PRD Inc., Springville, Ind., is a custom, tight-tolerance injection molder that has toiled contentedly behind the scenes since its start in 1979. Its bailiwick is lighting components that are
used primarily in the automotive industry molded from highly engineered resins. Located in a rural area just south of Indiana University, the company supplies its components worldwide. Because this is Hoosier country, the fact that the crimson vehicles in the parking lot outnumber cars of all other colors may be more than just coincidence.
PRD may not be responsible for the paint color of employees' vehicles, but President John Passanisi is quick to point out that PRD likely made a lot of their lighting components. The company is a supplier to Tier 1 and Tier 2 automotive suppliers. The products include LED/head and tail lighting; industrial lighting; suspension/handling; window lifts; latch components; HVAC; decorative parts for the interior; and fuel handling. As this lighting grows in complexity and sophistication, so does PRD.
But the automotive market is not the only one to benefit from PRD's diligence and tenacity. The company makes industrial products such as electronics housings, business machine components and impact/noise control products, as well as components.
Beside automotive suppliers, the company's customers include government clients. It even has a government contract for munitions systems. Its municipal applications include LED lighting products, which are growing in popularity due to their energy efficiency.
"It isn't just the cost," says Passanisi. "You don't have to get a guy out there to change the bulbs. We are on the forefront of the LED craze. We got into this business taking on a single project for Ford. PRD took the chance and purchased a 20-ton Toshiba all-electric press. The customer loved the parts so much that the volume increased by 600 percent. PRD showed this part to other customers, and the rest is history."
PRD is a division of Specialty Manufacturers Inc., Indianapolis, which also owns D&M Tool Corp., also of Springville, and Apollo Plastics, Chicago. Specialty Manufacturers purchased PRD and D&M in 1989.
Passanisi has been with the company since 1983. He led Plastics Machinery Magazine's tour of the factory along with GM Mark Murphy. The 72,000-square-foot facility is a modern-day example of a company always transitioning and making upgrades and investments to stay competitive. D&M is located just across the parking lot, a convenient distance because tool changes and tweaks are communicated face-to-face and engineers can follow the progress daily, says Passanisi, who admits that the company has had challenges but overall has had a good run.
"We came out on top during and after the recession," he says. "We had to make some tough choices."
Those choices included reducing the workforce and cutting salaries. PRD also went to a four-day workweek. "The owners explored all avenues of generating cash," says Passanisi. "Every penny was pinched."
Continual improvement
The factory was busy on the day of the tour, and the company now is up to 64 injection molding presses. Of the 64, only 17 are hydraulic. The company is quickly going all-electric, reports Passanisi. The average press is six or seven years old.
"We're trying to keep up with the technology," he says. Murphy says that all-electrics are more energy efficient with greater repeatability and shorter cycle times.
PRD's newest machine is an all-electric, 610-ton Toshiba with a Yushin multi-axis servo robot. This cell is making automotive lens housings and decorative covers.
PRD has been producing different parts for passenger vehicles, including suspension parts produced on a vertical Engel injection molding machine. Its two vertical injection molding presses specifically are used for insert molding.
PRD is evolving and will undergo many changes in the first half of this year. But continual improvement is something that the management and ownership have come to expect, says Murphy.
"We have never been a company that is OK with the status quo," he says. "As a company, we are always trying to find ways to do things better and be more efficient."
Officials are busy with the company's fifth expansion. They are adding 1,500 square feet for a specialty lab that will perform LED testing. That lab is scheduled for completion by the time this article is published.
All told, there are 62 horizontal injection molding machines, with 28 in cell configurations to improve efficiency; 35 have Yushin multi-axis robots and four have servo wrists for added end-of-arm tooling flexibility. The servo wrists are an optional add-on from Yushin. Each cell has its own group leaders and technicians.
Employees are rigorously trained. Sixteen recently went through training with RJG Inc., Traverse City, Mich., and one just completed RJG's Master Molder training.
