arranged in a line. It is designed for precision and efficiency and can be used on injection unit sizes ranging from 50 to 1,700. The two-spindle version features synchronously placed servo motors and symmetrical injection for correcting carriage movement deviations. It is designed to maintain parallelism to prevent premature wear on the injection unit. Two-spindle injection units are available in sizes ranging from 2,250 to 9,200. The four-spindle injection units feature multi-axis control technology based on servo torque direct drives. Intelligent algorithms enable the precise synchronization of all drives to allow for a fast response time. They are available with injection units ranging from 12,800 to 22,800.
In addition to the new features on the updated machines, Haitian’s Third Generation Technology offers Connectivity Plus, a software feature designed to make the machines compatible with a wide range of automation options.
The Third Generation Technology also includes improved performance through Motion Plus, a combination of hardware and software designed for intelligent motion control, such as the precise movement and adjustment as needed of the clamp or injection unit.
At the K show, a Venus III equipped with an eight-cavity mold produced syringe plungers for the medical industry out of PP. The shot weight was about 12.7 grams and the cycle time was 11 seconds.
A Zeres III at the show was equipped with a four-cavity mold and in-mold labeling equipment. It produced lids for 250-milliliter containers out of PP. The shot weight was 24 grams and the cycle time was 4.8 seconds.
Wittmann Battenfeld
Wittmann Battenfeld extended its line of EcoPower all-electric injection molding machines by adding models with clamping forces of 440, 496, 550 and 606 tons. The EcoPower line of IMMs was introduced in the U.S. in 2017 and now includes 11 machines with clamping forces ranging from 60 tons to 606 tons.
Like the previous versions of the EcoPower, the latest sizes have servo motors to drive the main movements (closing/opening, plasticizing and injection) and make mold height adjustments. The ejector, nozzle stroke, contact pressure and core pulls are driven by an integrated servo-hydraulic unit powered by a servo-electric motor with a fixed-displacement pump. Direct servo-mechanical drives are optional.
The injection units are equipped with a twin-drive system for injection and dosing. A torsion-resistant, one-piece cast-iron frame with linear guides is designed for precise movements.
The EcoPower clamping unit is a three-platen/four-tie-bar system with a five-point toggle lever driven by a servo motor. The platen travels on linear guides and roller bearings without contacting the tie bars. Injection can begin while the machine builds up clamping force.
The company’s patented energy-recovery system converts kinetic energy released by braking into electrical energy, which is used to heat the barrel. This reduces the machine’s energy consumption by up to 5 percent, the company said.
The moving platen guide system produces little friction, protecting the mold. The system measures force changes inside the drive, and, if the force is excessive, the system reduces the force, which also protects the mold.
The new IMMs feature the Unilog B8 control system to simplify operations. The industrial PC is equipped with a large touch-screen operator terminal. The screen is the interface to the Windows 10 Internet of Things (IoT) operating system for process control.
The machines are compatible with Wittmann 4.0, a uniform data-transfer platform between IMMs and auxiliary equipment.
Chen Hsong
Taking the spotlight for Chen Hsong were three machines in its brand-new Spark series. They include the SM100-Spark with a clamping force of 110 tons, the SM180-Spark with a clamping force of 198 tons and the SM230-Spark with a clamping force of 253 tons.
All three machines debuted in the U.S. and Europe this year, according to H.L.A. Corbey, GM of Chen Hsong Europe.
Spark-series machines feature “all adapt,” which is a package of technologies that enables them to manufacture a wide variety of parts, ranging from ultra-thin-wall packaging made at high speeds to thick-walled parts made at high pressures.
“This is made possible by high-end algorithms running in a high-speed computer controller, using data obtained from high-speed digital transducers, allowing the machine to adapt dynamically to the actual molding process in real-time,” Corbey said. This allows the machine to automatically adapt to various production requirements in milliseconds, he said.
The series features an auto stress-release system (ASRS) that monitors the state of the injection screw during the injection process. It works with a patented stress-release mechanism to make adjustments in real-time to minimize stress buildup in the part, which is a common cause of out-of-spec parts. “This is made possible by highly advanced algorithms [that are] fed high-precision, real-time data from high-end transducers running on very high-speed CPUs on the intelligent controller,” he said.
The machines also feature algorithm cross-protection, a patented electronic technology that smooths out mechanical shocks and vibrations to protect the mold during high-speed clamping. Similar to the ASRS, the system monitors and adjusts the ball screw driving the clamping axis, buffering the hydraulic circuit and creating a smoother movement, Corbey said. “It works together with the floating-point toggle design, resulting in high-speed, silky-smooth mechanical movements without shocks or noise.”
Nissei
Nissei introduced its NEX-V series machine, a concept model that is still being developed and will be sold globally in 2020. It is the fifth generation of the NEX series and will succeed the current NEX-IV series that was released in May 2016. More than 20,000 NEX-series units have been sold, the company said.
