Structural foam molding is the bailiwick of 20/20 Custom Molded Plastics Ltd. The company's already-sizeable manufacturing footprint will nearly double this year at its site in Holiday City, Ohio, about 15 miles from the Indiana border. When all is done, the company will occupy 400,000 square feet, including its manufacturing space, offices and some room for warehousing.
Structural foam molding is a low-pressure form of injection molding. It uses most thermoplastics, including post-consumer regrind, to mold rigid products with thicker walls and higher stiffness-to-weight ratios than standard injection molded products.
The company's seven foam molding machines are state-of-the-art. All of them are from Uniloy Milacron, including four 500-ton, one 1,000-ton and two 1,500-ton machines.
The company also performs high-pressure injection molding with all of the primary equipment supplied by Cincinnati Milacron. There are three 375-ton presses, one 725-ton press and one 2,600-ton press. 20/20 plans to add more as soon as it can get an order placed. Every machine has its own robot, which wasn't always the case.
"I have never been a proponent of robotics but every one of our machines has a robot on it," said President Ron Ernsberger. Ranger Automation Systems Inc., Shrewsbury, Mass., which supplies the company's Cartesian robots, is largely responsible for Ernsberger's change of heart. When 20/20 was hesitant to adopt robots, Ranger offered to equip a single machine with a robot to see how it performed.
"We allowed them to do that," Ernsberger said. "It's the smartest thing I've ever done."
That was in 2004. Ranger has since supplied seven robots for the structural foam machines and four for the standard injection molding machines. Ranger's model RT-3000S8 dual-offset arm robot is the largest robot at 20/20, and the largest made in the world for this application, said John Campbell, national sales manager with Ranger. There is five-axis motion on each arm with a payload of 200 pounds per arm. 20/20 has three of these running on 1,000 and 1,500-ton wide-platen Uniloy machines.
These robots, along with the model RT-3000S4 for the Uniloy 500-ton, were developed in collaboration with 20/20 to meet the company's needs as a custom structural foam molder, Campbell said.
"These robots are capable of extracting a shot size as large as the press can generate, and pick equally large parts from either the moving or stationary platen, without the need for any mechanical reconfiguration at mold changeovers," he said.
The company runs 12-hour shifts, seven days a week, and the safety and efficiency of the human beings on the floor is key. Robots make those humans more efficient and safer.
"Without robots, many jobs require two operators to walk under the mold and sometimes climb up on ladders to remove the parts," Campbell said. "This presents the risk of injury, which can lead to downtime and workplace disruption." Robots also reduce mold open time and allow running at consistent cycle times, which improves quality and output from the press.
"So the payback from the investment in robots is particularly strong, from reduced labor costs, improved yield, and less risk of injuries," he said.
Ernsberger is focused on eliminating human error and is proud that robots haven't replaced humans in 20/20's factory. But efficiencies have greatly improved. On a 12-hour shift, the goal might be 10 shots an hour, resulting in 120 pieces at the end of that shift.
"But I end up with 114," Ernsberger uses an example of missing the target and rattles off some excuses that can happen with humans. "There are all kinds of excuses. With the robots, the machine knows what you want. It's all tied together. The machine doesn't open and say, 'Where is my operator?' The machine doesn't open and the part is stuck and nobody is there. Today, at 20/20, the machine runs the operator. The operator doesn't run the machine. You must be there to answer the robot, or you are going to get buried in parts. Every cycle is the same. Do we get 100 percent efficiency? We absolutely don't. Dumb things happen. But by adding robots, we increased throughput, we increased efficiencies and we dramatically lowered scrap."
Ernsberger grew up in the grueling world of compression molding in the 1970s, when mixing was done by hand and safety measures were quite lax, if there were any at all. He recounts windows up near the ceiling, similar to skylights, that faced east. When he would start his morning shift, the sun rays coming through the windows would sparkle with star-like material. "That was the fiberglass in the air in there," he said.
He marvels at the innovations in machinery and equipment today.
"It's the hydraulics innovations, it's the electronics, it's the PC controls," he said. "The machines are so advanced. It's just so hard to imagine how we did what we did in the 1970s and 1980s."
Machinery utilization: A formula
Ernsberger and crew are no strangers to what it takes to succeed. As a custom shop, the company can be faced with molding any type of part. There are doghouses, pool ladders, tool boxes, trash containers, totes, portable potties, even caskets and crypts. Imagine the size of those types of products and the injection molding machines and molds required. The philosophy at 20/20 is that the company has nothing to sell but machine time.
"I love the custom business. Custom molding is an opportunity to get in with a company that looks at you as a partner," Ernsberger said. "Every time the phone rings, it's a different drummer. It's a different tune. Every customer's part, in their mind, is the best and the most unique. No matter how frivolous you think that part might be, you have to remember it's important to them."