Over the next several weeks, officials will travel to Italy, where three molds are being produced with compression injection capability. These molds will allow PRD to compress the plastic after it is injected to improve part quality for thick optics.
The molds will be run on one of PRD's new all-electric Toshiba presses. A multistage control mechanism allows the compression operation to take place following the injection process. The plastic is compressed after it is injected into the cavity via compression springs inside the mold.
The injection molding machines and the products they make are under constant evaluation for how they can be improved, officials said. That is illustrated on the tour. Where possible, robotics are being implemented. Passanisi and Murphy pause at a 390-ton, all-electric Toshiba, which has been equipped with a Motoman multi-axis robot that is mounted on top. This robot removes parts from the mold, places them in front of the laser for gate cutting and then puts the finished parts on the conveyor for packing.
"One of our most significant variable cost drivers is our labor cost," says Murphy. "We must keep this cost under control to remain competitive in our markets. Utilizing automation and robotics where feasible helps us accomplish this goal."
Officials have been working steadily to replace aging presses and to create fully automated work cells. At one cell, an operator is centrally located as the machine performs its tasks. The worker gets the part, a lighting component, and inspects it by holding it up to a light table. This is an extra measure put in place for quality control. Officials are trying to go paperless. Everything is becoming standardized with the equipment and all the components needed in a molding cell.
"Everything comes to the operator," says Passanisi as he walks through the area, which is home to 14 injection molding machines, 13 of which are new. The company now uses auxiliary equipment to handle materials that require new high-pressure thermolators reaching up to 356 degrees Fahrenheit.
For finishing and assembly, officials have had to find different ways to perform particular tasks. This includes, for example, finding a way to cut acrylic parts.
"Acrylic shatters when it gets cut, so we had to do it in a different way," says Murphy. The company now uses a laser cutter. The part that is being produced is an LED collimator used in a taillight assembly. For the uninitiated, this is a device that is able to narrow rays of light.
The injection molding press used to make the part is an all- electric 110-ton Toshiba with a Yushin multi-axis servo robot.
Angie DeRosa, managing editor
Contact:
Contact: PRD Inc., 812-279-8885, www.prd-inc.com
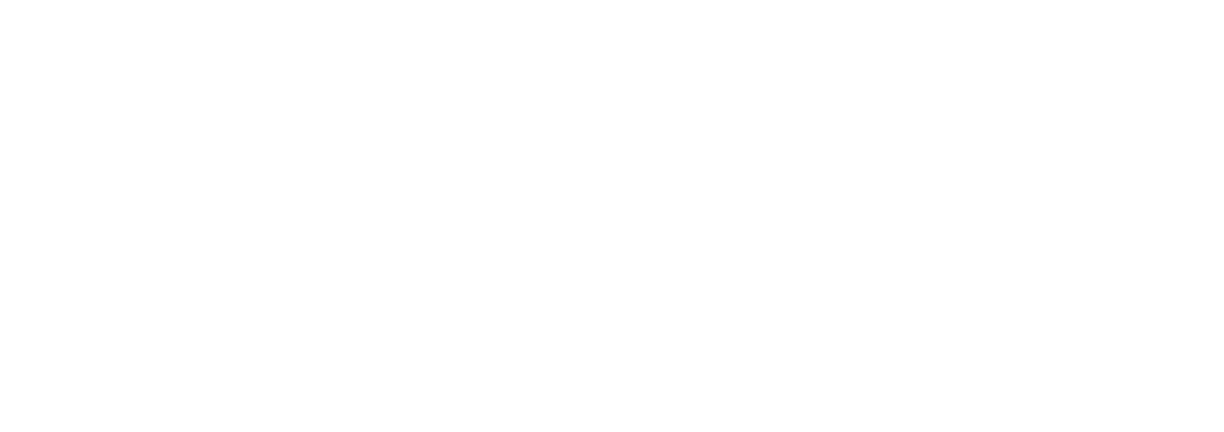