Problem: Band heaters on injection presses were slow to heat up, wasting money and creating an uncomfortable work environment.
Solution: High-efficiency radiant barrel heaters dramatically reduced machine start-up times, saving money and keeping employees cool.
Payback periods on industrial equipment investments are usually calculated in years, based on expected benefits. It’s not often that a plant will see a complete return on its investment in less than a year, but that’s what Pelican Products is expecting to achieve at its Torrance, Calif., injection molding plant.
The company invested approximately $95,000, including $10,000 in installation costs, to outfit the machines, which have clamping forces ranging from 600 tons to 1,800 tons, according to Gabe Guerra, director of manufacturing operations. Pelican expects to achieve annual savings of $80,240 by using 412,013 fewer kilowatt hours to heat those 10 machines. The company also is eligible to receive $44,112 in incentives from Southern California Edison, its utility company, for investing in energy savings, he said. That equates to a first-year savings of more than $124,000 on a $95,000 investment.
“We could have started by installing the TCS on only one machine and received a much smaller incentive, but we recognized that the larger our spend, the larger our savings and the larger the incentive,” Guerra said. “It made a lot of sense on paper, now we just need to confirm that we are getting the savings that we expect.”
Rex Materials installed the heaters on one machine per week for 10 weeks during planned weekend shutdowns, so production was not affected.
“The installation was smooth, and it was a seamless transition,” Guerra said. “All the new heater bands were installed by April 2019, and we already are noticing substantial savings on our energy bills.”
The company manufactures protective cases, temperature-controlled packaging and weather- resistant flashlights used by several industries, including the military, law enforcement, fire safety and entertainment sectors. Pelican has six manufacturing locations in North America, Europe and Australia; three of those are in the U.S. It operates in 26 countries with 24 international sales offices.
Ken Van Nimwegen, global sales manager at Rex Materials, said that injection molding machines with clamping forces of 300 tons or larger are ideal for the company’s TCS radiant heaters.
“The smaller machines don’t use as much energy, but there are other factors to consider,” Van Nimwegen said. “If companies run a high flow rate with quick cycle times, they are melting more plastic and they need more energy. It’s more about the energy used for heating than the tonnage of the press.”
In addition, available space on and around an injection molding machine can be a limiting factor.
“The bigger machines have a lot more space to work on,” Van Nimwegen said. “We need 3.25 inches around the entire circumference of the barrel to install the TCS. Smaller machines have more interference, like the nozzle shut-off valve. It is a combination of needing extra space for installation and the energy consumption that makes machines above 300 tons the better range.”
The biggest benefit of the TCS is its ability to retain heat on the injection molding machines, which improves machine productivity, according to Guerra.
“When a machine goes down for a color change, a mold change, maintenance or for whatever reason, you have to cut the power and you start losing heat,” Guerra said. “When you start the machine back up, you have to wait for the band heater to come back up to temperature. Then, you can restart production.
“We would lose anywhere from 10 to 25 minutes every time a machine went down. With the radiant TCS heaters, everything is insulated, and you are not losing much heat. Now we only lose a minute or two and the heat is back up to where it was when we shut the machine down. If you shut it down for four hours or overnight, you will have to wait longer for it to heat back up, but not as long as if we had to wait for the band heaters. The TCS offers a production efficiency gain.”
Van Nimwegen said Rex Materials conducted a controlled study to determine theoretical heat flow to the melt and to the surrounding area for traditional heater bands and for TCS barrel heaters. The study found that 25 percent of the energy being produced by heater bands goes into the melt and 75 percent goes into the environment. For TCS barrel heaters, the study showed that 80 percent of the energy being produced goes into the melt while 20 percent goes into the environment.
TCS also improves safety because operators are less likely to be burned if they accidentally touch the unit. Traditional heater bands allow more heat to escape, creating touch hazards and hot working conditions.
“There is a safety factor, where if somebody puts their hand on a traditional heater band, it is 500 degrees and you will get burned,” Guerra said. “We shield operators from that by covering the barrel so that doesn’t happen. With TCS, I can place my hand on the heater while the machine is running and it is only about 80 or 90 degrees. You could never do that with the old heater bands.”
At press time, Pelican had not yet used the TCS radiant heaters during summer months, but Guerra has great expectations about their performance.
“There is a lot of radiant heat that comes off the traditional heater bands,” he said. “When it is 90 degrees outside, it is 100 inside with all the heater bands sending off ambient heat. When summer comes, we won’t feel that additional heat that we’ve felt in the past because TCS contains the heat.”
Bruce Adams, senior staff reporter
Contact:
Pelican Products Inc.,
Torrance, Calif., 310-326-4700, www.pelican.com
Rex Materials Inc.,
Howell, Mich., 404-558-1653, www.rexmaterials.com
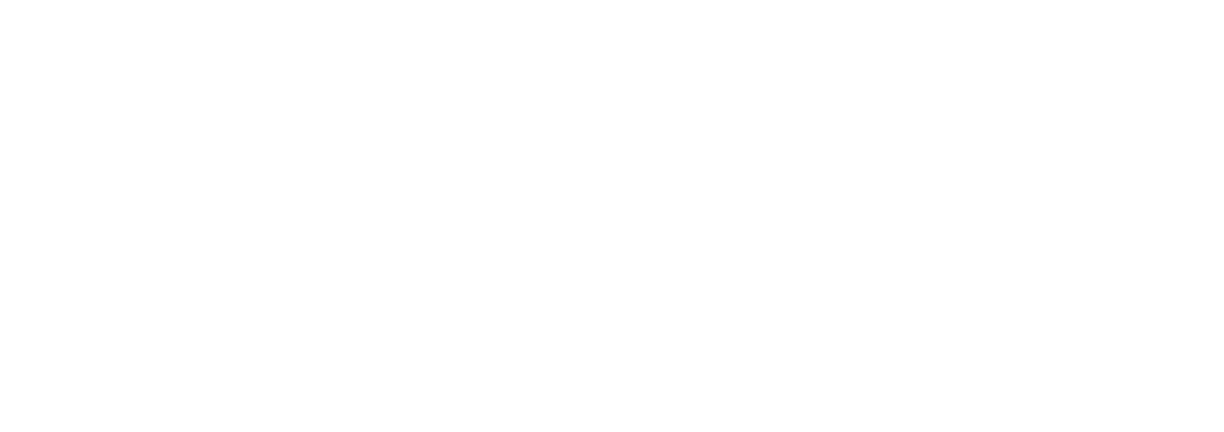