Problem: Huhtamaki needed to increase production of its popular Chinet-brand plastic plates without increasing the size of its Ohio manufacturing plant.
Solution: The company installed an integrated robot and automation system on one injection molding machine that increased production 50 percent without expanding the plant’s footprint.
Huhtamaki North America is a leader in advanced packaging and disposable tableware made of plastic, shaped paperboard and molded fiber. Products include consumer packaged goods, cups, containers and trays for the food- service and retail markets.
The company’s global parent company, Huhtamaki, is based in Espoo, Finland, and has 79 manufacturing facilities and 24 sales offices in 35 countries.
Huhtamaki works with CBW Automation, which supplies robots and automation systems with a focus on injection molding and thermoforming applications in the packaging and medical sectors.
“We’ve had a good long-term relationship with CBW,” said Mike Drake, senior process engineer at the Huhtamaki plant in New Vienna. “They specialize in our market: thin-wall packaging [made by] injection molding. They are a pioneer in the automation of this specific niche. I’ve been with the company since 1990, and legend has it that the business relationship goes back to the 1970s.”
So, after purchasing a larger cavitation stack mold to increase production of its Chinet-brand plastic plates, Huhtamaki worked with Taras Konowal, the director of sales and marketing for both CBW Automation and the Mold & Robotics Group, CBW Automation’s parent company.
CBW Automation customized one of its Beeline B-series B2X side-entry, stack mold retrieval robots to work with an improved automation system that Huhtamaki developed for one of its injection molding production lines. The robot operates with a three-axis telescoping arm with tooling attached to its rotation axis. It removes plates from the injection molding machine and stacks them on a conveyor. The custom conveying system connects the shrink wrapper, label applicator and accumulation table. It transports the plates to be shrink-wrapped and labeled. Then, employees manually pack them.
“It is a high-speed retrieval system that brings the plates out and lays them down on a stack belt, and the stack belt conveys them to a dual-sleeving system that does a shrink wrap around the stack and puts a pressure-sensitive label on the top,” Drake said. “It is a high-end-type label with high-resolution graphics.”
Having two shrink-wrap systems, each with a label applicator, ensures that the production line can keep running even during interruptions such as roll changes.
“There are two high-volume shrink-sleeve stations, so when we do SKU changes or a roll sleeve change, we can switch to the secondary sleeving line and keep the molding machine in production,” Drake said.
Installing an automated packaging system with that capability was a key company objective, he said. The injection molding machine produces round, cut-crystal 7-inch PS plates, and the packaging system groups different-size plates into stacks of eight, 10, 12, 25 and 32 plates.
“That was a big plus with this production line,” Drake said. “We can continue to produce when changing the sleeve material or changing the SKU or the stack count. We can do all those changes without having to shut down the molding machine. We did not have that feature in our previous equipment.”
As a result of these improvements, Huhtamaki increased output on the production line by 50 percent without taking up any additional space, Drake said. The speed of the robot, conveying system, and dual-packaging station allow the injection molding machine to keep running, whereas the press previously had to stop to allow the downstream system to catch up.
“The robot used for the plate takeout has a low intrusion time, so it gets in and out very quickly,” Konowal said. “It let them go to a bigger cavitation, which increased their volume dramatically. They have a large system that moves the plates away from the injection molding machine, so they can do the packaging in-line. Two shrink-sleeve stations allow them to keep up with the machine’s cycle time.”
The stacked and shrink-wrapped products are manually loaded into boxes and put on pallets for shipment.
The system was installed in March and training was completed in a couple of days, according to Drake. “We have other automated CBW equipment due to our history with them, so training went smoothly,” he said.
Bruce Adams, senior staff reporter
Contact:
CBW Automation Fort Collins, Colo., 800-229-9500,
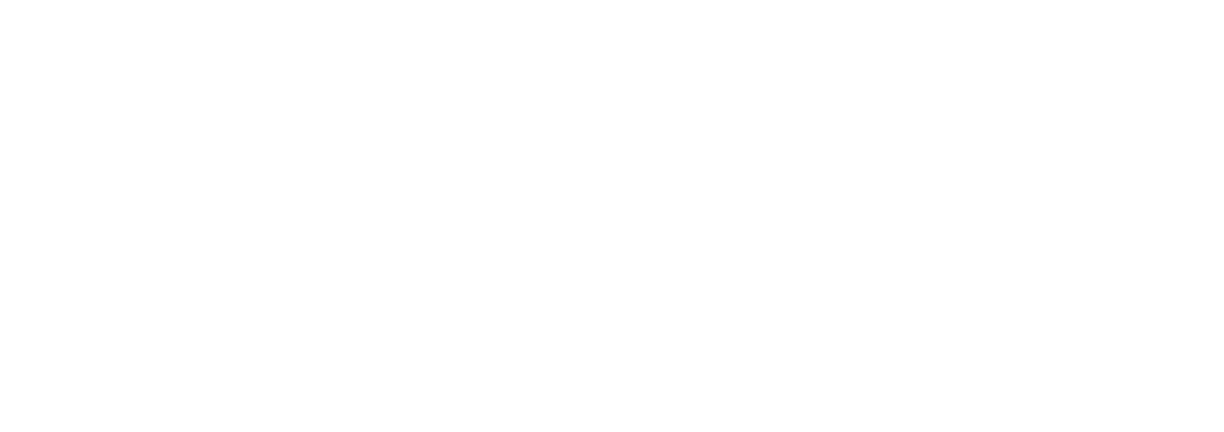