The new series will include a new controller that communicates with IoT technologies and will offer enhanced quality and production management and maintenance features to monitor data and show operating history, the company said. It will be OPC-UA compliant and meet Euromap 77 and 88 standards. Additionally, the controller will be designed so that it can be used in conjunction with an MES, and will be able to manage auxiliary equipment, including take-out robots, material feeders and mold temperature controllers. The touch screen on the control panel will be water- and dust-resistant.
The toggle-type clamping mechanism, which achieves fast cycle times, was carried over from the Series IV machines. Its time-tested flat clamping mechanism has a twist-resistant structure and offers uniform contact pressure. Standard linear guides provide precise clamp linearity, which prevents flash and other molding defects, the company said. They also contribute to longer mold and clamping unit life. The wear-resistant toggle and linear guides reduce the need for greasing.
Nissei exhibited two NEX280V-71E models. Using 100 percent biodegradable polylactic acid (PLA), one molded the base of a champagne flute, while the other molded the transparent thin-walled champagne glass. Carbon dioxide was injected into the molten (PLA) to improve the fluidity of the injected material. The glass was made in an eight-cavity mold with a 37-second cycle time and a shot weight of 185 grams. The base was made in a four-cavity mold with a 72-second cycle time and a shot weight of 108 grams. The glass was 0.65mm thick and the base was 0.74mm thick.
Stork
The gearbox has a new compact design with four gears instead of two. The electric motor is oriented vertically instead of horizontally, making the machine more compact. The toggle system was optimized for faster machine movements.
A new design of the tie-bar nut provides for enhanced load distribution over the thread passages. The size of the tie-bar thread has been increased.
Toggle pins are now clamped to provide better stability. “This provides for less overall wear and the possibility for faster and more accurate movements,” said Wim Brinkman, a Stork salesman at K 2019.
The screw also is clamped, similar to the toggle pins, to provide the same benefit.
Updated software reflects continuing additions and improvements to the Stork Services 4.0 initiative, which provides enhanced energy management, remote diagnosis and connection to a support desk.
The Food-Line 4400 at K 2019 was producing a 1.5-liter feta cheese container from a two-cavity Brink mold in a 3.9-second cycle time. The manufacturing cell included the Brink Standard IML system and robot take-out system.
The Stork Food Line has clamping forces ranging from 169 tons to 1,236 tons.
Bruce Adams, senior reporter
Contact
Absolute Haitian, 216-452-1000, Parma, Ohio, www.absolutehaitian.com
Wittmann Battenfeld Inc., Torrington, Conn., 860-496-9603, www.wittmann-group.com
Chen Hsong, CH-America, Torrington, Conn., 860-840-7070, www.chenhsong.com
Nissei America Inc., Anaheim, Calif., 714-693-3000, www.nisseiplastic.com
Stork Plastics Machinery BV, Hengelo, The Netherlands, 31 74-2 405000, www.storkimm.com
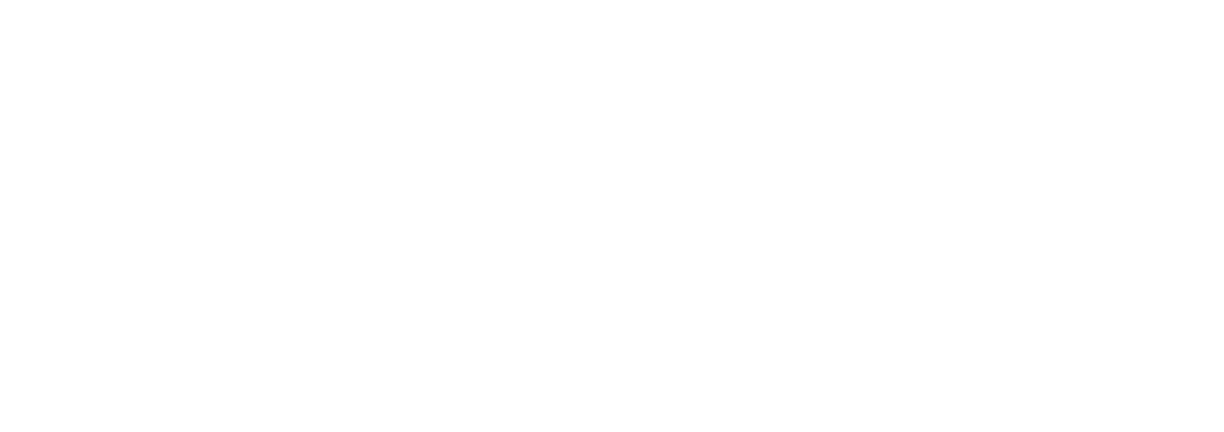