Each modular, air-cooled chiller in the 3FR line has a single refrigeration circuit, a high-efficiency Bitzer screw compressor, digital controls and an air-cooled condenser.
While each 3FR chiller is designed to be located inside the plant, its matching 3CR air-cooled condenser is installed outside — a configuration known as a split system — which reduces the equipment’s footprint on the factory floor, compared with systems that could be located entirely inside the plant. The split-system condensers are made for harsh outdoor conditions and feature stainless-steel frames and heat-exchange coils made from copper tube and aluminum fins, the company said.
Split-system chillers’ benefits go beyond their small indoor footprint, according to the company. Air-cooled chillers use ambient air to remove heat from process water. They can be located entirely outside a plant, but, when installed in that configuration in cold climates, packaged air-cooled chillers — with the compressor, evaporator and condenser in one unit — require glycol to keep the process water from freezing. In a split system, only the condenser, which contains refrigerant, not water, is outside.
“With a split system, the water stays inside the building, and there is no need for glycol,” Frigel marketing manager Al Fosco said. Glycol is “messy, especially during mold changes, expensive, and the glycol cannot be discharged to drain.
The digital controls perform self-diagnostics and can be operated remotely.
The 3FR line’s benefits include decreased cooling times, flexibility and an industry-leading energy-efficiency ratio, the company said.
The plug-and-play chillers, which came out this summer, are appropriate for injection molding, blow molding, blown film production, sheet casting and film extrusion.
Each unit’s screw compressor features variable- capacity modulation. An optional inverter drive offers continuous modulation from 25 percent to 100 percent, automatically adjusting to cooling load demand and saving energy under variable-load conditions.
Every chiller is factory-tested prior to shipment and comes with refrigerant. Chillers include isolation valves and flanges for quick and inexpensive installation.
Kathy Hayes, copy editor
Contact:
Frigel North America Inc. East Dundee, Ill., 847-540-0160
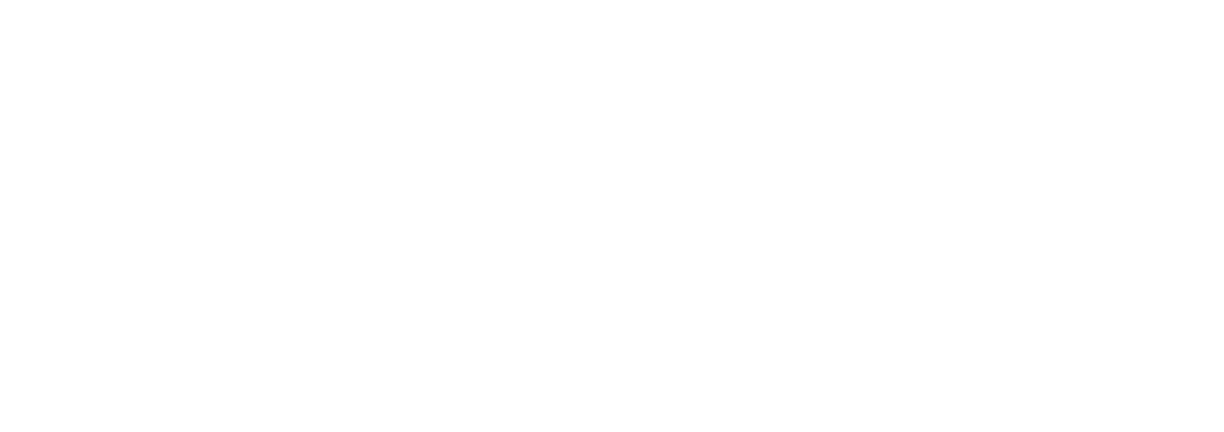