The goal at 20/20 is 85 percent capacity utilization of the machines. "We think that is 100 percent efficient," he said, continuing on to cite the variables that will affect efficiency. "There are going to be mold changes, insert changes, color changes. There is going to be maintenance. There are going to be days when people don't show up. But after you factor in all of those variables into a 24-hour day, I want to net 22."
The value of machine time
The primary machinery and the support equipment have to be predictable and reliable. Buying the equipment or justifying expansion is related to a carefully configured matrix. The equipment is expensive and an investment means all the components of the pricing structure have to add up.
"We're probably the odd guy out in the industry," Ernsberger said. "I can tell you without hesitation that we price things differently. Over the years, I've watched companies that try to manipulate raw material. They try to manipulate packaging. They play games with labor. They're looking for every opportunity to add profit. Me, too. I am all for that. But we have a piece of the puzzle that we won't negotiate and that is our machine time. Everything about 20/20 when we make our profit is based on machine time. We don't mark up material. We don't mark up packaging. Our customers can furnish that if they want. We don't care. It's a pass-through. So let's say we establish a part today as a $10 part. If material goes up a dime a pound, and that means it becomes an $11 part, that is what it is. If you want to furnish the material, go ahead, we don't care. But material went up and we have no control over that. None. So it needs to float."
Profit and the ability to reinvest would be affected if the part price remained stagnant. Therefore, the price is designed to float on things that 20/20 cannot control.
"But on the stuff we can control, I expect to get better," he said. "I expect to find ways to make it more economical. It's important to us to maintain that machine portion because that's not only where we make our profit, that is where we cover overhead."
ALWAYS HAVING a backup:Systems support
Twenty-one silos on 20/20's property hold the resin that is conveyed to dryers supplied by Una-Dyn Inc., Woodbridge, Va., or hopper loaders supplied by Maguire Products Inc., Aston, Pa. Inside the facility each one of the cells is stand-alone, meaning a problem on Press 1 will not affect Press 2.
All the primary machines are the same brand as are the nitrogen and air compressors. If a compressor goes down, a worker can make a switch and the system is back up and running while the offline unit is repaired.
"Our plant is really put together to be as user-friendly on the floor as possible," said Ernsberger, whose formative years in the industry molded his view toward how workers should be treated. For example, what he wants to avoid is having employees show up for work and just as they get settled in, they are sent home due to an equipment failure that affects the whole plant.
"Now you've made your best effort to get to work and we're going to say, 'Well, the plant is down, you're going to have to go home.' Now what is up with that?" Ernsberger said. "Not only did you lose the rest of your day's pay, you just made every effort to get here and it isn't really the company's fault, but because of a fault in equipment or something, we sent you home."
20/20 also is adamant that its equipment will come from U.S. manufacturers.
"We just prefer to keep our business in the U.S.," said Ernsberger. "I absolutely don't mean that as a reflection on anything. That is just our choice. When you look at the United States and all the hurdles that we have all had, I want to keep my business here."
Angie DeRosa, managing editor
Contact:
20/20 Custom Molded Plastics Ltd., 419-485-2020, www.2020cmp.com
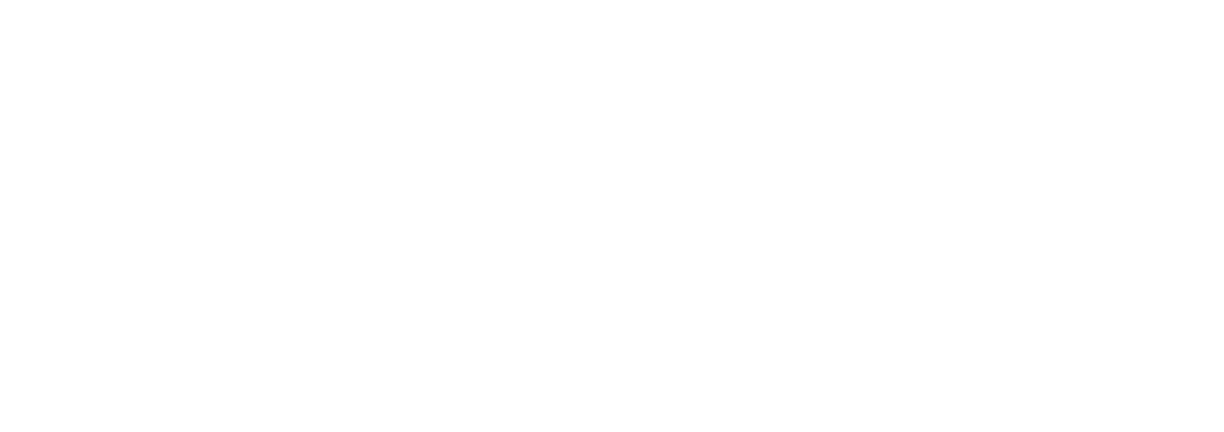